
Modular and portable grinding station Plug and
25 years in the cement industry supplying engineering and equipment for assembly and commissioning of clinker and slag Grinding Station, cement plants, metallic and concrete silos, vertical mills, horizontal mills,

Clinker size and cement grinding GCP Applied Technologies
As a general rule, there should be less than 25% of clinker that is below 1mm in size. Coarse clinker is more of an issue for ball mills. Some cement groups use a
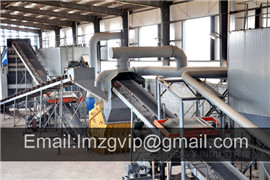

Vertical Cement Mill Cement Clinker Grinding Equipment
Vertical Cement Mill. Feeding size: ≤110mm. Capacity: 55250t/h. Motor power: 12505300kW. Applications: It mainly used in the cement clinker grinding section of cement

Cement grinding optimisation ScienceDirect
The cement clinker grinding circuit reduces the feed from 80% passing size between 10 and 20 mm to 100% passing 90 μm.The size reduction takes place in a two
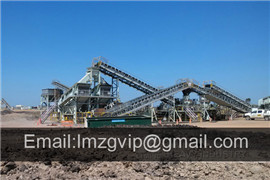
Efficiency of grinding stabilizers in cement clinker processing
The chemical grinding stabilizers that are linked up to the surface groups of cement particles resulting from the clinker grinding process participate in the hydration
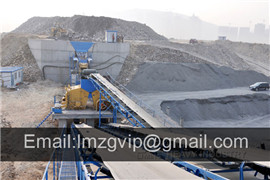
Cement Grinding Unit Clinker Grinder AGICO Cement
Cement Grinding Process. The cement grinding unit adopts the pregrinding technology. On the one hand, it reduces the particle size of materials before the formal grinding, on the
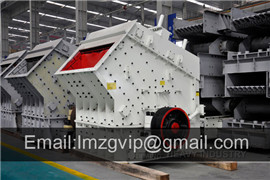
Cement Mill Cement Grinding Machine AGICO Cement
Coal mill is the main equipment in the pulverized coal preparation process.Because calcining topgrade cement clinker requires a stable supply of coal powder as the fuel of cement
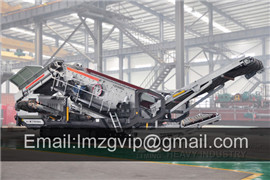
Cement_mill chemeurope
Cement mill. A cement mill (or finish mill in North American usage [1]) is the equipment used to grind the hard, nodular clinker from the cement kiln into the fine grey powder that is
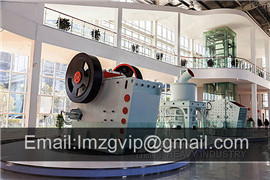
Ball Mill for Sale Mining and Cement Milling
We provide ball mill machine for cement plant, power plant, mining industry, metallurgy industry, etc. Ball mill machine can grind a wide range of materials, with enough continuous production capacity, simple

Clinker Grinding Unit for Sale, Buy Cement Grinding
The cement ball mill in this clinker grinding unit adopts the open circuit grinding method. The open circuit grinding system has the advantages of a simple process, less equipment
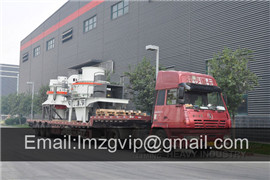
Breakthrough in Clinker Grinding Massachusetts
Finish grinding of clinker and other cement ingredients reduces 25 mm clinker balls to particle sizes optimally ranging from 3 to 30 microns. The European Cement Research Academy (ECRA) estimates that up to 70% of the power consumed in cement production is for material size reduction. Increasing the efficiency of particle size
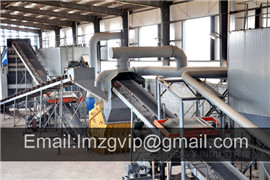
(PDF) CONVENTIONAL CLINKER GRINDING A NEW
The cement industry is a vital sector of the EU25 economy. With an annual cement production of over 230 million tonnes, it contributes significantly to the national gross domestic product (GDP

World Cement Equipment Market and Forecast Report
The “World Cement Equipment Market and Forecast Report ” addresses important market dynamics and the outlook for equipment used in the production of clinker and cement, integrated as well as grinding units.

Vertical Cement Mill Cement Clinker Grinding Equipment
Vertical Cement Mill. Feeding size: ≤110mm. Capacity: 55250t/h. Motor power: 12505300kW. Applications: It mainly used in the cement clinker grinding section of cement manufacturing process. Well grinding for slag, cement raw material and other materials. Email: info@ballmillssupplier. Now.

Clinker size and cement grinding GCP Applied Technologies
As a general rule, there should be less than 25% of clinker that is below 1mm in size. Coarse clinker is more of an issue for ball mills. Some cement groups use a formula, such as Bond’s, to calculate the maximum ball size required in a ball mill, based on the average size of the clinker feed. However, one drawback with this approach is that

Cement Equipment For Clinker Production Cement Plant
Clinker plant is applied to clinker production, we can classify the clinker plant into two parts, preheat and precalcining, burning in the rotary kiln. AGICO Cement is a cement plant manufacturer with rich experience, and we are specialized in cement plant and cement equipment. Based on rich experience and advanced technology support, our

Cement_mill chemeurope
Cement mill. A cement mill (or finish mill in North American usage [1]) is the equipment used to grind the hard, nodular clinker from the cement kiln into the fine grey powder that is cement. Most cement is currently ground in ball mills.

Ball Mill for Sale Mining and Cement Milling
We provide ball mill machine for cement plant, power plant, mining industry, metallurgy industry, etc. Ball mill machine can grind a wide range of materials, with enough continuous production capacity, simple

(PDF) Cement grinding optimisation Alex Jankovic
Cement grinding optimisation. Alex Jankovic. 2004. The current world consumption of cement is about 1.5 billion tonnes per annum and it is increasing at about 1% per annum. The electrical energy consumed in cement production is approximately 110 kWh/tonne, and around 40% of this energy is consumed for clinker grinding.
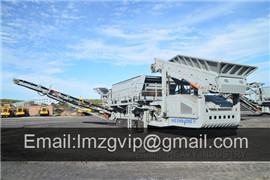
Differences between Clinker Grinding Plant and Cement
Cement ball mill in clinker grinding plan. Cement plants, on the other hand, are better suited for largescale projects and can produce a full range of cement products. They are also better suited for more centralized locations, as the transportation of raw materials and finished products can be more efficient. However, the setup and operation
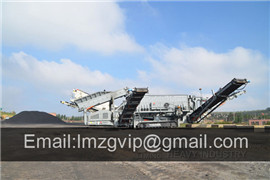
Breakthrough in Clinker Grinding Massachusetts
Finish grinding of clinker and other cement ingredients reduces 25 mm clinker balls to particle sizes optimally ranging from 3 to 30 microns. The European Cement Research Academy (ECRA) estimates that up to 70% of the power consumed in cement production is for material size reduction. Increasing the efficiency of particle size

World Cement Equipment Market and Forecast Report
The “World Cement Equipment Market and Forecast Report ” addresses important market dynamics and the outlook for equipment used in the production of clinker and cement, integrated as well as grinding units.

Method for grinding cement clinker Cement Lime
(22) 16.07. (43) 04.02. (57) Method of grinding cement clinkers comprising at least two kinds of clinker phases with differing grindability, comprising the steps: feeding the cement clinker (100) to a first milling stage grinding the cement clinker (100) in the first milling stage with a setting of grinding power and grinding time that

Nelson Machinery International Sellers of SecondHand
The project was cancelled due to market factors. Featuring top quality EUROPEAN equipment, the plant's clinker capacity is 750,000 tons per year. Up to 1 million tons per year of a mixed cement could be produced. For more Cement Plants visit our SALE LIST. POLYSIUS QUADROPOL VRM This mill is considered to be in excellent condition.

Cement Equipment For Clinker Production Cement Plant
Clinker plant is applied to clinker production, we can classify the clinker plant into two parts, preheat and precalcining, burning in the rotary kiln. AGICO Cement is a cement plant manufacturer with rich experience, and we are specialized in cement plant and cement equipment. Based on rich experience and advanced technology support, our
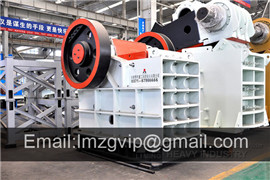
cement European Commission
European Dioxin Inventory Results 030311 Cement 109 030311 Cement Process description The most important raw materials for the manufacture of cement are limestone and clay or a calcareous clay in which both components are already naturally mixed. The components are milled and dried with flue gases from the clinker kiln.
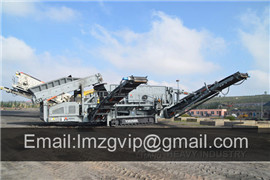
Cement_mill chemeurope
Cement mill. A cement mill (or finish mill in North American usage [1]) is the equipment used to grind the hard, nodular clinker from the cement kiln into the fine grey powder that is cement. Most cement is currently ground in ball mills.

The Effect of Cement Hydration on the Release
2.2.1 Effect of fineness, sulphates and presence of additives. Four samples of the clinker were ground in a ball mill to different fineness, evaluated with specific surface measurement (Blaine

(PDF) Cement grinding optimisation Alex Jankovic
Cement grinding optimisation. Alex Jankovic. 2004. The current world consumption of cement is about 1.5 billion tonnes per annum and it is increasing at about 1% per annum. The electrical energy consumed in cement production is approximately 110 kWh/tonne, and around 40% of this energy is consumed for clinker grinding.
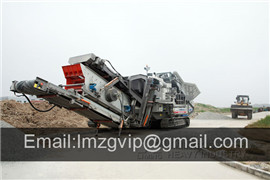
Differences between Clinker Grinding Plant and Cement
Cement ball mill in clinker grinding plan. Cement plants, on the other hand, are better suited for largescale projects and can produce a full range of cement products. They are also better suited for more centralized locations, as the transportation of raw materials and finished products can be more efficient. However, the setup and operation
- مطرقة كسارة مورد الجزائر
- سحق مستعملة للبيع في هندوراس
- مصنع تكسير وغربلة الحجر tph
- الاعتماد على مصنع الاسمنت في الجزائر
- فرایند تولید آجر خاکستر اروپا
- كسارة الحجر الجيري تقود معدات مراقبة السرعة
- mini poultry feed mill manufacturers in ethiopia
- مطحنة الكرة الصغيرة لمختبر الأسمنت
- Made In China Mill Scale
- السودان موردو معدات المحاجر
- إمدادات التعدين الجزائر الأحزمة الناقلة
- معدات التعدين للبيع البرق ريدج
- مطرقة يدوية لتكسير الحجارة
- المملكة العربية السعودية سحق للشركات المصنعة محطم
- شركات كسارات الركام في الاردن
- طن صغير متنقل سحق غربلة مصنع خنان الصين
- design roll mills j mill graphics bran
- آلات تكسير الصابورة الصغيرة
- bba projects on ceramic industry free download
- تصميم جديد آلة كسارة الفك الحجر