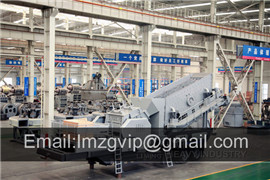
ebook: A Practical Guide to Improving Cement
The ebook gives an overview of cement, the cement production and analysis processes, and the basics about: The quarry, and its role in mining the raw materials, which need to be measured and analyzed. The raw mill and kiln, where
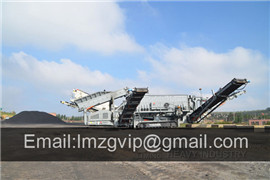
Cement Production an overview ScienceDirect Topics
World total cement production for was about 4.2 billion tons with emerging markets playing a dominant role (IFC, Figure 1 describes the cement manufacturing process. It
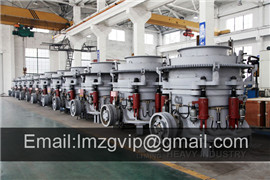
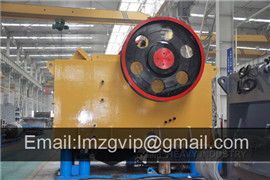
Advances in Cement Technology ScienceDirect
This chapter focuses on refractories in cementmaking. Portland cement is made by mixing together calcareous and argillaceous materials, firing at a temperature of 1300°C to
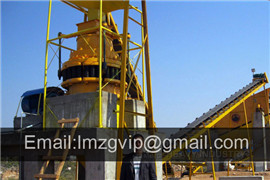
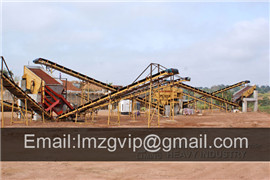
Cement Industry an overview ScienceDirect Topics
The cement manufacturing process involves three components: the mining and preparation of inputs; the chemical reactions that produce clinker; and the grinding of clinker with
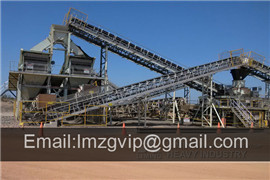
Cement Manufacturing Process Chemical Engineering
The manufacturing of cement generally involves four steps: Mixing; Burning; Grinding; Storage; Mixing: The mixing of raw materials can be done either with

Cement Manufacturing Process: 6 StepsTo Make
6 steps of the cement manufacturing process. When we talked about the manufacturing of cement, anyone who knows the cement manufacturing process slightly will mention “two grinding and one
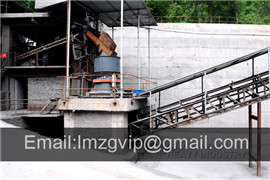
CEMENT MANUFACTURING PROCESS: RAW GRINDING
Dry grinding requires approximately 30 % more energy / wt. of ground material. Dry mills need more mill volume than comparable wet mills. However, the

Cement Manufacturing Process Phases Flow
Cement Manufacturing Process Phase 1: Raw Material Extraction. Cement uses raw materials that cover calcium, silicon, iron and aluminum. Such raw materials are limestone, clay and sand. Limestone
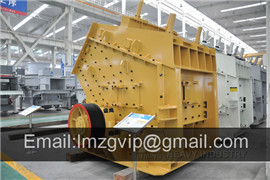
Role of Gypsum in Cement and its Effects The
The mixture then sent to final grinding process. For ordinary Portland cement it remains between 3 to 4% and in case of Quick setting cement it can be reduced up to 2.5%. Role of Gypsum in Cement The main
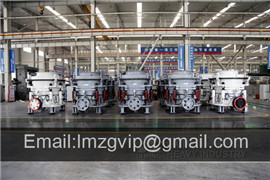
Grinding Machine: Types, Parts, Working & Operations
Working principle of Grinding Machine: The working principle of a grinding machine is quite easier to understand.. In a grinding machine, there is an electric motor
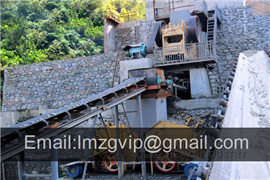
ebook: A Practical Guide to Improving Cement
The ebook gives an overview of cement, the cement production and analysis processes, and the basics about: The quarry, and its role in mining the raw materials, which need to be measured and analyzed. The raw mill and kiln, where adding, feeding, and heating are addressed. The clinker, and the role of grinding, cooling, and
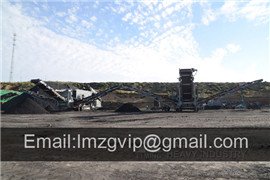
Digitization and the future of the cement plant McKinsey
According to our analyses, the cement plant of the future could reduce emissions by up to 75 percent by 2050 compared with . Around 20 percent will come from operational advances, such as energyefficiency measures and clinker substitution. An additional 10 percent will come from alternative fuels—however, the availability of
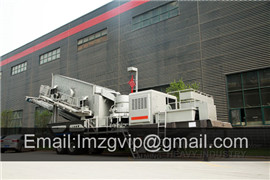
How Cement is Made Cement Manufacturing Process
The cement manufacturing process is a complex one involving several steps. Each step in the process plays an important role in the overall quality of the finished product. In this article, we will describe how cement is made with six cement manufacturing process stages. Cement is conveyed from grinding mills to silos (large storage tanks

Supply Chain Management in the Cement Industry
cement supply chain. First, GrindtoOrder where cement is kept in clicker (intermediate product of the cement manufacturing process) and then grinded as orders appear. Second, PacktoOrder, where cement is kept in bulk and then packed as orders appear. Further research should be made to confirm the feasibility of these alternatives.

Cement Finish Milling (Part 1: Introduction & History)
Although concrete is the most sustainable building material available [1], with over 4 billion tonnes of cement produced and consumed worldwide, optimisation of the grinding process can provide

Materials Free FullText Effect of Particle Size and
Supplementary cementitious material (SCM) plays an important role in blended cement, and the effect of the particle size and morphology of siliceous supplementary cementitious material on hydration should not be ignored. In this study, 0.5 h and 1 h of wet grinding was applied to pretreat iron ore tailing powder (TP), and the
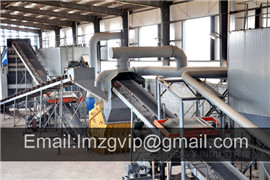
Cements and Cement Additives Structural Guide
In addition, there is much other raw material used in cement manufacturing. Addition of those materials is based on the requirements of the production. Then the Colling process starts. It is cooled with the air, grinding is done to create the cement powder. Gypsum 23% is added as a retarding agent at the final stage of grinding.
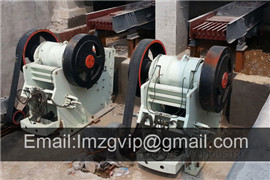
Ultratech Cement Commissions Cement & Grinding Units
With this commissioning the company’s total cement manufacturing capacity in India now stands at 126.95 million tonne per annum," the company said in an exchange filing. UltraTech has 22 integrated manufacturing units, 27 grinding units, one clinkerisation unit, and 8 bulk packaging terminals. It has a network of over one lakh channel
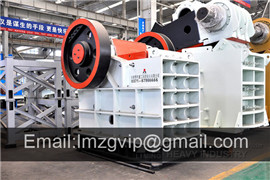
UltraTech Cement scale capacity of greenfield grinding
After this commissioning the company's total cement manufacturing capacity in India is at 126.95 mtpa. UltraTech Cement on Thursday announced the commissioning of 1.30 mtpa brownfield cement
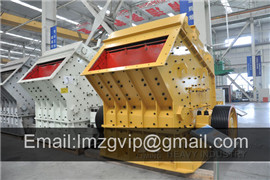
A Review on the Life Cycle Assessment Phases of Cement
8.2.1 Goal and Scope of Cement and Concrete Manufacturing LCA. The goal of carrying out an LCA study of concrete is to state the prophesied use and the reasons for conducting the study. Scope of concrete manufacturing LCA consists of the production systems that are to be studied, the functional unit, system boundaries, and the allocation
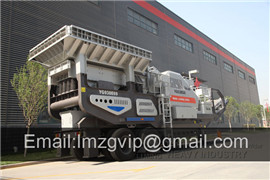
ebook: A Practical Guide to Improving Cement
The ebook gives an overview of cement, the cement production and analysis processes, and the basics about: The quarry, and its role in mining the raw materials, which need to be measured and analyzed. The raw mill and kiln, where adding, feeding, and heating are addressed. The clinker, and the role of grinding, cooling, and
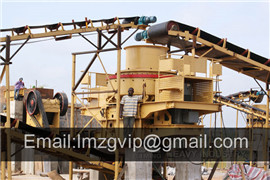
Cement Extraction and processing Britannica
There are four stages in the manufacture of portland cement: (1) crushing and grinding the raw materials, (2) blending the materials in the correct proportions, (3) burning the prepared mix in a kiln, and (4) grinding the burned product, known as “ clinker,” together with some 5 percent of gypsum (to control the time of set of the cement). The three processes of
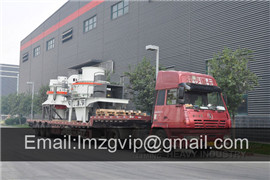
Digitization and the future of the cement plant McKinsey
According to our analyses, the cement plant of the future could reduce emissions by up to 75 percent by 2050 compared with . Around 20 percent will come from operational advances, such as energyefficiency measures and clinker substitution. An additional 10 percent will come from alternative fuels—however, the availability of

Supply Chain Management in the Cement Industry
cement supply chain. First, GrindtoOrder where cement is kept in clicker (intermediate product of the cement manufacturing process) and then grinded as orders appear. Second, PacktoOrder, where cement is kept in bulk and then packed as orders appear. Further research should be made to confirm the feasibility of these alternatives.

2 Process Of Manufacture Of Cement Civil Giant
Wet process. Dry Process of Manufacture of Cement: Crushing of limestone and clay in crushers and stored in silos. Grinding of crushed materials and storing in hoppers. Mixing of materials by compressed air in the right proportions to form a raw mix. Burning of raw mix in a rotary kiln to form clinkers.

Cements and Cement Additives Structural Guide
In addition, there is much other raw material used in cement manufacturing. Addition of those materials is based on the requirements of the production. Then the Colling process starts. It is cooled with the air, grinding is done to create the cement powder. Gypsum 23% is added as a retarding agent at the final stage of grinding.
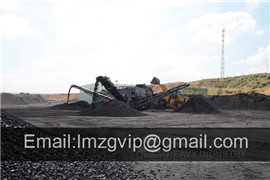
Materials Free FullText Effect of Particle Size and
Supplementary cementitious material (SCM) plays an important role in blended cement, and the effect of the particle size and morphology of siliceous supplementary cementitious material on hydration should not be ignored. In this study, 0.5 h and 1 h of wet grinding was applied to pretreat iron ore tailing powder (TP), and the
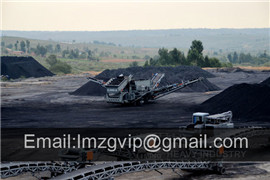
Importance of Cement Industry in India ijmra.us
From the clinker yard it is taken for grinding. In case ordinary portland cement is made only gypsum (46%) is added before grinding. In case of portland pozzolana cement additives like flyash/brick etc. are added Grinding again is same like for raw material grinding with ball mill or with latest technologies like verical mill/ Roller press etc

Ultratech Cement Commissions Cement & Grinding Units
With this commissioning the company’s total cement manufacturing capacity in India now stands at 126.95 million tonne per annum," the company said in an exchange filing. UltraTech has 22 integrated manufacturing units, 27 grinding units, one clinkerisation unit, and 8 bulk packaging terminals. It has a network of over one lakh channel

UltraTech Cement scale capacity of greenfield grinding
After this commissioning the company's total cement manufacturing capacity in India is at 126.95 mtpa. UltraTech Cement on Thursday announced the commissioning of 1.30 mtpa brownfield cement
- لفاف محطم مقابل الفك محطم
- تفاصيل حلقات ركوب الأفران الدوارة
- Concrete Mixing Plants Stock Image
- معدات غربلة الرمال في جنوب أفريقيا
- مصنع كسارة خام الحديد في العراق مصر
- المصنعين الفاصل المغناطيسي في تركيا
- تكلفة آلات محاجر الحجر الجيري
- Iron Ore Pelletsurface Hardening
- Mesin Penghancur Batu Kali Jaw Crusher Cone Crusher
- مشروع كسارة الحجر في ويكيبيديا
- خط عملية تنظيف الرمل الصناعي
- سنگ آهن کارخانه پی دی اف
- سعر معدات التكسير فى مصر
- حسابات كابكيتي مطحنة الذهب
- تامین کنندگان سنگ ماسه در بمبئی
- تستخدم معدات تعدين الماس في مصر
- mobile crusher plant flexible ramp
- غسل الرمال تجفيف طحن الرمل
- تصميم كسارة الحجر والتخطيط
- مصنع لتجهيز الخامات المستعملة