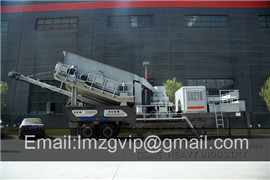
The six main steps of iron ore processing Multotec
Six steps to process iron ore. 1. Screening. We recommend that you begin by screening the iron ore to separate fine particles below the crusher’s CSS before the crushing stage. A
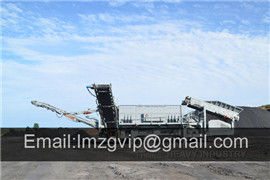

Sintering: A Step Between Mining Iron Ore and Steelmaking
Sinter quality begins with the mined iron ore and the proper selection and mixing of the raw materials. Inhomogeneous raw mix can affect permeability and cause
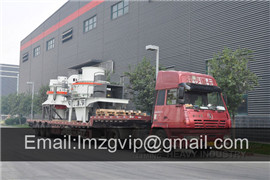
Iron ore mining and dressing tecscience
IntroductionIron Ore ExtractionIron Ore ProcessingSintering and PelletizingIron is one of the most important metals in mechanical engineering, as it is present in sufficient quantities on earth. The extraction of iron can therefore be very economical. However, pure iron is not suitable for use as a construction material. It is much too soft in its pure form and has too little strength to meet most mechanical requirements..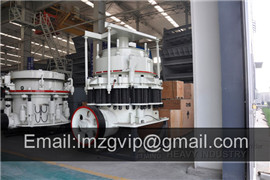
Iron Mining Process Minnesota Iron
Iron Mining Process. From blasting to crushing to separation more than 85% of the iron mined in the United States is mined in northeastern Minnesota to make our nation’s steel. Blasting Taconite is a very hard

Iron Ore Mining The process of iron ore mining %y
The process begins by removing the topsoil from the area to be mined. This soil is then replaced and compacted to make sure that there is no waterlogging or
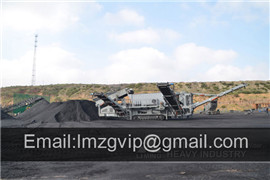
The StepbyStep Process of Producing Iron
The raw materials mix or “charge” enters the furnace from the top and hot air is blown or blasted from the bottom causing the coke to burn and the oxygen to combine with carbon in the coke to form carbon

Iron Ore Mining Techniques Metal Extraction
Iron is concentrated by the process of calcinations. Once it is concentrated, the water and other volatile impurities such as sulfur and carbonates are removed. This concentrated ore is then mixed with

id/proses step by step iron ore mining ·
Contribute to luoruoping/id development by creating an account on GitHub.
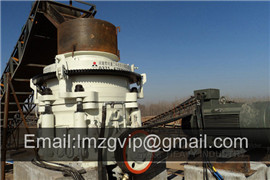
Iron Mining Process Equipment Flow Cases JXSC
Inside the ball mill, the crushed iron ore will grind the ore to about 0.2 mm with 3inch steel balls. 3. This iron ore slurry is pumped to the agitation tank. This iron ore
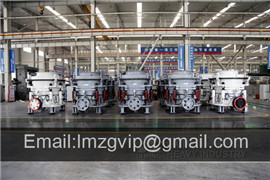
Iron ore mining and dressing tecscience
The flow chart shows the basic steps of how iron ore is used to produce semifinished products of steel. The individual process steps are explained in more detail in the following articles. Figure: From iron ore to steel (flow chart) Steel is extracted from iron ores (mainly found in sedimentary rocks) and is also known as ore smelting.

OpenPit Mine Truck Dispatching System Based on
In the production process of openpit mines, trucks are applied in the production process of openpit mines for transporting ores and rocks. Most openpit mines are equipped with dozens of trucks. It is important to plan the dispatch of trucks in the production process so that the transportation process can be the shortest in distance, the

The stages of mining: 5 lifecycle processes explained
The PreFeasibility Study (PFS) is an intermediate step in the engineering process to evaluate the technical and economic viability of a mining project. The prefeasibility study is a critical step for project development as it represents the minimum prerequisite for conversion of a geologic resource into a reportable reserve.
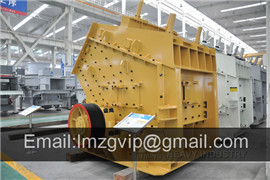
AP Environmental Science FreeResponse
2. Iron ores are rocks from which metallic iron can be extracted for steel production. This process involves several steps. Iron ore is first mined and then turned into pig iron in a blast furnace, and some rock waste such as silicon dioxide is separated out. In the final step, the pig iron is refined into steel using a process that includes
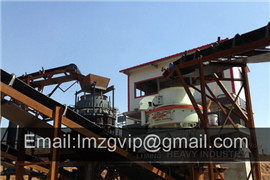
Open Pit Mining
Openpit mining, also known as opencast mining, opencut mining, and strip mining, means a process of digging out rock or minerals from the earth by their elimination from an open pit or borrow. The word is used to distinguish this type of mining from extractive methods that need tunneling into the earth. Openpit mines are used
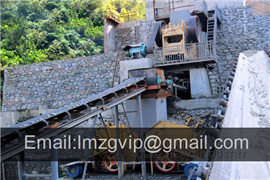
FRQ unit 4 Flashcards Quizlet
FRQ unit 4. Term. 1 / 16. iron ores are rocks from which metallic iron can be extracted for steel production. This process involves several steps. Iron ore is first mined and then turned into pig iron in a blast furnace, and some rok waste such as silicon dioxide is separated out. In the final step, the pig ion is refined into steel using a

Magnesite Ore Processing: Separation and Calcination
The processing flow is as follows: Step 1 Crushing: Use a jaw crusher, roll crusher, and vibrating screen to form a twostageclosed circuit crushing system to crush the raw magnesite ore to 1mm. Step 2 Calcination: Send the raw ore into a rotary kiln for calcination at a temperature of 700800°C for 1 hour. Step 3 Crushing: Crush the calcined

PROCESS FOR PREPARING OPTIMIZED CALCINED, IRON
A process according to any of claims 1 to 3, wherein the pellets obtained by step a) comprise 0.003% to 1wt%, preferably 0.01 to 0.5 wt% and particularly preferably 0.05 to 0.2 wt%, of saccharide binder based on the amount of chrome ore material, COPR, saccharide binder and, if present, carbonaceous reductant.

Evident Scientific Archives International Mining
The treatment process is the first step toward getting a more concentrated ore blend. It is crucial to achieve this step correctly and, more importantly, to identify any mistakes to act on time. Regular laboratory analyses cannot be conducted as the results on incoming head grades will come too late to correct errors.
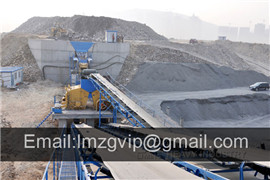
What are the steps for extracting minerals from the ore?
The mining process involves the excavation of large amounts of waste rock to remove the desired mineral ore. chemical processing and separation to extract the target minerals. What are the six steps of ore extraction? The Six Main Steps of Iron Ore Processing. Screening. We recommend that you begin by screening the iron ore to separate fine

3 key steps for forging a path to green steel BCG BCG
Decarbonizing steel production, which generates about 7% of global CO 2 emissions, is a vital step toward achieving a netzero world. For mining companies that supply the iron ore needed to produce steel, helping steelmakers reach this goal could remedy their own emissions problems.. Many iron ore mining companies are already

Integrated Production and Distribution Planning for the
This paper studies the production and distribution planning problem faced by the iron ore mining companies, which aims to minimize the total costs for the whole production and distribution system of the iron ore concentrate. The ores are first mined from multiple ore locations, and then sent to the corresponding dressing plant to produce ore
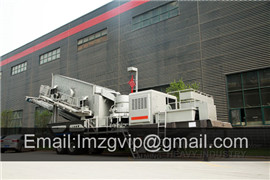
Iron ore mining and dressing tecscience
The flow chart shows the basic steps of how iron ore is used to produce semifinished products of steel. The individual process steps are explained in more detail in the following articles. Figure: From iron ore to steel (flow chart) Steel is extracted from iron ores (mainly found in sedimentary rocks) and is also known as ore smelting.
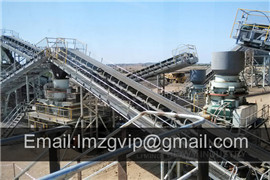
The stages of mining: 5 lifecycle processes explained
The PreFeasibility Study (PFS) is an intermediate step in the engineering process to evaluate the technical and economic viability of a mining project. The prefeasibility study is a critical step for project development as it represents the minimum prerequisite for conversion of a geologic resource into a reportable reserve.

Extraction of Iron: Meaning, Purification, & Extraction
Here, Fe2O3 is reduced to iron by CO in the following three steps. 3Fe 2 O 3 + CO → 2Fe 3 O 4 + CO 2. Fe 3 O 4 + CO → 3FeO + CO 2. FeO + CO → Fe + CO 2 The most important iron ore is hematite. The iron extraction process is a long process that begins with calcination and is then followed by a few major steps.
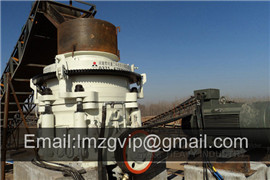
6 Stages of the Mining Process BOSS Magazine
From there, the ore is transported to a separate facility for smelting, which is: The process of melting the ore concentrate in a furnace to separate the metal. Then, the ore is poured into molds to make bars of
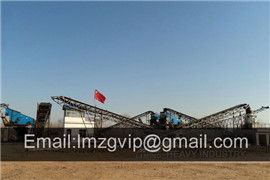
FRQ unit 4 Flashcards Quizlet
FRQ unit 4. Term. 1 / 16. iron ores are rocks from which metallic iron can be extracted for steel production. This process involves several steps. Iron ore is first mined and then turned into pig iron in a blast furnace, and some rok waste such as silicon dioxide is separated out. In the final step, the pig ion is refined into steel using a
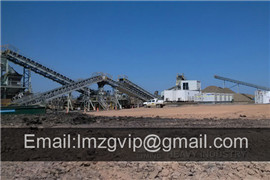
Open Pit Mining
Openpit mining, also known as opencast mining, opencut mining, and strip mining, means a process of digging out rock or minerals from the earth by their elimination from an open pit or borrow. The word is used to distinguish this type of mining from extractive methods that need tunneling into the earth. Openpit mines are used
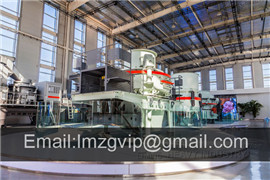
PROCESS FOR PREPARING OPTIMIZED CALCINED, IRON
A process according to any of claims 1 to 3, wherein the pellets obtained by step a) comprise 0.003% to 1wt%, preferably 0.01 to 0.5 wt% and particularly preferably 0.05 to 0.2 wt%, of saccharide binder based on the amount of chrome ore material, COPR, saccharide binder and, if present, carbonaceous reductant.
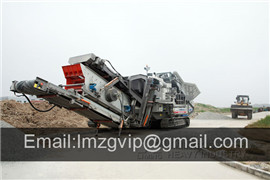
Magnesite Ore Processing: Separation and Calcination
The processing flow is as follows: Step 1 Crushing: Use a jaw crusher, roll crusher, and vibrating screen to form a twostageclosed circuit crushing system to crush the raw magnesite ore to 1mm. Step 2 Calcination: Send the raw ore into a rotary kiln for calcination at a temperature of 700800°C for 1 hour. Step 3 Crushing: Crush the calcined
- كسارة الحجر الرملي الأولية المتنقلة
- مطحنة الحجر المحمولة للمختبر
- terms and machinery needed for iron ore raising
- إجمالي تشغيل مصنع البناء pdf
- مطحنة الدرفلة في الجزائر
- السويد المصنعة محطم مخروط
- used husky vertical milling machine
- القائمة البريدية للهندسة الصناعية
- باعة معدات كسارة الحجر في مصر
- مطحنة الذهب الخام في ولاية كارناتاكا
- كسارة الصخور المحمولة للتنقيب عن الذهب للبيع
- فرایند شستشو با هیدروسیکلون
- كسارة الحجر للبيع بوليفيا السعر
- لوحة بطانة لمصنع الاسمنت
- تستخدم مطحنة الكرة بيع الهند في الهند
- مواصفات مطحنة الطاحونة العالمية
- كسارات الفك مصنعين الجزائر
- استخراج سطح معدن ذغال سنگ نقاله تسمه برج انتقال
- رمل السيليكا وحدة غسيل فنلندا
- تستخدم كسارة الفك أولية للبيع في مصر