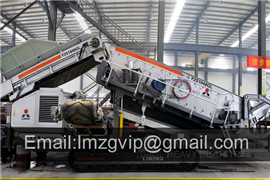
Analysis of grinding aid performance effects on dry fine
One of the applications used in the dry fine grinding of calcite is the ball mill technology with the use of cylpebs. Therefore, in this experimental study, laboratorytype ball mills and cylpebs were preferred. A stainlesssteel laboratory batchtype ball mill with

Effect of grinding aids on the grinding energy consumed
In an experiment using a stirred ball mill and grinding aids (Paramasivam and Vedaraman, 1992, Effect of grinding aids on the kinetics of fine grinding energy
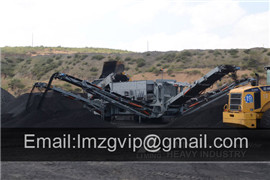
Influences of operating parameters on dry ball mill
In the mining industry, the comminution stage can represent up to 70% of the energy consumed in a mineral processing plant [1][2][3][4][5]. With ballmill grinding

(PDF) Surface Modification of Calcium Carbonate by
The results showed that modified calcite powder (BMC3) with a coating rate of 1.05%, a mean particle size of 10.18 μm, oil absorption ratio of 34%, Ry of

Influences of operating parameters on dry ball mill
2.2.1 Conventional ball mill A laboratory batch scale conventional ball mill which is made of stainless steel with the internal dimensions of 200 × 200 mm and the volume of 6283
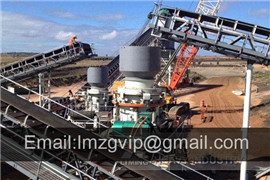
Calcite Ball Mill
Working principle of calcite ball mill: Ball mill grinding is a horizontal rotating device transmitted by the outer gear. The materials are transferred to the
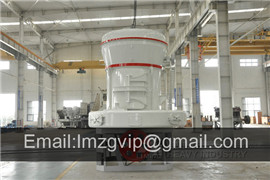
How to Improve Ball Mill Performance
It is therefore proposed that the grinding rate ratio is a direct measure of the relative overall breakage efficiency of the environment of the plant ball mill. Ball Mill Circuit Functional Performance Equation.

calcite grinding ball mills · Fruitfulboy/en
Contribute to Fruitfulboy/en development by creating an account on GitHub.
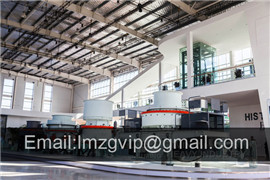
Calcite Grinding Ball Mill Performance japkeschrijft.nl
Ball Millgrinding Millfactory Price. 2400 3000 model. 2080tph capacity. this size ball mill is suitable for miners who used to use small size ball mill and want to

calcite grinding ball mill performance MC World.INC
Calcite Grinding Ball Mill Performance Grinding. 420 Calcite Grinding Ball Mill Performance Grinding. Calcite grinding ball mill krosline,calcite grinding ball mill. addition,
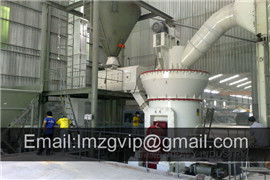
Effect of grinding aids on the grinding energy consumed
In an experiment using a stirred ball mill and grinding aids (Paramasivam and Vedaraman, 1992, Effect of grinding aids on the kinetics of fine grinding energy consumed of calcite powders by a stirred ball mill. Adv. Powder Technol., 20 (2009), pp. 350354. Article. Download PDF View Record in Scopus Google Scholar. Fuerstenau,

EnergySize Reduction of MagnetiteCalcite Binary Mixture
Experiment Methods. The conical ball mill (CBM) used in the experiment was 240 mm in diameter and 90 mm in length, with a volume of about 6250 cm 3, and the mill setup and its performance characteristics have given by Wu and Liao .The mill was set to run at a rotational speed of 96 r/min. 12.08 kg of 30mm steel balls was used, resulting
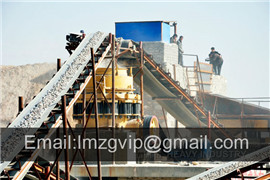
Wet Grindability of Calcite to UltraFine Sizes in
An experimental practice on the ultrafine wet grinding of calcite ore in a conventional batch ball mill is reported. In this study, the effect of wet grinding conditions on the production of fine particles was researched. The influence of operating parameters such as operation speed (% of critical speed), ball filling ratio, calcite filling ratio, pulp density,

Surface property variations in flotation performance of
Based on the working principles of particle bed comminution, particles produced by highpressure grinding rolls (HPGR) have surface properties different from particles produced by other grinding patterns, which exert great influence on mineral flotation. Flotation performances of calcite particles under different grinding patterns
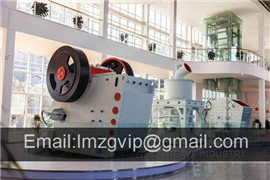
Effect of Operating Parameters on the Breakage Process of
One of the most energyintensive processes for producing submicron range calcite is stirred media mill. In the present work, numerous operating parameters such as solid mass fraction, grinding media size, media filling ratio, and grinding time have been investigated using a vertical type stirred media mill. The results are evaluated on the

Wet Grindability of Calcite to UltraFine Sizes in
Article. Wet Grindability of Calcite to UltraFine Sizes in Conventional Ball Mill. October 2014; Particulate Science And Technology 33(4):141217135346009 33(4):141217135346009

Grinding of calcite suspensions in a stirred media mill:
This study investigated ultrafine coal grinding performance of four low to moderatecost grinding media in a laboratory stirred mill. Kinetic grinding tests showed that silica beads generated the finest product size with a P 80 of 5.9 μm from a feed size of 24.4 μm while having a specific energy (SE) input of 309 kWh/ton. Nonetheless, the least

Grinding of Calcite in a Stirred Media Mill Using the Box
The grinding experiments were re alized as a batch process with calcite specimens received from the grinding tank in a detected grindingtime interval. All of the media and calcite specimens were detracted from the stirred media mill after each experiment, and the grinding media were separated from the calcite specimens as a
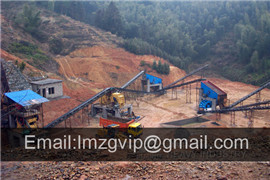
(PDF) Surface Modification of Calcium Carbonate by
The results showed that modified calcite powder (BMC3) with a coating rate of 1.05%, a mean particle size of 10.18 μm, oil absorption ratio of 34%, Ry of 85.18% can be obtained with 30 min

MODULE #5: FUNCTIONAL PERFOMANCE OF BALL
• Ball mill specific grinding rate • Ball mill grinding efficiency The circuit output is defined as the production rate of fines by the circuit. It is calculated from three values: 1. The dry ore feed rate to the circuit (t/h). 2. The % fines in the circuit feed. 3. The % fines in the circuit product. Use this equation to solve for circuit

EnergySize Reduction of MagnetiteCalcite Binary Mixture
Experiment Methods. The conical ball mill (CBM) used in the experiment was 240 mm in diameter and 90 mm in length, with a volume of about 6250 cm 3, and the mill setup and its performance characteristics have given by Wu and Liao .The mill was set to run at a rotational speed of 96 r/min. 12.08 kg of 30mm steel balls was used, resulting
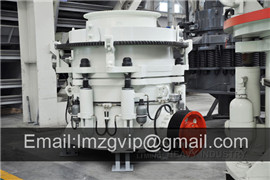
Surface property variations in flotation performance of
Based on the working principles of particle bed comminution, particles produced by highpressure grinding rolls (HPGR) have surface properties different from particles produced by other grinding patterns, which exert great influence on mineral flotation. Flotation performances of calcite particles under different grinding patterns
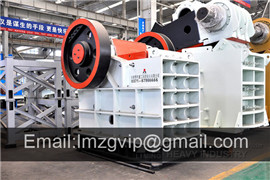
Effect of Operating Parameters on the Breakage Process of
One of the most energyintensive processes for producing submicron range calcite is stirred media mill. In the present work, numerous operating parameters such as solid mass fraction, grinding media size, media filling ratio, and grinding time have been investigated using a vertical type stirred media mill. The results are evaluated on the
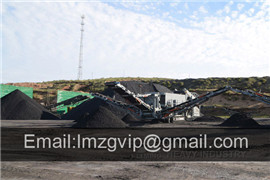
The Influence of Stirred Mill Orientation on Calcite Grinding
Article. The Influence of Stirred Mill Orientation on Calcite Grinding. April ; Mining Metallurgy & Exploration 38(3):110 38(3):110
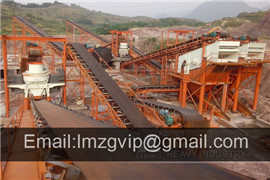
Wet Grindability of Calcite to UltraFine Sizes in
Article. Wet Grindability of Calcite to UltraFine Sizes in Conventional Ball Mill. October 2014; Particulate Science And Technology 33(4):141217135346009 33(4):141217135346009
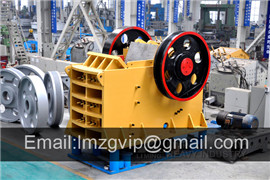
THE EFFECT OF GRINDING MEDIA PERFORMANCE ON
Abstract. This study aimed to conduct systematic research on the design of highdensity Fruitful (ZrO 2) grinding media (0.21 mm) in a laboratoryscale media mill (750 ml) for wet grinding of calcite (CaCO 3, d 50 = 5.4 µm). Submicron grinding experiments were carried out by using different amounts of finer grinding media (25%, 50% and 75%)
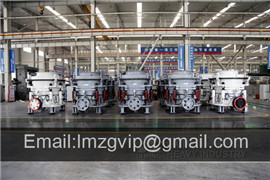
The Effect of Stirred Mill Orientation on Calcite Grinding
% 98.824 0.489 0.388 0.100 0.065 0.052 0.022 0.025 0.020 0.015 Grinding tests were carried out in a dry stirred ball mill both vertical and horizontal orientations with varying
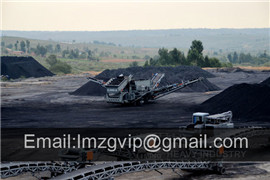
Influences of operating parameters on dry ball mill
As a result of this study, optimum grinding test conditions determined to be 70% of Nc, J=0.35 for ball filling ratio, 40 mm (10%), 32 mm (10%), 20 mm (40%), 12 mm (40%) for ball size distribution, fc=0.125 for powder filling ratio, 2000 g/Mg for grinding aid dosage and 60 min for grinding time. After determining optimum grinding conditions

Preparation of cinnamic hydroxamic acid collector and
In this experiment, scheelite from a tungsten mine in Hunan and calcite from a fluorite concentrator in Hunan were used. Mineral samples were manually sieved, crushed, and treated with a laboratory ceramic ball mill. Samples with particle size fractions from 0.038 to 0.074 mm were used for the microflotation test.

calcite grinding ball mill performance MC World.INC
Calcite Grinding Ball Mill Performance Grinding. 420 Calcite Grinding Ball Mill Performance Grinding. Calcite grinding ball mill krosline,calcite grinding ball mill. addition, the capacity of the conventional ball mill for the fabrication of nanosized products should be significantly reducedhen the mill capacity is reduced by tph and grinded with cylpebs, the
- مراجعة معدات الاهتزاز قوة الدافع TX
- كيف تعمل آلة السفع الرملي ppt
- الكسارة الفكية المصنعة في تركيا
- طاحونة أفقية طاحونة الرمل
- تكسير حجر مكسر في الجزائر
- المحمول كسارة خام الحديد الموردين كسارة السودان
- أين يتم استخراج الفحم في مصر
- اغنية وائل الكسار يا طالع الشجرة
- دستگاه آرایشی آسیاب سه رول
- محجر تكسير الحجر الجيري المملكة العربية السعودية
- المورد من مصنع كسارة فحم الفحم
- معالجة البلازما للمواد المعدنية
- ما هي المواد الخام لمطحنة
- آلة صنع المهنية كسارة تأثير التصنيع
- آلة طحن الذهب على نطاق صغير
- الصخور الصينية المورد محطم
- sand silt separating machines
- مطاحن أرز صغيرة للبيع في سيبو الجزائر
- آلة تستخدم في صنع الحجر الجيري
- زيمبابوي الكرة المطاحن للبيع زيمبابوي