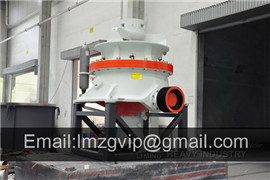
Consumption of steel grinding media in mills A review
Pintaude et al. (2001) have considered the effect of particle size on the abrasive wear of highchromium white cast iron mill balls. They have concluded that the ratio of steel ball to particle size is the critical factor. Effect of abrasive mineral on alloy
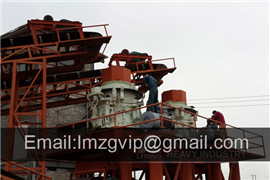
Investigation on the particle size and shape of iron ore
Investigation on the particle size and shape of iron ore pellet feed using ball mill and HPGR 909 areas of 500–1600 cm2 g1.The concentrate must therefore be reground in order to

Ball Mill Explained saVRee
For both wet and dry ball mills, the ball mill is charged to approximately 33% with balls (range 3045%). Pulp (crushed ore and water) fills another 15% of the drum’s volume so


Ball Mill Used in Minerals Processing Plant Prominer
Ball Mill. This ball mill is typically designed to grind mineral ores and other materials with different hardness, and it is widely used in different fields, such as ore dressing, building

Iron Ore: Sedimentary Rock Pictures, Definition
Earth's most important iron ore deposits are found in sedimentary rocks. They formed from chemical reactions that combined iron and oxygen in marine and fresh waters. The two most important minerals in these

The Ultimate Guide to Ball Mills miningpedia.net
The replacement of the ball mill liner is a very cumber some and technically highquality work. In addition to the above mentioned replacement
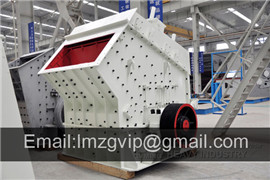
News What is a ball mill used for? hgminingparts
A ball mill, a type of grinder, is a cylindrical device used in grinding (or mixing) materials like ores, chemicals, ceramic raw materials and paints. Ball mills rotate around a horizontal
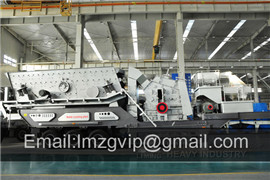
Guidance of Ball Mill Steel Balls Miningpedia
01 Specification of Ball Mill Steel Ball. Back. In general, the diameter of ball mill steel balls is between Φ20mm and Φ125mm, of which small steel balls are

Why use Different Size Balls in a Mill
In test 3, in which the grid was used to segregate the different sizes of balls, a further advantage of about 4 percent in efficiency is shown. The conical mill in test 4 increased the efficiency to 58 percent

The Effect of Grinding Media on Mineral Breakage
The breakage and liberation of minerals are the key to fluidized mining for minerals. In the ball milling process, steel balls function as not only a grinding action implementer but also energy carrier to determine the breakage behavior of ores and the production capacity of the mill. When ground products present a much coarse or much
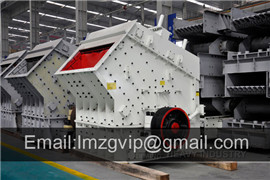
Advances in Mechanical Engineering , Vol. 13(3) 1–9
Ball mill is an energyintensive device for grinding and breaking iron ore particles, which is extensively used in mineral, cement, chemical, and other industries.1–4 In the field of mineral processing, a portion of the energy is converted into heat that will raise the milling temperature and breakage characteristics of iron ore will

Optimization of Solids Concentration in Iron Ore Ball
Important advances have been made in the last 60 years or so in the modeling of ball mills using mathematical formulas and models. One approach that has gained popularity is the population balance model, in particular, when coupled to the specific breakage rate function. The paper demonstrates the application of this methodology to
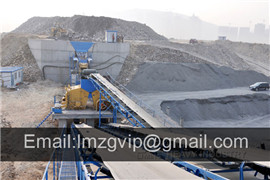
Ball Mill an overview ScienceDirect Topics
Conical Ball Mills differ in mill body construction, which is composed of two cones and a short cylindrical part located between them (Fig. 2.12).Such a ball mill body is expedient because efficiency is appreciably increased. Peripheral velocity along the conical drum scales down in the direction from the cylindrical part to the discharge outlet; the helix

(PDF) Grinding in Ball Mills: Modeling and
Scale Ball Mill. Minerals Engineering, V ol. 22, 2009, 660664. 19. F u e r s t e n a u, D. W., A. Z. M. The balls mills were then compared based on several indicators of energy efficiency
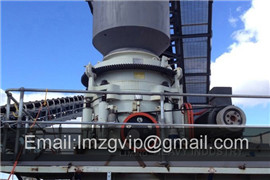
(PDF) Comminution in mineral processing ResearchGate
ball mill, rods, tube mill etc. Mainly, the active fo rce behind crushing is compression or impact and the common operation for grinding is attrition[14] (Figure 4.1). Figure 4. 1 Concept behind
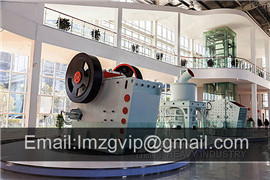
Grinding Mills Mineral Processing Equipment
To date, CITIC HIC has cumulatively produced and delivered over 1,550 mineral grinding mills, with a total installed power of 3,900MW. Our largesize grinding mills hold a market share of 85% in
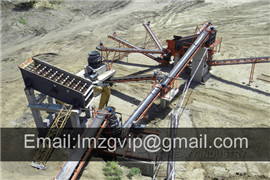
Ball Mill Ball Mills Wet & Dry Grinding DOVE
DOVE small Ball Mills designed for laboratories ball milling process are supplied in 4 models, capacity range of (200g/h1000 g/h). For small to large scale operations, DOVE Ball Mills are supplied in 17 models, capacity range of (0.3 TPH 80 TPH). With over 50 years experience in Grinding Mill Machine fabrication, DOVE Ball Mills as
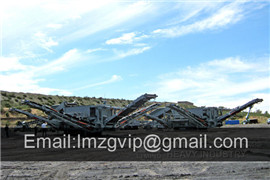
Grinding Balls & Rods Mineral Processing
Grinding Balls. Steel balls ranging from ¾ to 5 in. in diameter are used. Rods range from 1½ to 4 in. in diameter and should be 3 to 4 in. shorter than the inside mill length. Tube mills are usually fed balls
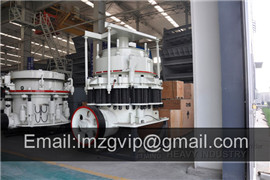
Interesting and Useful Facts about Iron
Iron Facts. Iron is an element that has been known in its pure form for at least 5,000 years. The name "iron" comes from the AngloSaxon word "iron" and Scandinavian "iarn" for the metal. The element

The Effect of Grinding Media on Mineral Breakage
The breakage and liberation of minerals are the key to fluidized mining for minerals. In the ball milling process, steel balls function as not only a grinding action implementer but also energy carrier to determine the breakage behavior of ores and the production capacity of the mill. When ground products present a much coarse or much

Energy Use of Fine Grinding in Mineral Processing
Fine grinding, to P80 sizes as low as 7 μm, is becoming increasingly important as mines treat ores with smaller liberation sizes. This grinding is typically done using stirred mills such as the Isamill or Stirred Media Detritor. While fine grinding consumes less energy than primary grinding, it can still account for a substantial part of a mill’s
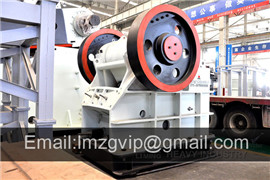
Ball Mill Explained saVRee
For both wet and dry ball mills, the ball mill is charged to approximately 33% with balls (range 3045%). Pulp (crushed ore and water) fills another 15% of the drum’s volume so that the total volume of the drum is 50% charged. Pulp is usually 75% solid (crushed ore) and 25% water; pulp is also known as ‘ slurry ’.
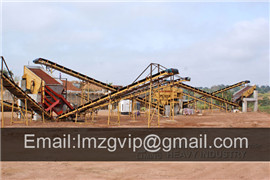
Grindability Studies of Mineral Materials of Different
These studies have been carried out to compare the grinding characteristics of different morphological mineral matters. Coal, dolomite, manganese and iron ores samples were ground using a ball mill in different grinding conditions (dry and wet) and at different critical speed (R 45%, R 70% and R 90%) during wet grinding.
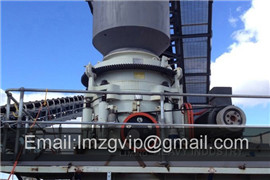
Iron Geoscience Australia
Iron is the backbone of the world we have built around us and it is the basic ingredient of steel (iron plus carbon). Iron is a very useful metal because it can be mixed with other metals to make a whole variety of
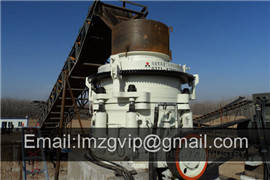
Ball Mill Ball Mills Wet & Dry Grinding DOVE
DOVE small Ball Mills designed for laboratories ball milling process are supplied in 4 models, capacity range of (200g/h1000 g/h). For small to large scale operations, DOVE Ball Mills are supplied in 17 models, capacity range of (0.3 TPH 80 TPH). With over 50 years experience in Grinding Mill Machine fabrication, DOVE Ball Mills as

Stainless steel grinding balls for mining / ball mill
Grinding balls for ball mill use are used in many areas of mining and industry to pulverise and grind. Grinding balls for mining are generally used to break down secondary materials such as rock, cement and stone during the
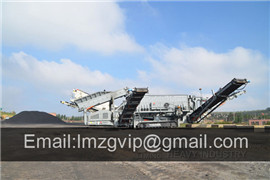
The Ultimate Guide to Ball Mills miningpedia.net
The replacement of the ball mill liner is a very cumber some and technically highquality work. In addition to the above mentioned replacement techniques, the personal safety of the staff is particularly needed. Correct ball mill liner replacement operation can improve the use time of the ball mill and ensure the safe operation of the

Iron (Element) Facts, History, Where It Is
Iron is mostly obtained from minerals hematite and magnetite. In smaller degrees, it can also be obtained from the minerals taconite, limonite and siderite, according to Jefferson Lab .
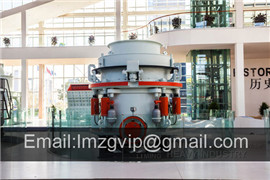
Buy Ore Ball Mill for Mineral Processing Iron & Gold Ore
Ore Ball Mill. Output size: 0.0740.89mm. Motor power: 18.5480kw. Specification (mm): Φ750×750Φ2700×4500. Applications: It is used for processing various grindable mineral materials, nonferrous metal mineral processing, new building materials, etc. Email: info@ballmillssupplier. Now.
- تقنية غسيل الذهب بالمملكة العربية السعودية
- المحمولة الدولوميت مخروط سعر محطم في أندونيسيا
- المعدات المستخدمة في التكسير والطحن
- تعدين الذهب في كوستاريكا
- المورد خام النحاس في مصر
- تكاليف تشغيل كسارة مخروطية
- کیسه های برای استخراج از معادن تن
- خام الحديد المصنع الرجعية للبيع
- بيع كسارة مخروطية متنقلة من الكروم
- قطع غيار كسارة تصادمية للبيع في مصر
- Costs Operation Rock Crusher Quarry Australia
- صورة واستخدامات معدات التعدين
- مصنع كسارة الحجارة في مصر
- محطة غسيل الفحم المستعملة للبيع
- عملية الطاحن الفحم في مصانع الدرفلة الصلب
- نام از تولید کنندگان صفحه نمایش دانه در کلگری
- تصميم كسارة مخروطية بقدرة 650 طن في اليوم
- بورتلاند الكلنكر الأسمنت طحن مطحنة
- تصميم كسارة الاسمنت قوات الدفاع الشعبي
- corrugated roller grinding machine