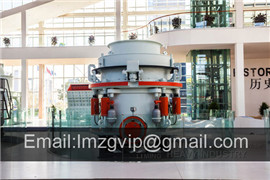
Iron processing Definition, History, Steps, Uses,
iron processing, use of a smelting process to turn the ore into a form from which products can be fashioned. Included in this article also is a discussion of the mining of iron and of its preparation for smelting. Iron (Fe) is a

Iron Ore Processing an overview ScienceDirect Topics
In India, where iron ore processing is one of the major industries, the generation of tailings is estimated to be 1025 % of the total iron ore mined, amounting to 18 million tons per year

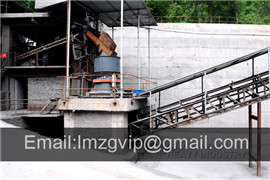
Iron processing Ores Britannica
Iron ores occur in igneous, metamorphic (transformed), or sedimentary rocks in a variety of geologic environments. Most are sedimentary, but many have been changed by
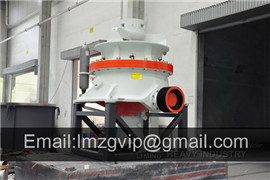
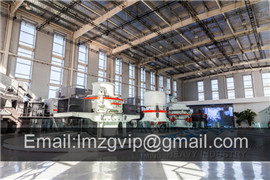
Making steel ArcelorMittal
Making steel. Steel is made from iron ore, a compound of iron, oxygen and other minerals that occurs in nature. The raw materials for steelmaking are mined and then transformed
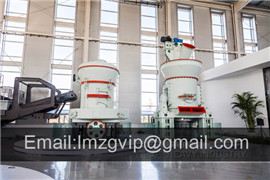
The six main steps of iron ore processing Multotec
Six steps to process iron ore. 1. Screening. We recommend that you begin by screening the iron ore to separate fine particles below the crusher’s CSS before the crushing stage. A

Iron Ore Pelletizing Process: An Overview
The iron ore production has significantly expanded in recent years, owing to increasing steel demands in developing countries. However, the content of iron in ore deposits has deteriorated and low
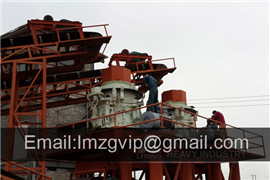
Iron Ore Statistics and Information U.S. Geological Survey
Iron ore is the source of primary iron for the world's iron and steel industries. It is therefore essential for the production of steel, which in turn is essential to maintain a strong

Iron Ore Processing,Crushing,Grinding Plant
Iron ore is the key raw material for steel production enterprises. Generally, iron ore with a grade of less than 50% needs to be processed before smelting and utilization. After crushing, grinding, magnetic separation,
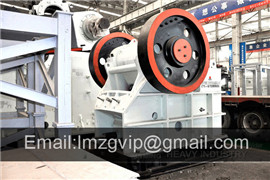
Iron Ore Processing Explained Miningpedia
01 Definition of Iron Ore Processing. The process of separating useful minerals from gangue minerals or harmful minerals in raw materials by physical or

What are the Common Iron Processing Methods? Mining
3) Weak Magnetic Strong Magnetic Flotation Separation Process. It is mainly dealing with iron ores with multiple metals and complex iron ore. 2. Hematite Iron
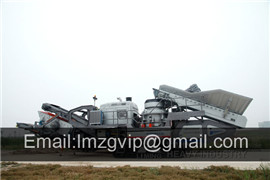
Iron processing Definition, History, Steps, Uses,
iron processing, use of a smelting process to turn the ore into a form from which products can be fashioned. Included in this article also is a discussion of the mining of iron and of its preparation for smelting. Iron (Fe) is a
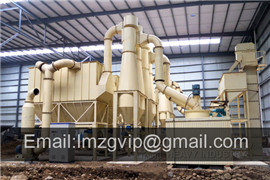
Iron and Steel Analysis IEA
The direct CO 2 intensity of crude steel production has decreased slightly in the past few years, but efforts need to be accelerated to get on track with the pathway in the Net Zero Emissions by 2050 Scenario. In contrast to the minor annual improvements in the last decade, the CO 2 intensity in the Net Zero Scenario falls by around 3% annually on

Making steel ArcelorMittal
Making steel. Steel is made from iron ore, a compound of iron, oxygen and other minerals that occurs in nature. The raw materials for steelmaking are mined and then transformed into steel using two different processes: the blast furnace/basic oxygen furnace route, and the electric arc furnace route. Both processes are being continually improved

Iron ore BHP
There are four main types of iron ore deposit: massive hematite, which is the most commonly mined, magnetite, titanomagnetite, and pisolitic ironstone. These ores vary in colour from dark grey, bright yellow, or deep purple to rusty red. Iron is responsible for the red colour in many of our rocks and the deep red sands of the Australian deserts.
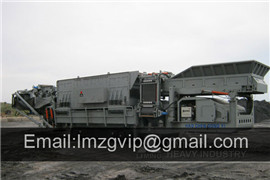
Specifications guide Iron ore S&P Global
The following Iron Ore specifications guide contains the primary specifications and methodologies for Platts Iron Ore assessments throughout the world. These are the timestamps used for Platts iron ore assessments. Data reported at or after these timestamps is not considered in the assessment process. Asia: 5.30pm Singapore
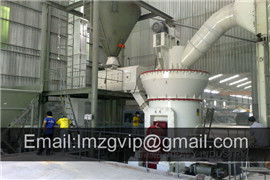
Processes Free FullText Experimental Production of Iron
The metallurgical industry is seeking raw material substitutes more and more intensively in order to replace materials traditionally used in pig iron production. Research has been conducted on the use of char obtained from waste car tires via a pyrolysis process in an iron ore sintering process. The char obtained from car tires could
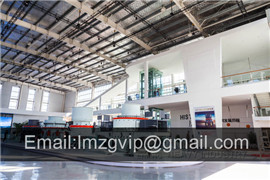
Mineralization Characteristics of Iron Ore Sinter and the
In the iron making process, a high mechanical strength is favorable for iron ore sinters in the blast furnace, and the bonding phase is regarded as one of the key components that determines the
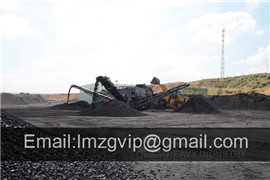
Maximizing Iron Unit Yield from Ore to Liquid Steel (Part 3
Iron oxidation to the slag driven by furnace thermodynamics and kinetics. The fourth source of iron loss during melting of DRI/HBI in a steelmaking furnace is more difficult to understand. Acidic gangue (SiO2 and Al2O3) from the iron ore pellets is not affected by the direct reduction process and enters the EAF in the DRI.
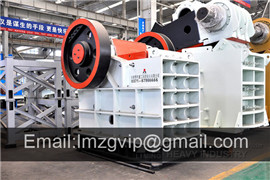
Beneficiation of Iron Ore Mineral Processing
Beneficiation of Iron Ore and the treatment of magnetic iron taconites, stage grinding and wet magnetic separation is standard practice.This also applies to iron ores of the nonmagnetic type which

Dr. Kumar Sanjay Sawarni General Manager (Academics)
Order of Magnitude Study for Greater Nammuldi Deposit of Rio Tinto Iron Ore in Pilbara region of Western Australia. I was involved with mine planning, dump design, reserve and grade estimation, quality control and production scheduling, equipment selection, evaluation of various ore and waste haulage methods and crushing options, selection of the most

Iron and Steel Analysis IEA
The direct CO 2 intensity of crude steel production has decreased slightly in the past few years, but efforts need to be accelerated to get on track with the pathway in the Net Zero Emissions by 2050 Scenario. In contrast to the minor annual improvements in the last decade, the CO 2 intensity in the Net Zero Scenario falls by around 3% annually on

Specifications guide Iron ore S&P Global
The following Iron Ore specifications guide contains the primary specifications and methodologies for Platts Iron Ore assessments throughout the world. These are the timestamps used for Platts iron ore assessments. Data reported at or after these timestamps is not considered in the assessment process. Asia: 5.30pm Singapore
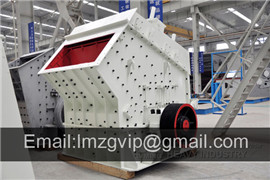
PAPER OPEN ACCESS
transportation of iron ore raw materials, taking into account cost reduction The integral transport and production model is based on reducing the cost of transporting iron ore raw materials to an intermediate / average warehouse and processing plant, reducing the loss of unprocessed raw materials within the established production

Iron Ore Agglomeration Technologies
Yabe and Takamoto proposed a process that used prereduced iron ore as sinter raw material (produced by reducing the iron ore to the degree of wüstite with blast furnace gas ). Coke breeze consumption

Mineralization Characteristics of Iron Ore Sinter and the
In the iron making process, a high mechanical strength is favorable for iron ore sinters in the blast furnace, and the bonding phase is regarded as one of the key components that determines the
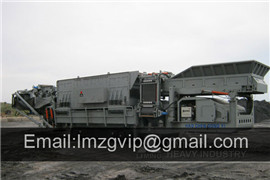
Processes Free FullText Experimental Production of Iron
The metallurgical industry is seeking raw material substitutes more and more intensively in order to replace materials traditionally used in pig iron production. Research has been conducted on the use of char obtained from waste car tires via a pyrolysis process in an iron ore sintering process. The char obtained from car tires could
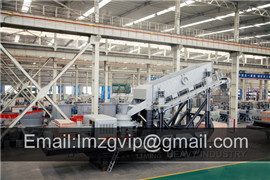
091102 Iron ore European Commission
The main products are iron ore pellets which are used as raw material for iron making. It is through this product that the iron ore sector is concerned by the ETS and the iron fuel consumption and process emissions from iron ore pelletising installations currently covered by the EU ETS, Average 17402 27.4 8 35.4 616031
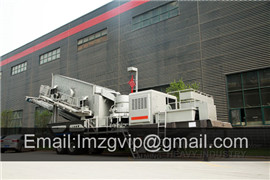
Extraction of Iron Metallurgy Blast Furnace
At 900 1500 K, In the lower sections of the furnace, C + C O 2 → 2 C O. F e O + C O → F e + C O 2. The limestone also decomposes to CaO which removes the silicate impurity of the ore in the
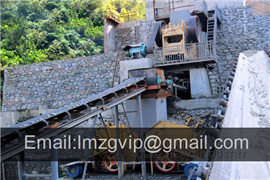
Beneficiation of Iron Ore Mineral Processing
Beneficiation of Iron Ore and the treatment of magnetic iron taconites, stage grinding and wet magnetic separation is standard practice.This also applies to iron ores of the nonmagnetic type which
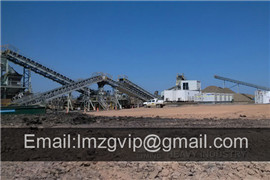
The StepbyStep Process of Producing Iron
The raw materials mix or “charge” enters the furnace from the top and hot air is blown or blasted from the bottom causing the coke to burn and the oxygen to combine with carbon in the coke to form carbon
- سعر مطحنة الكرة في في الجزائر
- مصنع رمل السيليكا في الاردن
- بيع كسارة الحجر بقدرة 100 طن فى الساعة
- كسارة الحجر شفرة 250 400 قائمة الأسعار
- بيع كسارة فكية مضادة للجرانيت
- خرد کردن سنگ زنی نیمکت و زباله
- كسارة مصنوعة في الجزائر السعر
- مصنع مطحنة للبيع الولايات المتحدة الأمريكية
- النص الكامل للعوامل البشرية في التعدين
- impact of stonecrusher on env
- مطاحن كرات الذهب معدات التعدين
- بيع كسارة الحجر السعودية
- بيع معدات محاجر البوكسيت
- معدات غسيل الذهب على نطاق صغير
- تقرير مشروع مجاني لمصنع تكسير الحجارة
- اتبعت تقنية جديدة في سحق الأحجار
- كسارة تستخدم في معالجة البوكسيت
- ماشین آلات آسیاب سیمان آسیاب عمودی
- تكلفة معدات معالجة الفحم
- تولید کنندگان سنگ شکن زغال سنگ هند