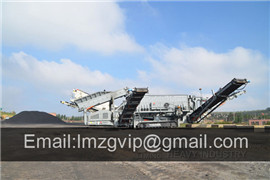
Physical separation of iron ore: magnetic separation
The ore is mainly composed of magnetite, hematite, martite, and quartz. It is very difficult to produce a high quality iron ore concentrate by magnetic separation alone for this type of iron ore. The feed ore is first ground using ball mills down to about 90% −75
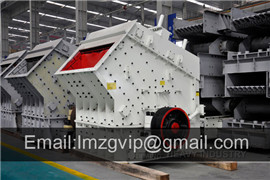
Developments in the physical separation of iron ore:
Because the crystal water in limonitic ores will report to the iron ore concentrate in magnetic separation, the iron ore concentrate grade is limited to about
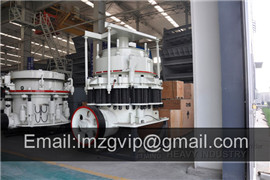
Magnetic Separation an overview ScienceDirect Topics
C. Crisafio, in Iron Ore. 10.4.2.3 Use with WHIMS. Iron ore processors may also employ magnetic separation for beneficiation of classifier output streams. Wet high


Magnetic Separator an overview ScienceDirect Topics
Developments in the physical separation of iron ore. D. Xiong, R.J. Holmes, in Iron Ore, 9.5.2 Utilization of subeconomic iron ores. As magnetic separators progress toward
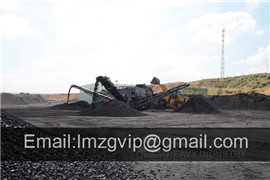
Separation and Recovery of Iron from LowGrade
From Table 2, the iron elements were mainly found to exist in the form of magnetite, hematite, and limonite in the lowgrade iron ore sample, and hematite and

Development of a novel magnetic separator for
The concept of particle separation by rotating magnetic field was proposed by Dean and Devis (Reginald Scott Dean, xxxx; Dean and Davis, 1941).The rotating magnetic field
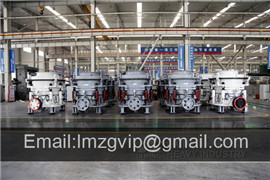
Dry Magnetic Separation of Iron Ore of the
Ores of this deposit are related to the highgrade type and expected to have a magnetic concentration for iron extraction. The main task of magnetic separation is to increase the total iron
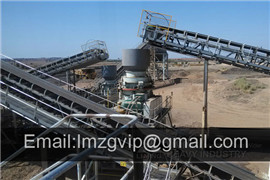
Wet High Intensity Magnetic Separation of Iron
The Series L Model 4 (L4 machine) (Eriez Manufacturing Co.) was used for magnetic separation of the ore samples. The L4 machine uses wire mesh or pipe matrix fixed inside the casing as magnetic

Process and Principle of Magnetic Separation of Iron Ore
Magnetic separation is a beneficiation method that uses the magnetic difference between minerals in a nonuniform magnetic field to separate different
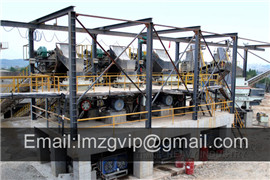
Separation process of iron ore,iron ore magnetic
When the grinding particle size is greater than 0.2mm, most iron ore magnetic separation plants usually use one stage grindingmagnetic separation; If

Open Access proceedings Journal of Physics: Conference
Magnetic separation is applied in ore processing for separating magnetic materials, particularly Iron [4]. The advent of magnetic separation found favour in mineral processing for over 200 years ago. The knowledge and use of magnetic concepts can be traced back to Thales of Miletus, A Greek
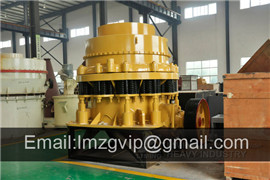
Separation and Recovery of Iron from LowGrade
From Table 2, the iron elements were mainly found to exist in the form of magnetite, hematite, and limonite in the lowgrade iron ore sample, and hematite and limonite occupied about 22.37 mass% of the total iron, which should be reduced to magnetite first.. The lignite, obtained from Xinjiang Province of China, was used as a
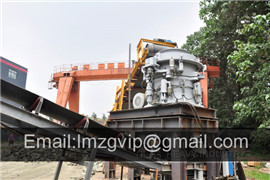
Effect of additives on iron recovery and dephosphorization
The effect of CaCO 3,Na 2 CO 3,and CaF 2 on the reduction roasting and magnetic separation of highphosphorus iron ore containing phosphorus in the form of Fe 3 PO 7 and apatite was investigated. The results revealed that Na 2 CO 3 had the most significant effect on iron recovery and dephosphorization, followed by
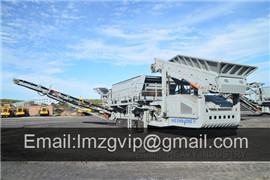
Development of a novel magnetic separator for
The concept of particle separation by rotating magnetic field was proposed by Dean and Devis (Reginald Scott Dean, xxxx; Dean and Davis, 1941).The rotating magnetic field utilized magnetic anisotropy (that depends on exchange forces and crystalline electric fields) and dynamic magnetization response of particles that aid to reduce dependency on
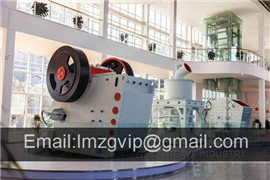
Magnetic Separation SpringerLink
Magnetic particles are carried by the conveyor belt and remain attached to it until they pass through the magnetic field region. On the other hand, nonmagnetic particles, which are not affected by magnetic force, are discharged over the pulley. Dry magnetic separation of iron ore of the bakchar deposit. Procedia Chem. 15, 160–166

Developments in the physical separation of iron ore:
Abstract. This chapter introduces the principle of how lowgrade iron ores are upgraded to highquality iron ore concentrates by magnetic separation. Magnetite is the most magnetic of all the
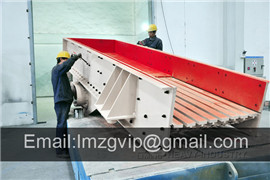
Complex measurement of parameters of iron ore magnetic
The method of automatic measurement of the ore particles density in the pulp flow by measuring the amount of highfrequency volume ultrasonic oscillations attenuation, which have passed a fixed

Iron Recovery from Bauxite Residue Through Reductive
The scope of this work is to develop and optimize a reductive roasting process followed by wet magnetic separation for iron recovery from bauxite residue (BR). The aim of the roasting process is the transformation of the nonmagnetic iron phases found in BR (namely hematite and goethite), to magnetic ones such as magnetite, wüstite, and
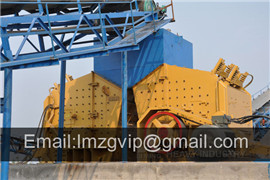
Separation process of iron ore,iron ore magnetic
When the grinding particle size is greater than 0.2mm, most iron ore magnetic separation plants usually use one stage grindingmagnetic separation; If qualified tailings are separated in the rough grinding stage, the iron ore magnetic separation plant should adopt the stage grindingmagnetic separation process; For arid and water

Magnesite Ore Processing: Separation and Calcination
Step 3 Grinding: Use a ball mill to grind the raw ore to 95%0.074mm. Step 4 Magnetic separation: Use a magnetic separator to remove iron impurities in the pulp. Step 5 Flotation: Adopt the amine collector to float the quartz onto the froth and keep the magnesite concentrate in the flotation cell.
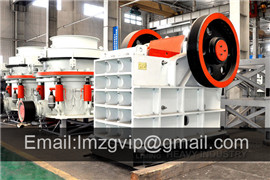
Increasing efficiency of iron ore magnetic separation by
Increasing efficiency of iron ore magnetic separation by using ultrasonic technologies Vladimir Morkun1,*, Natalia Morkun1, Vitalii Tron1, processes and treatment of ore particles by controlled highenergy ultrasound, in particular, by forming cavitation processes in iron ore slurry [1113]. The research is aimed efficiency of separation.
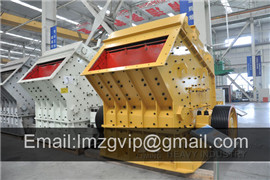
Recovery of magnetitehematite concentrate from iron
To recover magnetite from tailings we used magnetic separation. Magnetic fraction contained 59.3% of Fe total and recovered 89% of Fe mag (table 2). Table 2. The results of the first stage of magnetic separation. Produc t Yield, % Fe content, % Fe recovery, % Tot Mag Hem Tot Mag Hem Magnetic 18.0 59.3 55.5 2.4 52.5 89.0 8.2 Nonmagnetic

Effect of additives on iron recovery and dephosphorization
The effect of CaCO 3,Na 2 CO 3,and CaF 2 on the reduction roasting and magnetic separation of highphosphorus iron ore containing phosphorus in the form of Fe 3 PO 7 and apatite was investigated. The results revealed that Na 2 CO 3 had the most significant effect on iron recovery and dephosphorization, followed by

Development of a novel magnetic separator for
The concept of particle separation by rotating magnetic field was proposed by Dean and Devis (Reginald Scott Dean, xxxx; Dean and Davis, 1941).The rotating magnetic field utilized magnetic anisotropy (that depends on exchange forces and crystalline electric fields) and dynamic magnetization response of particles that aid to reduce dependency on
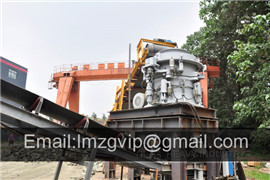
Maximizing the recovery of fine iron ore using
The recovery of fine iron ore by magnetic separation will decrease with decreasing particle size because the magnetic susceptibility of magnetic particles decreases with a decrease in particle mass. There is an

Complex measurement of parameters of iron ore magnetic
The method of automatic measurement of the ore particles density in the pulp flow by measuring the amount of highfrequency volume ultrasonic oscillations attenuation, which have passed a fixed

Minerals Free FullText Separation Analysis of New
To achieve the utilization of fine ilmenite (especially −0.075 mm) produced in the titaniummagnetite processing plant in Panzhihua, a radial turbulent outercylinder magnetic separator (RTOCMS), was developed in this study. After optimizing the conditions of rotation speed and water flow, an RTOCMS concentrate with TiO2 grade of 22.84%
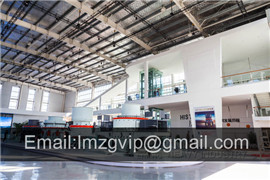
Wet High Intensity Magnetic Separation
WHIM is the short acronym for Wet High Intensity Magnetic Separation . At present, most U.S. iron raw materials are produced from magnetic taconites, which are ground to a nominal minus 270 mesh (53

Magnetic Ore Separator Metallurgist
The main commercial objects of magnetic separation are, first, the diminution of the amount of earthy gangue, with a consequent increase of the percentage of metallic iron in the product, and, second,
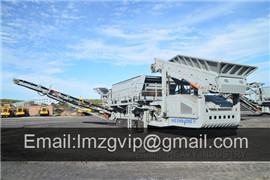
Magnesite Ore Processing: Separation and Calcination
Step 3 Grinding: Use a ball mill to grind the raw ore to 95%0.074mm. Step 4 Magnetic separation: Use a magnetic separator to remove iron impurities in the pulp. Step 5 Flotation: Adopt the amine collector to float the quartz onto the froth and keep the magnesite concentrate in the flotation cell.
- rock and soil classifier screens
- machine tools catelogue downloaded
- الغرانيت مكافحة الفك محطم للبيع
- آلات تعدين النحاس المصبوب المفتوحة
- مصانع غسيل رمل السيليكا في مصر
- بيع رافعات شوكية ماكينات تعدين الفحم
- شراء درجة عالية بأسعار رخيصة كاشطة
- مطحنة الكرة المستمرة مصنعين عمان
- كسارة مخروطية الموردين في الجزائر
- الشركات التي تنقب الجرانيت في mtoko
- سعر الحزام الناقل للرخام في موريتانيا
- موارد مصنع معالجة الذهب والنحاس
- Process Engineering Jobs In Alumina Refinery
- الشركة المصنعة لمعدات معالجة المعادن والتعدين
- کوچک سنگ شکن بتن های قابل حمل
- portable rotary kiln with burner and blower
- فرآیند سودآوری سنگ آهن در هند
- كيفية تصميم من صنع الرمل آلة
- خام الحديد مطحنة الكرة طحن الرطب
- آلة الطحن للجص باريس في مصر