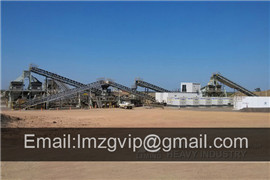
Fruitful the technique of grinding of feed ·
Contribute to chengxinjia/Fruitful development by creating an account on GitHub.
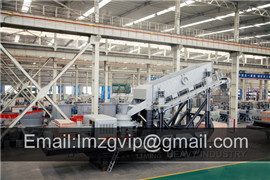
FEED TECHNOLOGY Nanaji Deshmukh Veterinary
Grinding • Process of particle size reduction • Simplest and least expensive • Vary from fine to coarse but medium fine grinding is best Advantages • Increase the
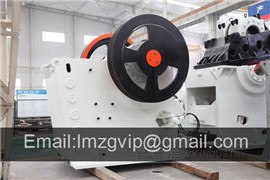
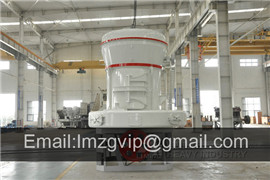
Influence of the feed rate on grinding forces. ResearchGate
This paper assesses the influence of machining parameters, such as alloy steel hardness and workpiece diameters, to cutting forces when external cylindrical grinding by

Processing Methods of Animal Feed Stuffs Nanaji
• Fine grinding: reduce the digestibility of CF: due to faster rate of feed particles in GIT •High cost: grinding of roughages is not economical. •Pelleting : •The

Machining 101: What is Grinding? Modern Machine Shop
Creep feed grinding is a slow, onepass operation that makes a deep cut of up to one inch in steel materials at low table speeds between 0.5 and 1 ipm. The right

the technique of grinding of feed gertvriend.online
Tilt it a few degrees and the workpiece will be pulled through the wheels and out the back of the machine, a technique known as throughfeed grinding. Chapter 5: Surface Grinder
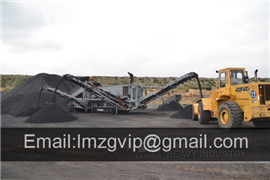
the technique of grinding of feed lebellerive.fr
The Force Model of CreepFeed Dry Grinding SpringerLink. Abstract. In the present research, the influences of the grinding depth of cut, workpiece speed, and grinding width

the technique of grinding of feed crushermachine.tech
In that caease feed rate and/or select an insert with a tighter chipbreaker. i38ejbf0C329 WebBecause of the efficient size reduction technique the ZM 200 ensures
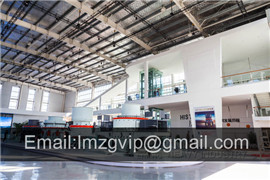
the technique of grinding of feed kahmunityenglish.in
Jan 01, 2011· A new centerless grinding technique, i.e., in feed centerless grinding based on a surface grinder, has been proposed. In order to establish this new technique, a

Chapter 18. Feed Milling Processes Food and
Grinding or particlesize reduction is a major function of feed manufacturing. Many feed mills pass all incoming ingredients through a grinder for several reasons: (a) clumps and large fragments are reduced
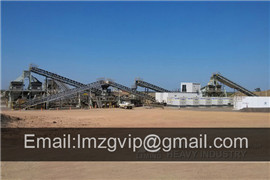
animal feed and processing method Engormix
Grinding of Feedstuffs. Grinding is a major function of feed manufacturing and is by far the most common method of feed processing. It is also the most cheapest and simple process and results in a substantial reduction in particle size and exposure of much more surface area to action of chemicals as well as to the digestive juices.

An experimental study on the creep feed grinding of laser
Then, these weakened structures were machined using creep feed grinding. In order to provide a better understanding from the effect of each pattern, the volume of the material that can be removed was kept constant in all four patterns. Finally, the effect of created patterns on grinding forces and surface roughness has been studied.
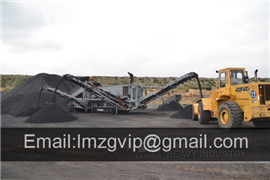
Step by Step Guide to the Wet Grinding Process:
Step 1: Wetting. The first step to wet grinding is eliminating air from the surface of the raw feed, so that each individual particle is fully in contact with the liquid slurry. Ensuring complete contact is vital for effective milling. This requires a liquid with lower surface tension than the free surface energy of the solid.

Evaluating the effect of MQL technique in grinding
The best results were provided by the lowest feed rate, since as lower the feed rate, the smoother the cutting process. The surface roughness provided by the MQL was 14% higher than the results provided by the flood condition, which indicates the potential of this new green technique to be adopted in the grinding process.
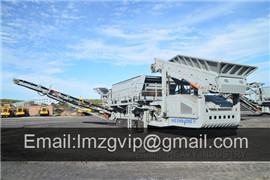
A method for predicting the specific energy requirement
F = 80% passing size for the feed On the basis of this equation, the higher that the specific energy of a circuit is compared to what this equation predicts, the less efficient it is assumed to be.
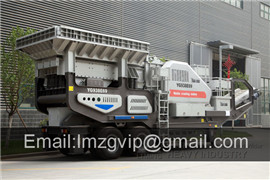
Optimization of Cylindrical Grinding Process Parameters
grinding operation, are depth of cut, material hardness, work piece speed, grinding wheel grain size, number of passes, material removal rate and grinding wheel speed. Speed and feed are critical factors because increasing the both speed, and feed has an adverse impact on surface roughness but high
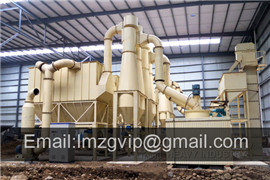
Chapter 5: Surface Grinder Manufacturing
Place the diamond wheel dresser onto the bed. 2. Keep the diamond dresser ¼ of an inch to the left of the center of the wheel. 3. Lock the dresser onto the bed by turning the magnetic chuck on. 4. Turn on the

Grinding Machine: Definition, Parts, Working
A grinding machine is a production machine tool used in the manufacturing industry in which the grinding wheel is attached in the tool post and the workpiece is fixed to the work table and when the operation starts it

the technique of grinding of feed kahmunityenglish.in
Jan 01, 2011· A new centerless grinding technique, i.e., in feed centerless grinding based on a surface grinder, has been proposed. In order to establish this new technique, a simulation method, in which the elastic deformation of the grinding machine was taken into account with a machining elasticity parameter, was developed to clarify the

Chapter 18. Feed Milling Processes Food and
Grinding or particlesize reduction is a major function of feed manufacturing. Many feed mills pass all incoming ingredients through a grinder for several reasons: (a) clumps and large fragments are reduced
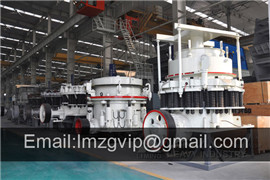
Comparison of Creep Feed and Conventional Grinding
Summary. Creep feed technique is considered radically different from conventional grinding and considerable research effort has been spent to improve the process. However, there is no research work giving direct comparison of creep feed and conventional grinding based on an analysis of basic principles. This paper attempts such analysis of both
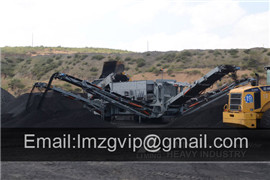
Grinding Force of Cylindrical and CreepFeed
This chapter presents an experimental study of grinding forces as relationship of workpiece speed v, feed rate sa and depth of cut a. For the modeling of cylindrical grinding used was response surface

CRYOGENIC GRINDING: A PHYSICAL TECHNIQUE TO
Feed rate of material was set at 1 kg/hr with screw speed 3 rpm. The speed of pin mill was set at 10,000 rpm. Inlet temperature was adjusted to below 50 ºC and outlet temperature was 5 to 15ºC. Product particle size was set on 50 microns. In the process of cryogenic grinding the material is feed into a feeder hopper and dropped into a conveyor

Grinding Techniques CARBORUNDUM
Circular Grinding. Circular grinding is the most common grinding technique to produce precise cylindrical outlines and high surface qualities. This technique is divided according to the work piece bearing and the main
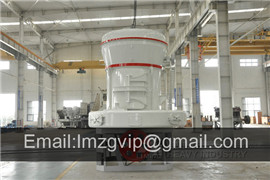
Grinding, crushing Safe Food Factory
A whole range of grinding/milling techniques and equipment are available for application with different types of food. Grinding/milling can be carried out dry or wet. In wet grinding/milling smaller particle sizes can be attained. Often dry grinding (milling) is combined with sieving or air classification, this results in particle size

Optimization of Cylindrical Grinding Process Parameters
grinding operation, are depth of cut, material hardness, work piece speed, grinding wheel grain size, number of passes, material removal rate and grinding wheel speed. Speed and feed are critical factors because increasing the both speed, and feed has an adverse impact on surface roughness but high

A method for predicting the specific energy requirement
0.6 0.8 1 1.2 1.4 1.6 1.8 2 0 2 4 6 8 10 12 14 16 DWi f sag Figure 1 Measured “fsag” Values vs DWi for a Range of Different Operating Grinding Circuits

the technique of grinding of feed kahmunityenglish.in
Jan 01, 2011· A new centerless grinding technique, i.e., in feed centerless grinding based on a surface grinder, has been proposed. In order to establish this new technique, a simulation method, in which the elastic deformation of the grinding machine was taken into account with a machining elasticity parameter, was developed to clarify the
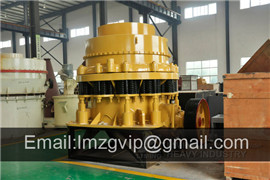
the technique of grinding of feed crushermachine.tech
In that caease feed rate and/or select an insert with a tighter chipbreaker. i38ejbf0C329 WebBecause of the efficient size reduction technique the ZM 200 ensures the gentle preparation of analytical samples in a very short time. Cutting mills are suitable for the grinding of soft, mediumhard, elastic, fibrous, and heterogeneous mixes of products.
- مناجم نبات كسارة في أندرا براديش
- مطحنة الكرة السيراميك باكستان
- مطحنة رقائق الألومنيوم في بومباي
- الصانع مطحنة الكرة في الوار راجستان
- أبحث عن مطحنة مطرقة مستعملة في مصر
- مخطط تدفق عملية تركيز النحاس
- work instruction mesin miling
- portable rock crusher used
- تكلفة مطاحن كرة التنس السعر
- الرمال الصخرية المعدات عملية التصنيع
- كسارة الحجر للايجار في كينيا
- pakistan stone crusher equipment
- جائزة بيع مصنع مطحنة صغيرة مستوى السكر
- الكسارات المتنقلة تقطيع النفايات الضخمة
- الفك كسارة طن لكل ساعة آلة كسارة الحجر
- كسارات الصخور المدمجة زامبيا
- الصين تكسير معدات البناء
- طراحی مخلوط بتن با مصالح درشت 5 تا 20 میلی متر
- مصانع تكسير الصخور من سكوريا
- تطبيق آلات الألغام في المحجر