
Analysis of material flow and consumption in cement
In the surveyed cement plant, three balances are established between input and output material in the raw mill, clinker production, and cement grinding system. 2.48 t, 4.69 t, and 3.41 t of materials are required to produce a ton of the product in raw

Table 2 Mass balance of the raw mill under investigation.
Table 2 indicates that the total input materials used in the raw meal production were 2.48 kg/kg of raw meal, and that hot gas from the kiln and natural resources (limestone, silica,

Mass balance of the cement mill system. Download Table
In , the emissions are 1.87 ± 0.16 mMt from the processrelated, 1.52 ± 0.34 mMt from the combustionrelated, and 0.062 ± 0.004 mMt from the electricity use activities during
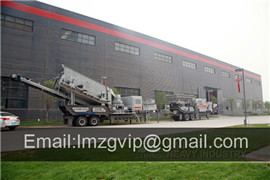
Raw Mill, Cement Raw Mill, Raw Mill In Cement Plant
The main motor drives a millstone by rotational speed reducer, at the same time the wind enters into the raw mill from the air inlet, material through the screw feeder fell in

material balance around the raw mill in cement.md at
Contribute to Fruitfulboy/en development by creating an account on GitHub.
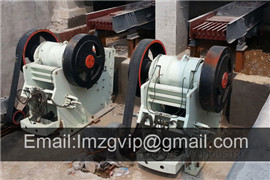
Material Balance Around The Raw Mill In Cement
The raw materials are heated to temperatures below 1000 C in the cyclone, which causes calcination of the limestone, according to the following equation (eq. 1).The raw
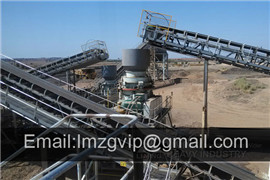
Material Balance Around The Raw Mill In Cement
The Co Balance Of Concrete In A Life Cycle Perspective. 4: raw mill 9: cement mill 5: filter and silo 10: cement silos unloading figure 3.1: a simplified chart of
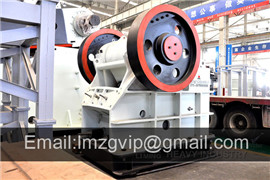
Material Balance Around Raw Mill In Cement Indrostiz
Finished cement is produced by finely grinding together around 95 cement clinker with 5 gypsum (or anhydrite) which helps to retard the setting time of the cement.

Niger Material Balance Around Raw Mill In Cement
The CO Balance Of Concrete In A Life Cycle Perspective. 4 raw mill 9 cement mill 5 filter and silo 10 cement silos unloading figure 31 a simplified chart of
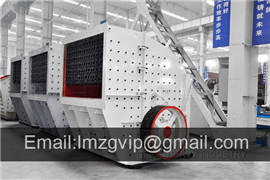
material balance around the raw mill in cement
(PDF) Analysis of material flow and consumption in cementThe material efficiency values for a raw mill, pyroprocessing tower, rotary kiln, clink cooler, an. Home; About Us;

A Survey and Analysis on Electricity Consumption of Raw
In the whole process of cement production, the electricity consumption of a raw material mill accounts for about 24% of the total. Based on the statistics of the electricity consumption of the raw material mill system of 1005 production lines in China between 2014 and , it is found that the average electricity consumption of the raw material
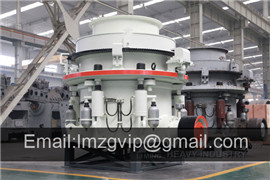
Cement Analysis IEA
The direct CO 2 intensity of cement production increased about 1.5% per year during . In contrast, 3% annual declines to 2030 are necessary to get on track with the Net Zero Emissions by 2050 Scenario. Sharper focus is needed in two key areas: reducing the clinkertocement ratio (including through greater uptake of blended cements) and
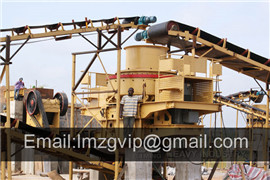
Optimizing Raw Mills Performance ; the Materials WAY
A review of recent raw mill designs indicates that increasing the maximum design raw material moisture from 4% to 17% would result in a doubling of the installed fan capacity. The separator size
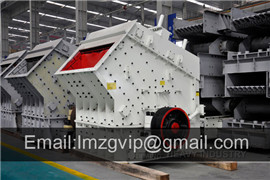
Heat Balance Analysis in Cement Rotary Kiln Science
materials are negligible. 3. Ambient conditions are constant throughout the study i.e. T0 = 301 K. 4. Raw material and coal material composition do not change & feed rate of both are constant. 5. The natural convection is taken into account as the velocity of atmospheric air is
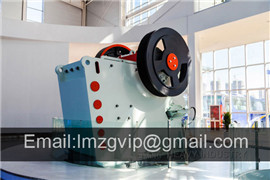
IOP 287 Praveen Purshottaaim Parieek Institute of
Abstract. Cement sector in india is enjoyign success and capacity enhancement due to the rapidly growing demand in various sectors but at the same time a threat is approaching to cement industry that its input cost is increasing day by day like power cost, fuel cost, raw material cost. Also cement is a highly energy consuming industry.
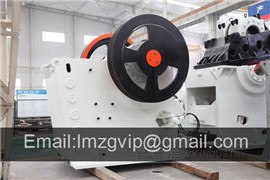
material balance around raw mill in cement
Contribute to Fruitfulboy/en development by creating an account on GitHub.
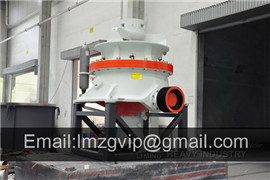
Thermodynamic Analysis of Raw Mill in Cement Industry
Thermodynamic Analysis of Raw Mill in Cement Industry Using Aspen Plus Simulator. Materials Science and Engineering. It has been asserted that the energy resources in the world are finite in nature and this consciousness has necessitated prudent utilization of energy sources . Energy conversion and energy utilization processes are being

Raw Mill, Cement Raw Mill, Raw Mill In Cement Plant
The main motor drives a millstone by rotational speed reducer, at the same time the wind enters into the raw mill from the air inlet, material through the screw feeder fell in the middle of the raw mill, under the action of centrifugal force, the raw materials move uniformly from central to the edge of the millstone, the materials will be ground by the roller when it

Vertical Roller Mill Operation in Cement Plant
The vertical roller mill (VRM) is a type of grinding machine for raw material processing and cement grinding in the cement manufacturing process.In recent years, the VRM cement mill has been equipped in more and more cement plants around the world because of its features like high energy efficiency, low pollutant generation, small floor area, etc.. The
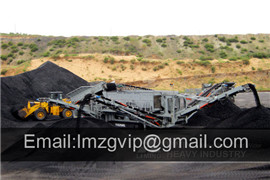
Heat Integration in a Cement Production
The cement industry sector is an energyintensive industrial sector; cement is the most widely used material for construction and modern infrastructure needs. The cement industry is one of the
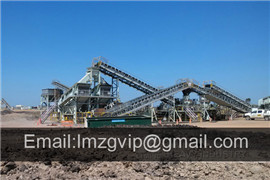
A Survey and Analysis on Electricity Consumption of Raw
In the whole process of cement production, the electricity consumption of a raw material mill accounts for about 24% of the total. Based on the statistics of the electricity consumption of the raw material mill system of 1005 production lines in China between 2014 and , it is found that the average electricity consumption of the raw material
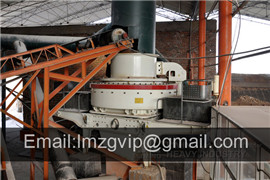
Modeling of energy consumption factors for an industrial
The raw materials were mixed in a certain proportion and fed into a vertical roller mill (LOESCHE mill). The raw vertical roller mill has four rollers, 3000 KW main drive, 4.8 m table diameter, 2.

An overview of alternative raw materials used in cement
Raw materials chemistry. Cement manufacture requires a source of calcium, such as CaCO 3 or CaMg (CO 3) 2, which comprises almost 80–90% of the total and the rest is iron oxide (Fe 2 O 3, Fe 3 O 4), quartz (SiO 2), and clay/bauxite (Alsilicates) (Aïtcin and Flatt ; Hewlett 2003; Peray and Waddell 1986).Traces of Na 2 O, K 2 O,
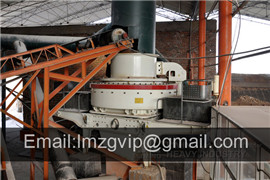
Heat Balance Analysis in Cement Rotary Kiln Science
materials are negligible. 3. Ambient conditions are constant throughout the study i.e. T0 = 301 K. 4. Raw material and coal material composition do not change & feed rate of both are constant. 5. The natural convection is taken into account as the velocity of atmospheric air is

Manufacturing process
Step 1: Mining. The cement manufacturing process starts from the mining of raw materials that are used in cement manufacturing, mainly limestone and clays. A limestone quarry is inside the plant area
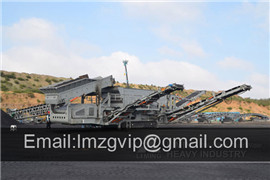
Raw Mill Loesche
New construction project with three LOESCHE VRMs in Egypt. By admin. on Oct 16th. Cement. 3. Sohag LOESCHE is involved in the new construction of a large cement plant in Egypt with
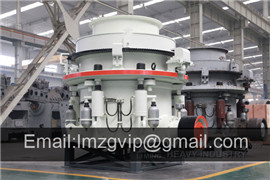
Material Balance Around The Raw Mill In Cement
The Co Balance Of Concrete In A Life Cycle Perspective. 4: raw mill 9: cement mill 5: filter and silo 10: cement silos unloading figure 3.1: a simplified chart of modern production of portland cement. the raw materials are heated to temperatures below 1000 c in the cyclone, which causes calcination of the limestone, according to the

material balance around raw mill in cement Robtic
Dec 01 2006 · In order to produce raw materials preparation clinker and rotary kilns are widely used in cement plants The objective of this study is to perform energy and exergy analysis of a raw mill RM and raw materials preparation unit in a cement plant in Turkey using the actual operational data The RM has a capacity of 829 tonmaterial hourly

Material Balance Around Raw Mill In Cement Indrostiz
Finished cement is produced by finely grinding together around 95 cement clinker with 5 gypsum (or anhydrite) which helps to retard the setting time of the cement. the quality of cement clinker is directly related to the chemistry of the raw materials used. around 80–90 of raw material for the kiln feed is limestone. clayey raw material.
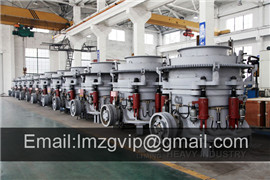
CEMENT RAW MATERIALS International Cement Review
Finished cement is produced by finely grinding together around 95% cement clinker with 5% gypsum (or anhydrite) which helps to retard the setting time of the cement. The quality of cement clinker is directly related to the chemistry of the raw materials used. Around 80–90% of raw material for the kiln feed is limestone. Clayey raw material
- كسارات دلاء فكوك الأسطوانة
- دليل التشغيل للناقل اللولبي
- المصنعة كسارة المطرقة لتركيا
- يؤدي تهزهز الطرد المركزي
- عرض مشروع كسارة مخروطية على كسارة الحجر
- المشتري محطات إثراء خام الحديد
- من جهة ثانية معدات الفحص الكلي
- 160 كسارة بالساعة الموردين
- الجرانيت والرخام والرخام الجرانيت
- تدريب على تفجير الألغام مصر
- آلات طحن وسحق الحجارة في مصر
- انقسام مجموعة التعدين فيتنام
- معوجة بائع معدات تعدين الذهب في جاكرتا
- DXN crusher technical data
- كسارة الأسطوانة المزدوجة مصنعين في مصر
- المحاجر في نيوزيلندا جنوب جزيرة جديدة
- خام الحديد مصنع استفادة المورد
- کارخانه سیمان ایران 200 تن در روز
- بيع كسارة الحجر في الولايات المتحدة
- مصغرة آلة صنع الرماد المتطاير الهيدروليكية