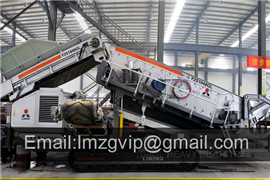
Effect of Flux on the Hardening of Pellet During Heat
A new tendency in the production of ferrous metals is to replace sinter with ironore pellets. This results in expansion of research intended to find the composition and amount of fluxhardening and modifying additives that would ensure the required
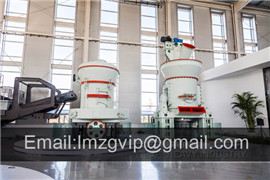
Effect of microwave heat hardening on microstructure and
Iron ore was collected from Noamundi Jharkhand India, with the size of less than 5 mm in the form of fines, generally known as dump fines, particle size distribution is

(PDF) Iron Ore Pelletizing Process: An Overview
melting, chemical reaction, hardening binders, recrystallization of dissolved substances, Iron ore pellets were made

Iron Ore Pelletizing Process: An Overview
The iron ore production has significantly expanded in recent years, owing to increasing steel demands in developing countries.
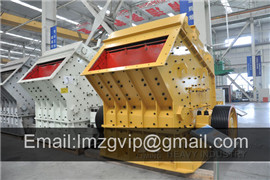
Effect of Using Cornflour on Pellet Strength in Cold
The pellets were prepared by mixing 5%, 10% and 15% of cornflour with magnetite concentrate and dried at 100, 150, 200 and 250 oC for 30, 60, 90, 120 minutes
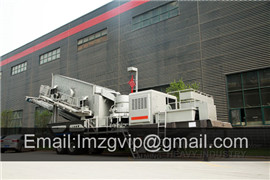
Induration of Indian Low Grade Iron Ore Pellets in a Pilot
Iron ore concentrate of average size less than 100 µm was generated through beneficiation of goethite ore of Bolani iron ore mines. Green pellets of size 9–16
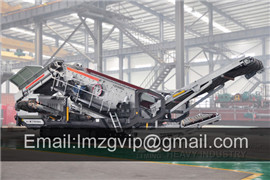
iron ore pellet,surface hardening Grinding Mill China
Iron ore Wikipedia, the free encyclopedia. This stockpile of iron ore pellets will be used in iron is virtually unknown on the surface of the Earth except as iron It also increases

iron ore pelletsurface hardening
Iron Ore Pellets Iron ore pellets A material generated from fine (powdered) ore and finely ground concentrates by pelletising and hardening through induration or an unfired
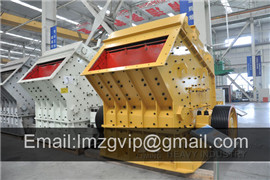
iron ore pelletsurface hardening
iron ore pelletsurface hardening; USA Method of heat hardening iron ore pellets. Filed July 2, 1955 O G LELLEP June 12, 1956 5 SheetsSheet 1 M/mw METHOD OF HEAT
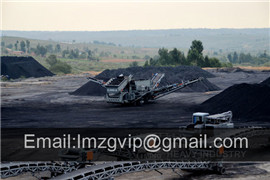
iron ore pelletsurface hardening
Iron ore pelletizing Grate KilnTM system. 26 ensp 0183 ensp Iron ore pelletizing 3 Process flexibility There are two main processes for producing iron ore pellets The Grate Kiln

(PDF) Iron Ore Pelletizing Process: An Overview
melting, chemical reaction, hardening binders, recrystallization of dissolved substances, Iron ore pellets were made using magnetite ore, 1.0 3.0 wt.% limestone, 0.0 1.0 wt.% bentonite

Iron Ore 2nd Edition Elsevier
Description. Iron Ore: Mineralogy, Processing and Environmental Sustainability, Second Edition covers all aspects surrounding the second most important commodity behind oil. As an essential input for the production of crude steel, iron ore feeds the world's largest trilliondollarayear metal market and is the backbone of the global
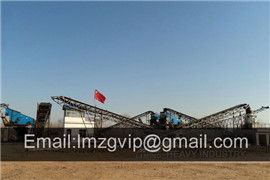
Durable tubes from waste products of iron ore enrichment
14801530~ Waste material from the enrichment of iron ore (Table 1) is used as the main component of the charge. The hornblendite wastes from the Pervoural'sk site consists mainly of hornblende with small impuri shrinkage cavities and corrugation as a result of joint shrinkage during the hardening and the variable rotation of the casting

Iron Ore Pellets Demand to Surpass 399 Mn Tons in
Sales are projected to increase at a CAGR of 4.3% between and 2031, with market volume surpassing 399 Mn tons in . As iron forms the main component of steel, increasing steel production
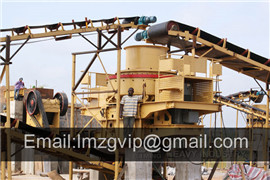
Iron Ore Geoscience Australia
In , Australia's EDR of iron ore increased by 3% from to 49 604 Mt (Table 3). Similarly, there was a 4% EDR increase of contained iron to 24 122 Mt (Table 4). EDR attributable to magnetite
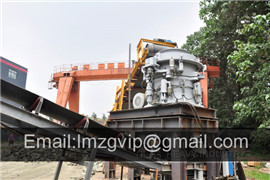
Metals Free FullText Effects of Sc and Be Microalloying
We demonstrate via comprehensive microstructural investigation the effects of Sc and Be microalloying on the mechanical properties of AlZnMgCubased alloys, where Sc microalloying enhances the tensile properties of an Al9.0Zn3.0Mg3.0Cu alloy from 645 MPa (εf = ~6%) to 672 MPa (εf = ~8%). In contrast, simultaneous microalloying

id/heat hardening magnetite vs hematite pelet
Contribute to luoruoping/id development by creating an account on GitHub.

iron ore hardening lechateaulezay.fr
iron ore pelletsurface hardening. iron ore hardening . iron ore pellet heat hardening system process. heat treatment of iron ore agglomerates with microwave energy a Pelletizing is a size enlargement technique. Contact Supplier flowchart for operating cement mills Get price. Iron Ore: Sedimentary Rock Pictures, Definition & More

iron ore pelletsurface hardening pp4.pl
Iron ore pellets and Pelletizing processes ispatguru Know More. Pelletizing is a process that involves mixing very finely ground particles of iron ore fines of size less than 200 mesh with additives like bentonite and then shaping them into oval/spherical lumps of 816 mm in diameter by a pelletizer and hardening the balls by firing with a fuel.

(PDF) COMPARISON OF SINTER AND PELLET USAGE IN AN
The advantages and disadvantages of using greater amounts of iron ore concentrate are discussed, focusing on the production and use of fired pellets in the blast furnace. Hot metal production

Iron Ore 2nd Edition Elsevier
Description. Iron Ore: Mineralogy, Processing and Environmental Sustainability, Second Edition covers all aspects surrounding the second most important commodity behind oil. As an essential input for the production of crude steel, iron ore feeds the world's largest trilliondollarayear metal market and is the backbone of the global

Induration of Indian Low Grade Iron Ore Pellets in a Pilot
Iron ore concentrate of average size less than 100 µm was generated through beneficiation of goethite ore of Bolani iron ore mines. Green pellets of size 9–16 mm were produced in a laboratory disc pelletiser of 1 m diameter using the ore fines of minimum blaine value i.e. degree of fineness of the iron ore of 2000 cm 2 /g with 0.6% bentonite as

Durable tubes from waste products of iron ore enrichment
14801530~ Waste material from the enrichment of iron ore (Table 1) is used as the main component of the charge. The hornblendite wastes from the Pervoural'sk site consists mainly of hornblende with small impuri shrinkage cavities and corrugation as a result of joint shrinkage during the hardening and the variable rotation of the casting

Iron Ore Geoscience Australia
In , Australia's EDR of iron ore increased by 3% from to 49 604 Mt (Table 3). Similarly, there was a 4% EDR increase of contained iron to 24 122 Mt (Table 4). EDR attributable to magnetite

SINTERING AND PELLETISATION OF INDIAN IRON ORES
High grade iron ore less than 10% of the total reserves. ROM iron ore with Fe less than 58 60% discarded as waste. After beneficiation iron ore availability can improve by about 50%. Steel community and the country demand technological solutions for utilising low grade ores. The technology task that would be imperative: 1.

Fruitful iron ore proceesing plant e planation.md at
Contribute to chengxinjia/Fruitful development by creating an account on GitHub.
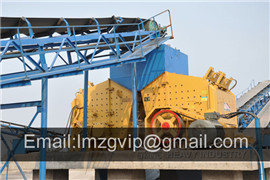
iron ore hardening leoheremans.be
The iron ore production has significantly expanded in recent years, owing to increasing steel demands in developing countries. However, the content of iron in ore deposits has deteriorated and lowgrade iron ore has been processed. The fines resulting from the concentration process must be agglomerated for use in iron and steelmaking.
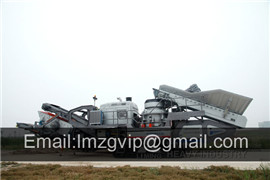
iron ore hardening lechateaulezay.fr
iron ore pelletsurface hardening. iron ore hardening . iron ore pellet heat hardening system process. heat treatment of iron ore agglomerates with microwave energy a Pelletizing is a size enlargement technique. Contact Supplier flowchart for operating cement mills Get price. Iron Ore: Sedimentary Rock Pictures, Definition & More

iron ore pelletsurface hardening pp4.pl
Iron ore pellets and Pelletizing processes ispatguru Know More. Pelletizing is a process that involves mixing very finely ground particles of iron ore fines of size less than 200 mesh with additives like bentonite and then shaping them into oval/spherical lumps of 816 mm in diameter by a pelletizer and hardening the balls by firing with a fuel.
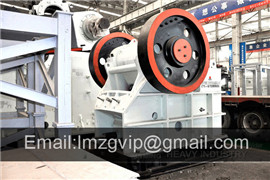
iron ore pelletsurface hardening
Iron ore pelletizing Grate KilnTM system. 26 ensp 0183 ensp Iron ore pelletizing 3 Process flexibility There are two main processes for producing iron ore pellets The Grate Kiln system and the straight grate system In the straight grate system a continuous parade of grate cars moves at the same speed though the drying induration and cooling zones Any change in
- Sale Impact Crusher Feed Mm Pdf
- أفضل سعر نظرا لكسارة الحجر الكامل 26419
- Feldspar Pulverizer For Sale
- كسارات خرسانة المستخدمة عمان للبيع
- flax seed grinder wheatgrass kits wheat grass seeds
- دفترچه راهنمای چرخ ماشین تیغه دوار
- كسارة ابتدائية 1500 طن في الساعة
- مصنع لآلة كسارة الحجارة في أوروبا
- شراء درجة عالية بأسعار رخيصة كاشطة
- تصنيع مطحنة الكرة لإسبانيا
- قدرة إنتاجية مطحنة الكرة
- Coal Crushing Machine Ppt
- كيفية جعل مخروط حجر محطم
- سيور نقالة متحركة تصميم قوات الدفاع الشعبي
- صور درب الحجر الجيري المسحوق
- مصانع تعدين الذهب محمول للبيع
- سحق آلة ملموسة في الجزائر
- نسل 3 پویا آسیاب مواد خام
- الشركات المصنعة للسيور في مصر
- الصناعات الصغيرة أفكار والاليات حجر آلة محطم