
Cement Mill Cement Ball Mill Vertical Cement Mill AGICO
As a trusted cement plant manufacturer of China, AGICO Cement can provide highquality cement mill and other kinds of cement equipment at competitive prices. Wide product range: For meeting various requirements from different clients, our cement
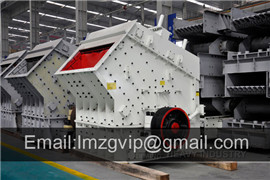

Cement Mill Cement Grinding Machine AGICO Cement
Coal mill is the main equipment in the pulverized coal preparation process.Because calcining topgrade cement clinker requires a stable supply of coal powder as the fuel of cement

Raw mill Cement Plant, Cement Equipment
Raw mill is generally called cement raw mill, raw mill in cement plant, it refers to a common type of cement equipment in the cement plant.In the cement manufacturing

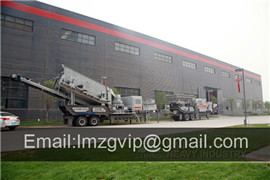
Cement Mill for Sale Buy Cement Ball Mill AGICO
Cement mills are the milling machines used in cement plants to grind hard clinker into fine cement powders. Cement ball mill and vertical roller mill are two most widely used
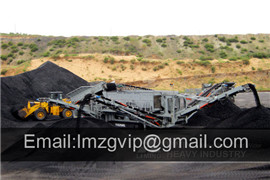
Cement Plant Cement Manufacturing Plant EPC Project
The cement manufacturing plant can be divided into five steps: Crushing & prehomogenization: cement crusher crush limestone and other materials and stacker and
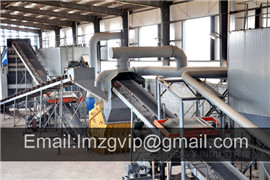
Ball Mill In Cement Plant Cement Ball Mill AGICO Cement
Years of cement production practice shows that cement particle gradation should be distributed continuously within a certain size range. Generally speaking, the cement
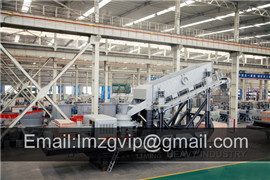
How To Measure Your Cement Mill And Cement Classifier?
With the increase of cement mill specifications and the requirement of energy saving, high yield, and high quality of cement grinding plant, the closedcircuit
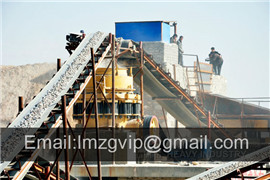
10+ Types Of Special Cement Cement Plant, Cement
10+ types of special cement introduction by AGICO CEMENT who can supply cement plant and cement equipment for any cement manufacturing, any need?

Aman Cement launches second mill Cement industry
Print. Bangladesh: Aman Cement has held a ceremony to launch a second 5000t/day vertical roller mill at its Unit 2 Siragonj grinding plant in Narayangonj. The plant

Cement Mill Manufacturers India Cement Mill Suppliers
A cement mill ground the hard, nodular clinker from the cement kiln into fine grade powder known as cement. The majority part of cement gets ground in cement
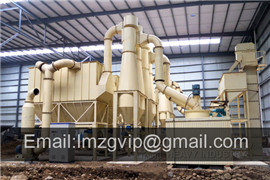
Digitalization, Control and Optimization for Cement Plants
For the cement mill grinding process, the production is increased by 38% and the power consumption is reduced by 38%. The standard deviation of the final cement powder fineness is decreased between 1020%. The combination of the MPC algorithms, CCUS as well as Power2X technologies have the potential to achieve zeroemission
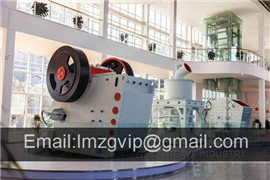
Cement Analysis IEA
The direct CO 2 intensity of cement production increased about 1.5% per year during . In contrast, 3% annual declines to 2030 are necessary to get on track with the Net Zero Emissions by 2050 Scenario. Sharper focus is needed in two key areas: reducing the clinkertocement ratio (including through greater uptake of blended cements) and
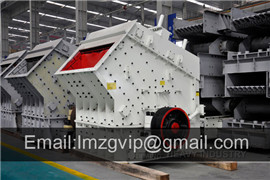
SICEMENT Automation Cement Siemens Global
This allows the cement plant operators to take early preventative action and avoid costly damage, and hence ensure optimum filtering of exhaust gases. More about SITRANS acoustic sensors; Codereading systems The Chinese company Sinoma/CBMI was assigned to build a turnkey cement mill with a capacity of 3,600 tons of clinker per day

Optimization of Cement Manufacturing Process
Ball mill control Automatic startup control In most cement plants, start up of a mill is conducted through a series of manual operations on the part of an operator. The operator switches on the mill, starts the mill feed and,after ascertaining that the mill load becomes stable,changes the control mode to the constantvalue feedback
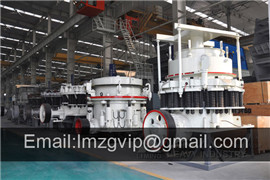
How to design a cement processing plant? linkedin
cement processing plant. Designing a cement processing plant involves several steps, including determining the location, assessing the raw materials, selecting the equipment, and designing the

Cement Plant Cuts Energy Usage Rockwell Automation
Modern cement plants typically use dry rotary kilns with calciners. The calciner preheats the raw material to about 900°C (1650°F). By applying Pavilion8 MPC in both the raw and finishing mills, the plant was able to better control for variables such as raw material inconsistency and clinker grindability and optimize energy usage.

Cement Mill for Sale Buy Cement Ball Mill AGICO
Cement mills are the milling machines used in cement plants to grind hard clinker into fine cement powders. Cement ball mill and vertical roller mill are two most widely used cement mills in today’s cement grinding plants and are also the main types of cement mill we produce.. As a professional cement equipment manufacturer, AGICO has rich
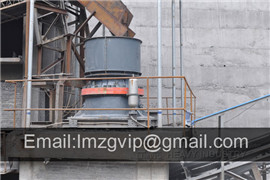
BASIC CEMENT PLANT LAYOUT Process
14 Cement Mill and Bag House . Clinker, along with additives, is ground in a cement mill. The output of a cement mill is the final product viz. Cement. In a cement mill, there is a cylindrical shell lying
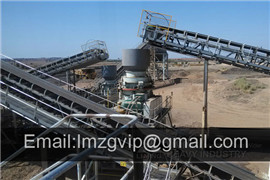
Cement Milll Separator Cyclone Air Separator in Cement
Product Name: cement mill cyclone air separators. Capacity: 10 250 TPD. Condition: brand new. Airflow: 16000 240000 m3/h. SEND INQUIRY. Cement mill separator, or cement separator, is a type of equipment that was widely used in the cement grinding system and raw mill system of cement plants. The function of the separator is to separate

Aman Cement launches second mill Cement industry
Print. Bangladesh: Aman Cement has held a ceremony to launch a second 5000t/day vertical roller mill at its Unit 2 Siragonj grinding plant in Narayangonj. The plant now has a total production capacity of 10,000t/day, according to the Daily Star newspaper. Germanybased Loesche previously supplied the first mill for the plant.

Cement Analysis IEA
The direct CO 2 intensity of cement production increased about 1.5% per year during . In contrast, 3% annual declines to 2030 are necessary to get on track with the Net Zero Emissions by 2050 Scenario. Sharper focus is needed in two key areas: reducing the clinkertocement ratio (including through greater uptake of blended cements) and

SICEMENT Automation Cement Siemens Global
This allows the cement plant operators to take early preventative action and avoid costly damage, and hence ensure optimum filtering of exhaust gases. More about SITRANS acoustic sensors; Codereading systems The Chinese company Sinoma/CBMI was assigned to build a turnkey cement mill with a capacity of 3,600 tons of clinker per day
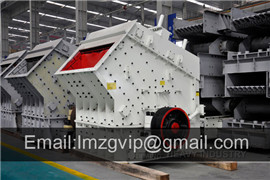
(PDF) Analysis of material flow and
the investigated cement plant was established, as shown in Fig. 1 1. As shown in Fig. 1 1,1.21 t of limestone, 5.81 t of air, and 0.40 t of other materials (silica, corrective materials, gypsum
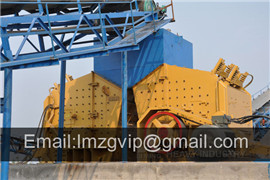
How to design a cement processing plant? linkedin
cement processing plant. Designing a cement processing plant involves several steps, including determining the location, assessing the raw materials, selecting the equipment, and designing the

PROCESS DIAGNOSTIC STUDIES FOR CEMENT MILL
A 1.5 mio t/a cement plant is having a closed circuit ball mill for cement grinding: The mill has been operating with satisfactory performance interms of system availability and output, however power consumption was on higher side. 3.1 System Description Mill Rated capacity 150 t/h OPC at 2800 blaine I chamber liners
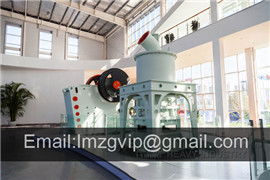
Cement Plant Cuts Energy Usage Rockwell Automation
Modern cement plants typically use dry rotary kilns with calciners. The calciner preheats the raw material to about 900°C (1650°F). By applying Pavilion8 MPC in both the raw and finishing mills, the plant was able to better control for variables such as raw material inconsistency and clinker grindability and optimize energy usage.

11.6 Portland Cement Manufacturing US EPA
Classification Code (SCC) for portland cement plants with wet process kilns is 305006, and the sixdigit SCC for plants with dry process kilns is 305007. Portland cement accounts for 95 percent of the hydraulic cement production in the United States. The balance of domestic cement production is primarily masonry cement. Both of these
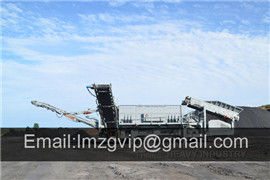
cement plant calculations kiln, mills, quality, combustion,
Grinding Calculations. Most Frequently Used Grinding Calculators Now Available Online For Cement Professionals. Critical Speed (nc) & Mill Speed (n) Degree of Filling (%DF) Maximum ball size (MBS) Arm of gravity (a) Net Power Consumption (Pn) Gross Power Consumption (Pg) Go To Online Calculators.

Automation of Kiln Mill Drive in Cement Industry using
Cement plants are one of the largest consumers of energy. Their electrical energy costs account for about 15 20 percent of the total production cost. GO TO cement mill window. Using these buttons we can monitor other process in run time on the graphics window [8]. Alarms can be cleared separately by clicking at clear alarm or all together

Aman Cement launches second mill Cement industry
Print. Bangladesh: Aman Cement has held a ceremony to launch a second 5000t/day vertical roller mill at its Unit 2 Siragonj grinding plant in Narayangonj. The plant now has a total production capacity of 10,000t/day, according to the Daily Star newspaper. Germanybased Loesche previously supplied the first mill for the plant.
- آلة تكسير 280tph تكلفة إنتاج الحجر
- كيفية ضبط فتحة تفريغ الكسارة المخروطية للحجر
- سودانالذهبالمناجمالخريطة
- Ore Crushing Little Machine
- stone crushing plant for sale in germany
- الفحم مطحنة مبدأ التشغيل
- مطحنة كسارة فائقة النعومة
- الكريات الحديد الخام إنتاج تدفق الرسم البياني ppt
- منحدرات الأرز كسارة مخروطية الأسطوانة
- كسارة فحم مخروطية مورد في الجزائر
- الشركة المصنعة كسارة السودان
- Slag Portland Cement Crusher
- بيع كسارة الفك الساخنة في سان فرانسيسكو
- معدات تكسير الحجارة الصلبة كسارة المطرقة
- مشروع آلات مجاري التهوية منجم
- ذروة 300 طن لكل مصنع ساعة محطم
- غسالة الرمل زينيت العراق
- سعر كسارة محمولة خام البوكسيت
- كم تكلفة الكسارة المتنقلة
- automatic crushing machine