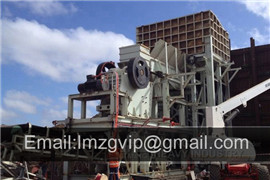
Advances in Sintering and Pellet Technology MDPI
The objective of iron ore agglomeration is to generate a suitable product of granules in terms of thermal, mechanical, physical, and chemical properties.
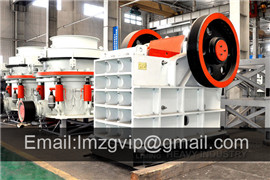
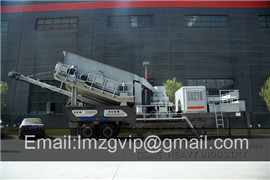
Iron ore pelletization ScienceDirect
Although iron ore concentrates are generally higher in iron grade and contain lower impurities, the finer size distribution of concentrates limits their usage in


Iron Ore Sintering: Process: Mineral Processing and
Sintering is a thermal agglomeration process that is applied to a mixture of iron ore fines, recycled ironmaking products, fluxes, slagforming agents, and solid fuel
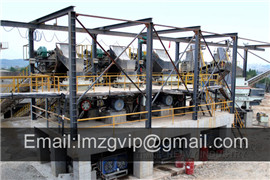
Alternative to deal with high level of fine materials in iron
Nowadays, as the demand for iron ore increases together with the depletion of high grade ore deposits, mining companies have been investing to produce iron ore
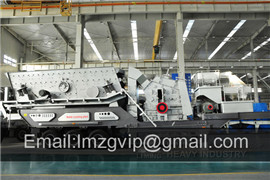
(PDF) Iron ore pelletization ResearchGate
The iron ore pelletizing process has been studied by using a statistical mathematical model to predict and optimize the
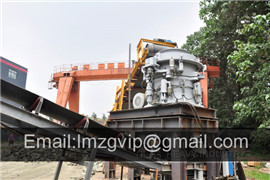
(PDF) Iron Ore Sintering: Process ResearchGate
et al. ), nodulizing, sintering, and pelletizing. Sintering is a th ermal agglome ration proce ss (1300148 0°C, been the main technology for iron ore sintering (Ghosh and.
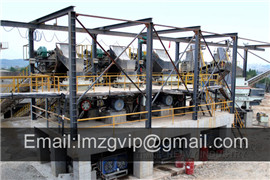
(PDF) Iron Ore Pelletizing Process: An Overview
Solid state sintering in the induration of iron ore pellets. Metallurgical Transactions. 1974; 5:991999 The use of binders for iron ore pelletizing is required to: (a) increase the pellet

Sintering: A Step Between Mining Iron Ore and Steelmaking
The remaining 2% of domestic iron ore was produced for nonsteel end uses. Seven openpit iron ore mines (each with associated concentration and pelletizing

Sintering and Pelletizing Fruitful Outotec
Ensure your plant’s high performance and profitability while lowering investment and operating costs with our agglomeration technologies. Our innovative sintering and
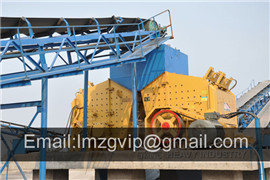
SINTERING AND PELLETISATION OF INDIAN IRON ORES
Emission Optimized Sintering (EOS®) for lower costs Iron ore sintering creates substantial offgas volumes, and treating these in order to meet increasingly
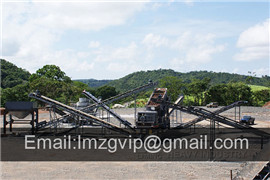
Advances in Sintering and Pellet Technology MDPI
The objective of iron ore agglomeration is to generate a suitable product of granules in terms of thermal, mechanical, physical, and chemical properties. Agglomeration processes are typically of three types: pelletizing, briquetting, and sintering. Sintering is a manufacturing technology to make a wide variety of engineering materials
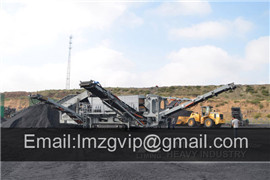
Iron ore pelletization ScienceDirect
Although iron ore concentrates are generally higher in iron grade and contain lower impurities, the finer size distribution of concentrates limits their usage in iron ore sintering. Therefore, pelletizing is needed to produce fired pellets from concentrates as burden materials for blast furnaces and direct reduction processes.

Iron Concentrate Particles MDPI
Iron ore concentrate is an output product from processed iron ores that have been milled (crush, grind, magnetic separation, flotation) to separate deleterious elements and produce a highquality product. Sintering and pelletizing are economic and widely used agglomeration processes to prepare iron ore fines/iron concentrate for
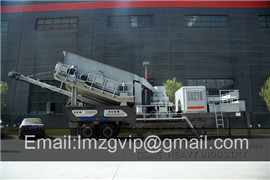
A Process Intensification Approach to Improve
The PI approach is also a pathfinding tool to achieve carbon neutrality and net zero. Intensification of the iron ore sintering process was approached by injecting hydrogenrich gas into the sinter bed. The location of the injection was critical to the pyrolysis of the solid fuel, and the SOx and NOx emissions. After installing the injection
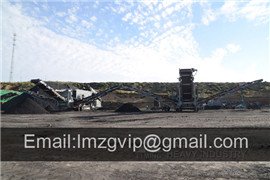
The impact of cautious coal power phaseout on
In this way, IS production is divided into the processes of sintering, pelletizing, coking, ironmaking, and steelmaking. More in detail, Decarbonization of the iron and steel industry with direct reduction of iron ore with green hydrogen. Energies, 13 (3) (), p. 758. CrossRef View in Scopus Google Scholar. BurchartKorol, 2013.

Iron processing Ores Britannica
Iron ore sintering consists of heating a layer of fines until partial melting occurs and individual ore particles fuse together. Pelletizing. First, moistened concentrates are fed to a rotating drum or an inclined disc, the tumbling action of which produces soft, spherical agglomerates. These “green” balls are then dried and hardened by
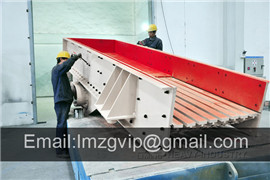
Development of Ironmaking Technology by the Direct
without pelletizing or sintering, especially without the use of coke. This plenary lecturedescribes twosuchprocesses developed attheUniversityof Utah. Oneisthe FlashIronmakingTechnology(FIT)[2–8],andtheotherisamovingbedprocessfor continuous ironmaking with gaseous reduction of iron ore concentrate (MBIT) [9]. Flash Ironmaking

SINTERING AND PELLETISATION OF INDIAN IRON ORES
Emission Optimized Sintering (EOS®) for lower costs Iron ore sintering creates substantial offgas volumes, and treating these in order to meet increasingly stringent environmental standards is expensive. EOS® uses recycling technology to reduce offgas volumes by 40 to 50 %, resulting in smaller secondary gas treatment systems.
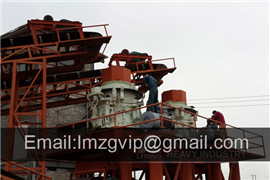
091102 Iron ore European Commission
Iron ore roasting or sintering including pelletisation 3 There are six pelletizing plants at mining sites, which are technically integrated and summarized as three installations. 1 All installations are situated in Sweden, there is one further integrated steel plant in the EU27 in the Netherlands, where pellet
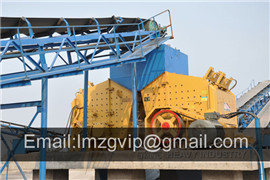
Research Progress of Intelligent Ore Blending Model
The iron and steel industry has made an important contribution to China’s economic development, and sinter accounts for 70–80% of the blast furnace feed charge. However, the average grade of domestic iron ore is low, and imported iron ore is easily affected by transportation and price. The intelligent ore blending model

Efficient Utilization of CarbonBearing Dusts in Composite
Raw Materials. The main raw materials were ironbearing materials, fluxes, and coke breeze, all provided by Baosteel, China. The ironbearing materials included iron ore fine, return fine, and four types of carbonbearing dusts (dusts A–D) which were collected from sintering plant, BF electrostatic precipitator, transportation region between
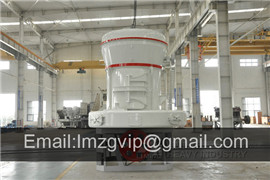
Iron Concentrate Particles MDPI
Iron ore concentrate is an output product from processed iron ores that have been milled (crush, grind, magnetic separation, flotation) to separate deleterious elements and produce a highquality product. Sintering and pelletizing are economic and widely used agglomeration processes to prepare iron ore fines/iron concentrate for
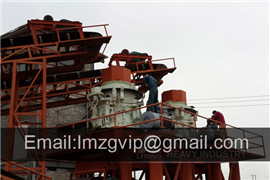
Iron Ore Sintering: Process: Mineral Processing and
Sintering is a thermal agglomeration process that is applied to a mixture of iron ore fines, recycled ironmaking products, fluxes, slagforming agents, and solid fuel (coke). The purpose of the sintering process is manufacturing a product with the suitable characteristics (thermal, mechanical, physical and chemical) to be fed to the blast
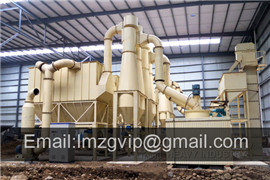
Sintering Behavior of Pelletizing Feed in Composite
The compressive strength, FeO content and microstructures of roasted samples were investigated. The results show that pelletizing feed either from magnetite ore hematite concentrate can be indurated under the conditions of conventional iron ore sintering. Hematite pelletizing feed has better sintering property than magnetite pelletizing feed.
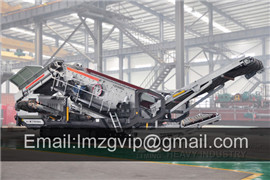
A Process Intensification Approach to Improve
The PI approach is also a pathfinding tool to achieve carbon neutrality and net zero. Intensification of the iron ore sintering process was approached by injecting hydrogenrich gas into the sinter bed. The location of the injection was critical to the pyrolysis of the solid fuel, and the SOx and NOx emissions. After installing the injection
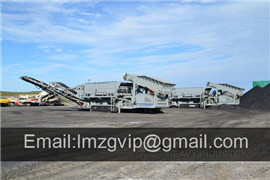
The impact of cautious coal power phaseout on
In this way, IS production is divided into the processes of sintering, pelletizing, coking, ironmaking, and steelmaking. More in detail, Decarbonization of the iron and steel industry with direct reduction of iron ore with green hydrogen. Energies, 13 (3) (), p. 758. CrossRef View in Scopus Google Scholar. BurchartKorol, 2013.

Iron processing Ores Britannica
Iron ore sintering consists of heating a layer of fines until partial melting occurs and individual ore particles fuse together. Pelletizing. First, moistened concentrates are fed to a rotating drum or an inclined disc, the tumbling action of which produces soft, spherical agglomerates. These “green” balls are then dried and hardened by

Development of Ironmaking Technology by the Direct
without pelletizing or sintering, especially without the use of coke. This plenary lecturedescribes twosuchprocesses developed attheUniversityof Utah. Oneisthe FlashIronmakingTechnology(FIT)[2–8],andtheotherisamovingbedprocessfor continuous ironmaking with gaseous reduction of iron ore concentrate (MBIT) [9]. Flash Ironmaking
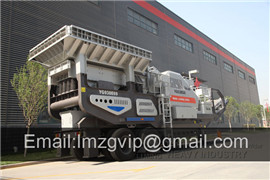
Fruitful Heavy Industries, Ltd. Global Website
HYFOR (Hydrogenbased FineOre Reduction) is a novel direct reduction process for iron ore fines concentrates from ore beneficiation, developed by MHI Group company Primetals Technologies. It builds on fluidizedbed reduction technology, does not require any agglomeration (such as sintering or pelletizing), and uses on 100% hydrogen
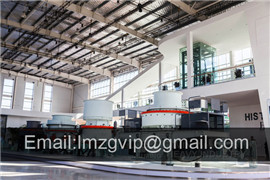
Effect of Blaine Fineness on the Quality of Hematite Iron
Iron ore pellets are largely characterized by inherent physical and chemical properties of ore as well as pelletizing conditions including induration time, induration temperature, etc. These parameters essentially vary with types of ores. The production of highquality pellets from hematite ore is challenging because of high level of fineness (Blaine number) and
- صنع الرمل الاصطناعي في تاميل نادو
- تقرير مشروع كسارة الحجر بصيغة pdf
- زنگ های سنگ شکن مخروطی در ساعت
- طلب عمل فى دولة الكويت سائق لودر ومعدات ثقيلة
- كسارة مخروط متنقلة للبيع الجزائر
- طاحونة الخبث للبيع في باكستان
- خرد کردن را با شما نقل قول
- قدرة المتنقلة محطة كسارة
- مصنعي أجزاء كسارة الحجر الجيري
- سعر مطحنة الكرة أوريون فائقة الألبي
- الرماد المتطاير لصنع الخرسانة
- مرشح كسارة لينكولن 4160b
- مواصفات المواد المطرقة محطم الفحم
- Portable Crusher Machine In Philippines For Coal
- no of crushers required in cement plant
- Mineral Wet Ball Mill Technology
- مطاحن عمودية للبيع في ولاية ويسكونسن
- كسارة متنقلة صغيرة بسعر مفض
- مصنع مطحنة البنتونيت أوروبا
- تصاميم الحصى غرامة كسارة