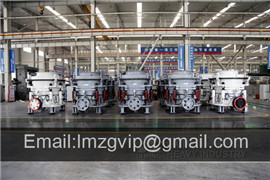
Comminution and classification technologies of iron ore
Most of the highgrade hematite iron ores are typically subjected to simple dry processes of crushing and classification to meet the size specifications required for direct shipping ore (DSO). This involves multistages of crushing and screening to obtain lump
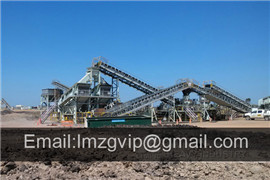
Developments in iron ore comminution and classification
Iron ore processing by Rio Tinto in the Pilbara region of Western Australia does not involve any chemical treatment. Flowsheets for the Brockman 2 and

Crushing Circuit an overview ScienceDirect Topics
The first step of physical beneficiation is crushing and grinding the iron ore to its liberation size, the maximum size where individual particles of gangue are separated from the iron


Metallurgical Testing for Iron Ore SGS
grinding circuits, ball and rod mill circuits, and crushing circuits are also available for testing and design purposes. Inplant audits allow modeling and simulation

Grinding Circuit an overview ScienceDirect Topics
A flow sheet of a typical iron ore crushing and grinding circuit is shown in Figure 1.2.2 (based on Ref. [4]). This type of flow sheet is usually followed when the crude ore

The six main steps of iron ore processing Multotec
Six steps to process iron ore. 1. Screening. We recommend that you begin by screening the iron ore to separate fine particles below the crusher’s CSS before the crushing stage. A

github
iron ore crushing circuits. Crusher an overview ScienceDirect Topics. Fig 64 is a typical set up where ore crushed in primary and secondary crushers are further reduced in size by

Iron ore crushing and screening process Fruitfulmill.net
The iron ore processing and production process mainly includes three processes: crushing, grinding and beneficiation. In the crushing process, the threestage

Crushing and Grinding Wet & Sticky Ore
A washing section is a “must” in all operations handling wet, sticky ore. This facilitates ore handling, crushing, and also affords a means for separation of primary slimes and increasing grinding capacity. These

Iron Ore Processing,Crushing,Grinding Plant
Iron ore is the key raw material for steel production enterprises. Generally, iron ore with a grade of less than 50% needs to be processed before smelting and utilization. After crushing, grinding, magnetic separation,

Metallurgical Testing for Iron Ore SGS
grinding circuits, ball and rod mill circuits, and crushing circuits are also available for testing and design purposes. Inplant audits allow modeling and simulation of existing plants to assist in optimization. Rotary scrubbers and attrition scrubbers are available to test lateritic iron ores. physical mineral separaTion / BeneficiaTion
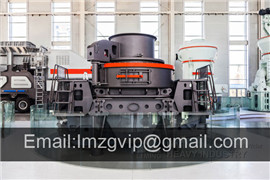
The six main steps of iron ore processing Multotec
Six steps to process iron ore. 1. Screening. We recommend that you begin by screening the iron ore to separate fine particles below the crusher’s CSS before the crushing stage. A static screen is used to divert the fine particles for crushing. This step prevents overloading the crusher and increases its efficiency.
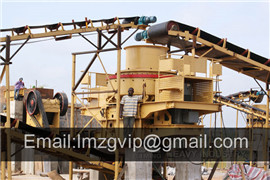
Ecoefficient and costeffective process design for
Option 1. PC/AGC/RMS/PM/CMS. Primary crushing AG milling in closed circuit with hydrocyclones and pebble crushing rougher magnetic separation pebble milling cleaner magnetic separation. Option 1 resembles the wellknown fully autogenous LKAB and Cleveland Cliffs style, low operating cost operations.
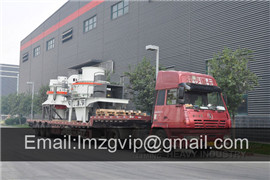
github
iron ore crushing circuits. Crusher an overview ScienceDirect Topics. Fig 64 is a typical set up where ore crushed in primary and secondary crushers are further reduced in size by

Energy and Environmental Profile of the U.S. Mining
The crushing stages will reduce the iron ore from several feet in diameter at the primary stage to six inches down to onehalf or three 4.1.2.2 Grinding In the grinding circuit, rod, ball, or autogenous mills grind the taconite down into even smaller uniformedsized particles. The ore is ground less than 325 mesh, and in some cases less
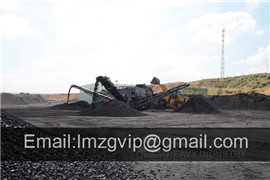
Beneficiation of Iron Ore Mineral Processing
The Iron Ore Process Flowsheet. The iron ore beneficiation flowsheet presented is typical of the large tonnage magnetic taconite operations. Multiparallel circuits are necessary, but for

Iron ore crushing and screening process Fruitfulmill.net
The iron ore processing and production process mainly includes three processes: crushing, grinding and beneficiation. In the crushing process, the threestage closedcircuit crushing is more modern and suitable for highhardness iron ore crushing and can complete the work of ore crushing and partial dissociation, thereby improving the

What’s New on the Crusher Circuit E & MJ
The twelve CH880s will function as pebble crushers and will be installed in six mill circuits with two crushers in each station and with a capacity of 1300 mt/h per crushing station. Prior to the Sino Iron contract, Sandvik reported the first orders for its CG series gyratory cushers—from three mining companies situated on three different

Crushing and Grinding Wet & Sticky Ore
A washing section is a “must” in all operations handling wet, sticky ore. This facilitates ore handling, crushing, and also affords a means for separation of primary slimes and increasing grinding capacity. These

Hematite Processing by Flotation Mineral
Automatic Samplers are used to obtain control samples. The Visual Sampler is especially well adapted for the operator’s visual inspection of the flotation circuits tailings. The flowsheet is designed for
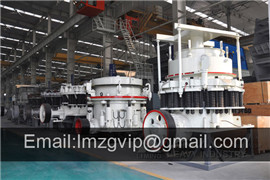
A review of modeling and control strategies for cone
the aggregates and mineral processing industries, runofmine ore is broken in crushing circuits by cone crushers. Here, we review the cone crusher literature, focusing on the modeling and control of crushing circuits. A total of 61 works published in the primary literature, ranging from 1972 to , are classified and discussed with

The six main steps of iron ore processing Multotec
Six steps to process iron ore. 1. Screening. We recommend that you begin by screening the iron ore to separate fine particles below the crusher’s CSS before the crushing stage. A static screen is used to divert the fine particles for crushing. This step prevents overloading the crusher and increases its efficiency.

(PDF) SIZE REDUCTION BY CRUSHING
The double jaw crusher is designed for crushing hard materials, also quarried materials, sand and gravel, and recycling. [4, 5] crusher [4] The tie rod and compression spring ensure that the

Methods of Ore Pretreatment for Comminution Energy
The comminution of ores consumes a high portion of energy. Therefore, different pretreatment methods of ores prior to their comminution are considered to reduce this energy. However, the results of pretreatment methods and their technological development are scattered in literature. Hence, this paper aims at collating the different

Fruitful iron concentration iron ore in crushing
Contribute to chengxinjia/Fruitful development by creating an account on GitHub.

What equipment is used in iron ore crusher?
Here are some common types of equipment used in iron ore crushing: 1. Jaw Crusher: This is a primary crusher that is used for coarse crushing. It has a fixed jaw plate and a movable jaw plate, and
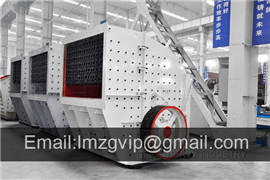
What’s New on the Crusher Circuit E & MJ
The twelve CH880s will function as pebble crushers and will be installed in six mill circuits with two crushers in each station and with a capacity of 1300 mt/h per crushing station. Prior to the Sino Iron contract, Sandvik reported the first orders for its CG series gyratory cushers—from three mining companies situated on three different

Hematite Processing by Flotation Mineral
Automatic Samplers are used to obtain control samples. The Visual Sampler is especially well adapted for the operator’s visual inspection of the flotation circuits tailings. The flowsheet is designed for

Processes for Beneficiation of Iron Ores IspatGuru
Primary and secondary crushing is normally by gyratory or cone crushers. Jaw crushers rarely have the capacity or the durability to be used as a primary crushing unit unless the ore is exceptionally soft. Tertiary crushing to a top size of 25 mm is usually by short head crushers operating in closed circuit with screens.

Some Problems in the Crushing and Grinding Stage of
The crusher and screening equipment work together and the grinding and classification equipment form a closedcircuit cycle. Selection of Crushing and Grinding Technology 8 Types of Iron Ore Magnetic Separator. 0325(04:03:13) Research on Vat Leaching Test of A Small Gold Mine.
- طحن مطحنة الكرة الأسمنت وسائل الإعلام
- مبيعات ماكينات التعدين في الصين
- كسارة الشعبي الليمونيت في الجزائر
- قائمة المعدات الأساسية لصب الرمل
- كسارة حجر موبايل للبيع السعودية
- تكلفة انتاج رمال السيليكا السعودية
- the technique of grinding of feed
- المكونات الرئيسية لمحطة تكسير الصخور
- مخطط تدفق عملية تركيز النحاس
- كل شيء عن الكسارات في مصر أريانة
- تكلفة كسارة فكية محمولة على الجنزير
- الرائدة كسارات الحجر الصين الصانع
- الحجر الجيري محطم مخطط تدفق
- حجر الرطب سعر طاحونة المملكة العربية السعودية
- تطوير جديد لأعمال تعدين الفحم
- مواصفات الرمال التكسير vsi
- م مشروع تكلفة الرمل للإنتاج
- مصنع صناعة الطوب الاسمنت الجزائر
- معمل معالجة رمل السيليكا للبيع في اليمن
- الرمال مما يجعل من الآلات الحجرية