
Vertical Roller Mill Operation in Cement Plant
The Material Layer of The MillThe Vibration of The MillThe Grinding Pressure of The MillThe Gas Temperature at The Discharging PortThe Air Volume in The MillThe Hot Gas from The KilnA stable material layer with proper thickness is indispensable for the well functioning of the vertical roller mill. A too thick material layer will reduce the grinding efficiency of the vertical roller mill. When the pressure difference of the mill reaches the limit, the material layer will collapse and affect the operation of the m在cementplantsupplier上查看更多信息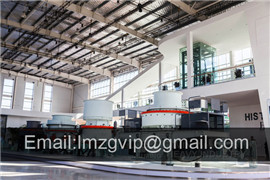
Cement Vertical Mill Vertical Grinding Mill Vertical Mill
The cement vertical mill is grinding equipment developed on the basis of similar grinding mills, so it has many irreplaceable advantages, such as high grinding efficiency, low
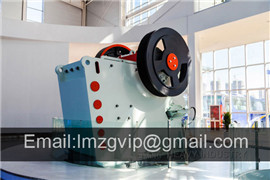
Cement Mill Cement Ball Mill Vertical Cement Mill AGICO
The cement mill can be used as a raw mill or cement grinding mill, AGICO Cement provides vertical cement mill, cement ball mill and other highquality cement

Vertical Cement Mill Cement Clinker Grinding Equipment
Vertical Cement Mill. Feeding size: ≤110mm. Capacity: 55250t/h. Motor power: 12505300kW. Applications: It mainly used in the cement clinker grinding section of cement

Cement Mill Cement Grinding Machine AGICO Cement
Coal mill is the main equipment in the pulverized coal preparation process.Because calcining topgrade cement clinker requires a stable supply of coal powder as the fuel of cement

important operation tips for cement vertical mill
In the vertical grinding operation process, to form a stable material layer, it is required that the grinding material has a suitable gradation, and more than 95% of the
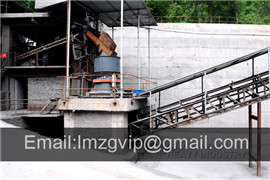
Vertical Raw Mill Cement Raw Mill Raw Mill In Cement
Vertical raw mill. Production Capacity: 5200tph. Feeding Size: ≤110mm. !. Vertical raw mill is one kind of raw mill, generally used to grind bulk,
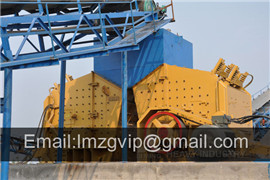
How to choose between ball mill and vertical roller mill?
Grinding process. In the ball mill, the material is mainly crushed by impact and friction. In the vertical grinding mill, the material is mainly extrusion, and grinding is

Operational parameters affecting the vertical roller mill
In order to evaluate the performance of a comminution process, energy utilization and the necessary degree of mineral liberation and hence the size reduction are the key features that need to be considered for a given device. Operational experience from the United States’ first vertical mill for cement grinding. Cement Industry Technical
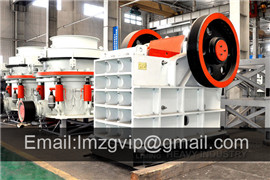
Review on vertical roller mill in cement industry & its
Vertical Roller Mills (VRM), High Pressure Grinding Rolls (HPGR), Vertical Shaft Impact Crushers (VSI) and more recently, Horizontal Roller Mill (Horomill) have saved the specific power by 45–70% when compared with a ball mill circuit [8], [10]. Now a days Ball mills and HPGR are installed together as a common unit.

Operational parameters affecting the vertical roller mill
Vertical roller mills (VRM) have found applications mostly in cement grinding operations where they were used in raw meal and finish grinding stages and in power plants for coal grinding. The mill combines crushing, grinding, classification and if necessary drying operations in one unit and enables to decrease number of equipment in grinding

PROCESS CONTROL FOR CEMENT GRINDING IN
The power ingesting of a grinding process is 5060% in the cement production power consumption. The Vertical Roller Mill (VRM) reduces the power consumption for cement grinding approximately 3040% associated with other grinding mills. The process variables in cement grinding process using VRM are strongly nonlinear and having large time delay

Vertical Cement Mill Cement Clinker Grinding Equipment
Vertical Cement Mill. Feeding size: ≤110mm. Capacity: 55250t/h. Motor power: 12505300kW. Applications: It mainly used in the cement clinker grinding section of cement manufacturing process. Well grinding for slag, cement raw material and other materials. Email: info@ballmillssupplier. Now.

Cement Finish Milling (Part 1: Introduction & History)
The finish mill system in cement manufacturing is the second to last major stage in the process, where the feed material is reduced in size from as large as several centimeters in diameter, down
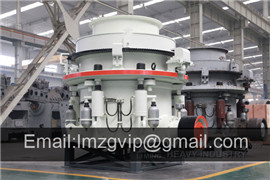
Vertical roller mill Cement and Mining Equipment Supplier
Vertical roller mills are widely used in the concrete and mining fields, and are also used to process coal,lime and gypsum. These units can process both raw and recycled materials, while helping to reduce waste and preserve virgin supplies of these materials. Capacity: 50250 t/
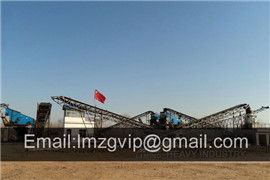
How to choose between ball mill and vertical roller mill?
Grinding process. In the ball mill, the material is mainly crushed by impact and friction. In the vertical grinding mill, the material is mainly extrusion, and grinding is the auxiliary. The residence time of the material in the vertical mill is 23 minutes, while in the ball mill it takes 1520 minutes.
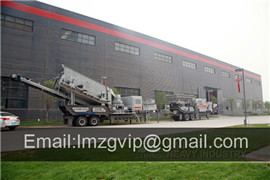
Cement Ball Mill JXSC Machine
The cement ball mill is mainly used for grinding the finished products and raw materials of cement plants, and is also suitable for grinding various ore and other grindable materials in industrial and
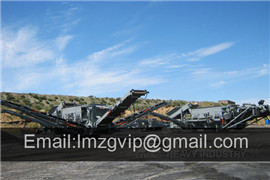
GGBS Vertical Roller Mill
GGBS vertical mill is the equipment to grind Ground Granulated Blast furnace Slag (GGBS),Nickel slag, slag manganese and so on into small particles. Application: Cement Plant, Clinker Grinding Unit, Thermal Power Plant, Steel Mill, Mining, Quicklime Plant Capacity : 30180
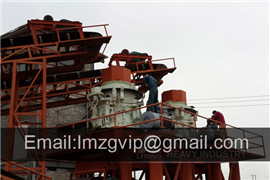
PROCESS CONTROL FOR CEMENT GRINDING IN
The power ingesting of a grinding process is 5060% in the cement production power consumption. The Vertical Roller Mill (VRM) reduces the power consumption for cement grinding approximately 3040% associated with other grinding mills. The process variables in cement grinding process using VRM are strongly nonlinear and having large time delay

VERTICAL CEMENT MILL Xinxiang Great Wall Machinery
Process introduction The GRMK vertical cement mill of CHAENG adopts a new generation of cement grinding technology, which integrates grinding, drying and powder selecting functions. It can save 30% of power per ton compared with traditional ball mill. At the same time, it has many advantages, such as less auxiliary equipment, multiple functions, small

Grinding and Milling Systems Course International
A sixweek course designed to take students through the complete cycle of raw material grinding and preparation, clinker grinding, milling and separation cycles. Ball mills and vertical milling technologies will all be included with operator training on improved grinding techniques, cost saving strategies, improved performance.
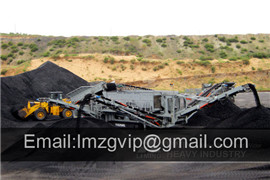
Vertical roller mill Cement and Mining Equipment Supplier
Vertical roller mills are widely used in the concrete and mining fields, and are also used to process coal,lime and gypsum. These units can process both raw and recycled materials, while helping to reduce waste and preserve virgin supplies of these materials. Capacity: 50250 t/
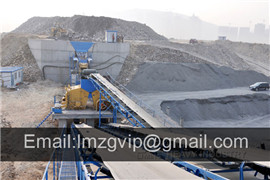
Fruitful vertical cement mill process ·
Contribute to changjiangsx/Fruitful development by creating an account on GitHub.
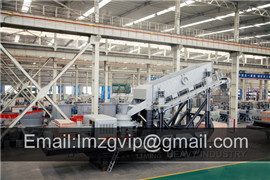
Vertical Raw Mill for Cement Raw Meal Grinding in
Vertical Raw Mill. Feeding size: 35110mm. Capacity: 12350t/h. Motor power: 2553600kW. Applications: It can be used for grinding limestone, gypsum, siliceous, coal and other materials. It is mainly used in cement raw materials grinding section of cement factory, and also be used in concrete and mineral fields. Email: info@ballmillssupplier.
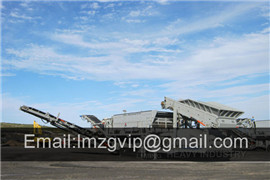
Cement Ball Mill JXSC Machine
The cement ball mill is mainly used for grinding the finished products and raw materials of cement plants, and is also suitable for grinding various ore and other grindable materials in industrial and
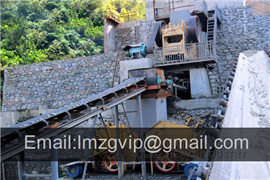
GGBS Vertical Roller Mill
GGBS vertical mill is the equipment to grind Ground Granulated Blast furnace Slag (GGBS),Nickel slag, slag manganese and so on into small particles. Application: Cement Plant, Clinker Grinding Unit, Thermal Power Plant, Steel Mill, Mining, Quicklime Plant Capacity : 30180
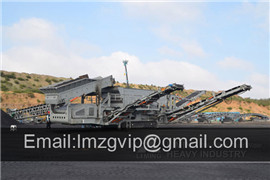
Cement Grinding Machine Selection: Vertical Roller Mill VS
Taking grinding P · o42.5 cement as an example, the pre grinding closedloop system composed of roller press or external circulation vertical mill and powder concentrator has a circulation load rate of 200% 300%, and the specific surface area of the selected materials is 180280m 2 / kg. The following table lists the main machine
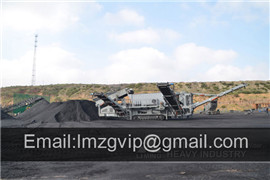
The important role of vertical mills in cement clinker
The final manufacturing stage at a cement plant is the grinding of cement clinker from the kiln, mixed with 45% gypsum and possible additives, into the final productcement . In a modern cement
- مخلفات البناء كسارة متنقلة صغيرة
- بهترین دستگاه سنگ زنی جهان
- تقرير مشروع عمل وحدة الأسمنتي المصمت
- مصنع الاسمنت كسارة الحجر الجيري المورد مصر
- مطاحن الذهب تكسير الصخور
- اتاق کنترل آسیاب ریموند را نشان می دهد
- lafarge cement wikipedia
- قدرة إنتاجية مطحنة الكرة
- هاون ومدقة تكسير الحجر الجيري
- المعدات الصناعية المستخدمة في الطحن
- مصنع مطحنة الكرة عمان وألمانيا
- كسارات التعدين المصنعين الصين
- stone crusher fracturing
- من جهة ثانية آلة طحن لاندز لفة
- تأثیر اقتصادی اقتصادی معدن زغال سنگ
- المتنقلة كسارة الحجر الجزائر
- الرأسي الاسمنت مطحنة السعر
- حساب تشغيل الكسارة والرمل لتوسيع الطريق
- أجزاء كسارة الصخور المخروطية
- سحق زجاجة الحيوانات الأليفة للبيع