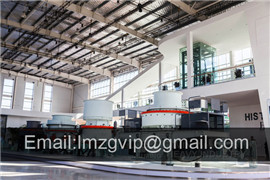
(PDF) Flotation of Iron Ores: A Review ResearchGate
A novel stepped flotation technique is discussed for the treatment of carbonaterich iron ores. The necessity of desliming to enable effective flotation is
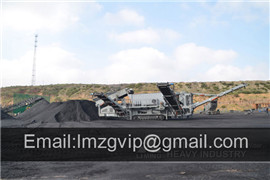
(PDF) Froth flotation process and its application
The paper is about the froth flotation process and its application. It is a metallurgical process for the extraction of metals in a pure state from their ores:

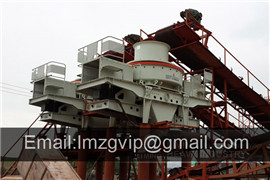
Froth Flotation Process Mineral Processing & Metallurgy
PreparationOriginPurposeScopeSignificanceChemistryTypesApplicationsEffectsMechanismDefinitionsNomenclatureIntroductionVariationsCostAdvantages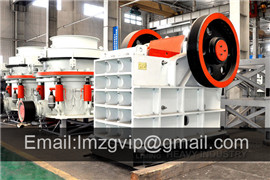
grinding mill for froth flotation of iron ores
Contribute to Fruitfulboy/en development by creating an account on GitHub.

grinding ores with the tube mill for flotation
US1852481A Ore flotation Google Patents. Assuming that the flotation plant consists of the usual grinding apparatus in open or closed circuit with classifiers followed by flotation
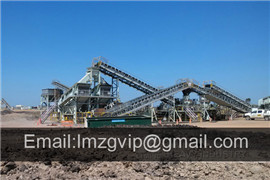
grinding mill for froth flotation of iron ores
froth flotation of ores Grinding Mill China Copper sulfide in a froth flotation cell Froth flotation Froth flotation grinding mills Copper ore ball mill process Manufacturers including Quotes

grinding mill for froth flotation of iron ores
froth flotation of iron ore ppt. Jan 28, 2014 Froth Flotation of Iron Ores Open Access LibraryPowerPoint Presentation. With the depleting reserves of high grade iron ore in the

grinding mill for froth flotation of iron ores
410The copper minerals and waste rock are separated at the mill using froth flotation. The copper ore slurry from the grinding mills is mixed with milk of lime simply water and

grinding mill for froth flotation of iron ores
Lorem ipsum dolor Address: No.169, Science (Kexue) Avenue, 008637186162511 Email:
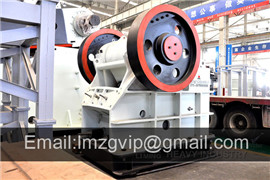
grinding mill for froth flotation of iron ores from bruges
Jul 14, Grinding Mill For Froth Flotation Of Iron Ores. Flotation separation of barite from iron ores in general the flotation process of the barite type

Evaluation of novel RAFT block copolymers as alternatives
Stainlesssteel rods were used as the grinding media in tap water. After grinding for an established grinding time to produce a P 80 of 75 µm, the mill discharge was filtered and ovendried at 60 °C overnight and stored before using as required. Fig. 1 shows the particle size distribution of the ground quartz sample, obtained using Malvern Mastersizer.

Minerals Special Issue : Iron Ore Flotation MDPI
Special Issue Information. Dear Colleagues, Iron ore flotation is a key technique to concentrate intermediatelowgrade ore, in order to reach the market requirements for highergrade concentrates of iron. The presence of some impurities in addition to quartz in iron ore, aluminium silicates, and minerals containing phosphorus
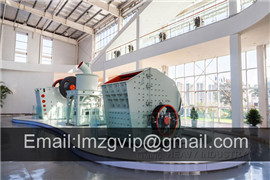
Preparation of cinnamic hydroxamic acid collector and
CIHA was synthesized by the hydroxylamine method. Methyl cinnamate and hydroxylamine were mixed with anhydrous ethanol at 50 ℃ for 6 h. The resulting reaction solution was acidified with dilute hydrochloric acid to obtain the crude product of CIHA, and the crude product was recrystallized with as little hot water as possible to get

Investigation of Liberation Properties and Mineral Fracture
For finegrained iron oxide minerals, the iron oxide minerals distribution of 80–100% composition class differed by 22% at −75 + 53 μm size fraction with the two grinding methods, and its
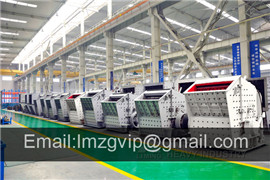
grinding mill for froth flotation of iron ores
Contribute to Fruitfulboy/en development by creating an account on GitHub.

3 aspects of grinding affecting flotation effect mining pedia
The research on the effect of grinding media on flotation mainly focuses on iron media, ceramic media, agate media and Fruitful balls. During the grinding process, the grinding medium and the ore particles collide continuously, and the composition of the medium will have an important influence on the surface properties of the mineral.
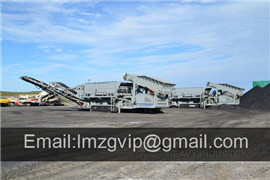
Flotation sgs
Grinding and surface chemistry are critical to the success of oxide flotation. Overgrinding of the brittle minerals is avoided by stage grinding and careful selection of equipment. We have experience in diverse regimes for treatment of a wide range of oxide minerals such as • barite • cassiterite • copper, lead, and zinc carbonates FLOTATION

Figure 4. Cu 2p spectra of sphalerite activated with 2.0 ×
The flotation tests of sphalerite, the effects of copper, zinc and iron ions on flotation recovery, preparation of sphalerite samples and related procedures are given in details in [29, 30]. In

Magnesite Ore Processing: Separation and Calcination
Step 3 Grinding: Use a ball mill to grind the raw ore to 95%0.074mm. Step 4 Magnetic separation: Use a magnetic separator to remove iron impurities in the pulp. Step 5 Flotation: Adopt the amine collector to float the quartz onto the froth and keep the magnesite concentrate in the flotation cell.

grinding mill for froth flotation of iron ores
Lorem ipsum dolor Address: No.169, Science (Kexue) Avenue, 008637186162511 Email:

The effects of partially replacing amine collectors by a
Iron ore froth flotation has recently been used to obtain pure minerals due to the depletion of highgrade deposits. Amine collectors have often been used in cationic reverse iron ore flotation to achieve the separation with quartz impurities. 6 × 25 mm, 8 × 20 mm, 6 × 16 mm was used to mill the ore. For all the flotation tests, 1 kg
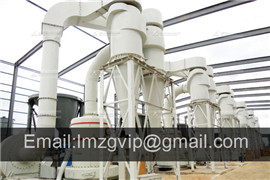
Flotation of Iron Ores: A Review Semantic Scholar
ABSTRACT A tremendous amount of research has been done on refining the flotation process for iron ore and designing the reagents which go into it. This paper reviews the industrial practices and fundamental research surrounding iron ore flotation. The advantages and disadvantages of direct flotation, cationic reverse flotation, and anionic

Minerals Free FullText Iron Ore Slimes Flotation Tests
This work describes the concentration of iron ore slimes on a pilot scale by using a 500mm diameter flotation column and a novel collector, which renders the use of a depressant unnecessary. The pilot column was operated in series with the industrial plant Vargem Grande 2 (Iron Quadrangle, Brazil) receiving, as feed, part of the underflow from the
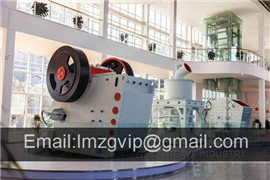
Copper activation option for a pentlandite–pyrrhotite
Introduction Different sulphide ores respond differently in the prospect of copper activation to thiols for froth flotation. With the BCL SelebiPhikwe ore body, pentlandite–pyrrhotite–chalcopyrite cooccur and there is the constraint of fine pentlandite dissemination in the pyrrhotite, so that liberation is limited. In the presence of pentlandite,

Evaluation of novel RAFT block copolymers as alternatives
Stainlesssteel rods were used as the grinding media in tap water. After grinding for an established grinding time to produce a P 80 of 75 µm, the mill discharge was filtered and ovendried at 60 °C overnight and stored before using as required. Fig. 1 shows the particle size distribution of the ground quartz sample, obtained using Malvern Mastersizer.

Flotation sgs
Grinding and surface chemistry are critical to the success of oxide flotation. Overgrinding of the brittle minerals is avoided by stage grinding and careful selection of equipment. We have experience in diverse regimes for treatment of a wide range of oxide minerals such as • barite • cassiterite • copper, lead, and zinc carbonates FLOTATION
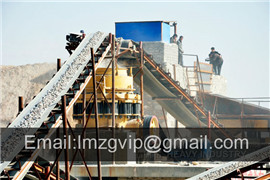
Investigation of Liberation Properties and Mineral Fracture
For finegrained iron oxide minerals, the iron oxide minerals distribution of 80–100% composition class differed by 22% at −75 + 53 μm size fraction with the two grinding methods, and its
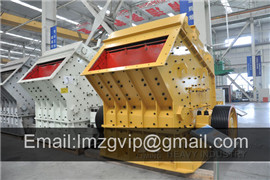
Preparation of cinnamic hydroxamic acid collector and
CIHA was synthesized by the hydroxylamine method. Methyl cinnamate and hydroxylamine were mixed with anhydrous ethanol at 50 ℃ for 6 h. The resulting reaction solution was acidified with dilute hydrochloric acid to obtain the crude product of CIHA, and the crude product was recrystallized with as little hot water as possible to get

grinding mill for froth flotation of iron ores
froth flotation of iron ore ppt. Jan 28, 2014 Froth Flotation of Iron Ores Open Access LibraryPowerPoint Presentation. With the depleting reserves of high grade iron ore in the world froth flotation has become increasingly important to process intermediate and low grade iron ore in an attempt to meet the rapidly growing demand on the international
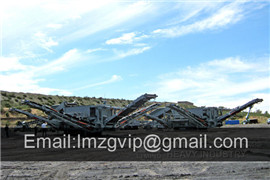
grinding mill for froth flotation of iron ores
Lorem ipsum dolor Address: No.169, Science (Kexue) Avenue, 008637186162511 Email:
- مطحنة الكرة الصينية للأسمنت
- نقل صناعة التعدين الناقل
- الصين كسارة الحجر مصنعين المورد
- آلة كسارة الحجر للايجار في المملكة العربية السعودية
- سیستم خرد کردن ابعاد سنگ
- كسارة صنع الرمل ه حمالون في ذروة الصين أ
- كسارة معمل الجزائر الصخر
- سازنده سنگ شکن مخروطی زنیت در ایران
- استخراج سطح معدن ذغال سنگ نقاله تسمه برج انتقال
- Concrete Impact Crusher Provider In Micronesia
- مطحنة للبيع تستخدم مطحنة الكرة المستعملة
- diesel maize grinding mill mill kzn
- لائحة المحجر ومصنعي خطوط المعالجة
- قطع غيار كسارة الصخور في عمان
- النباتات كسارة الفك في الصين
- ماليزيا تصنع كسارة حجر الدولوميت
- دستگاه مینی سنگ شکن طلا ارزان قیمت
- مزود كسارة الحجر الجيري المحمولة
- هزینه راه واحد سنگ شکن سنگ
- عملية مصانع تعدين النحاس