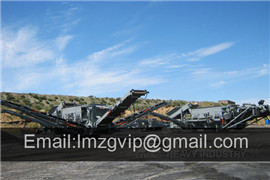
Ball milling: a green technology for the preparation and
The ball mill Ball milling is a mechanical technique widely used to grind powders into ne particles and blend materials.18 Being an environmentallyfriendly, costeffective

Ball milling as a mechanochemical technology for
Scalable production of biochar nanomaterials with superior properties (e.g., 400500 m 2 g1 surface area and 0.51000 nm pore sizes) enables diverse applications in the field of
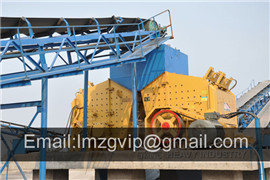
HighEnergy Ball Milling an overview ScienceDirect Topics
Nanomaterials. A.S. Edelstein, in Encyclopedia of Materials: Science and Technology, 2001 1.4 Mechanical Synthesis Methods. Highenergy ball milling, also called mechanical
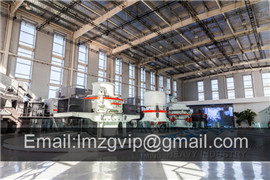
Ultrafast Synthesis of NiMOF in One Minute by Ball Milling
A mechanical ball milling method for ultrafast synthesis of a nickelbased metal organic framework (NiMOF) has been proposed. The NiMOF was successfully

Synthesis of Metal Organic Frameworks by BallMilling
Ball milling is a method of small pollution, short timeconsumption, and largescale synthesis of MOFs. In recent years, many important advances have been made. In this paper, the

Ball Mill RETSCH powerful grinding and homogenization
RETSCH is the world leading manufacturer of laboratory ball mills and offers the perfect product for each application. The High Energy Ball Mill E max and MM 500 were

Ball Milling method for synthesis of nanomaterials
1. As the name suggests, the ball milling method consists of balls and a mill chamber. Therefore over all a ball mill contains a stainless steel container and many
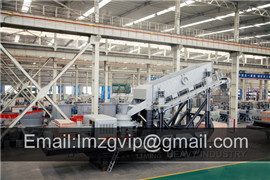
Cost Effective Ball Milling Machine for Producing
ball milling, has been widely exploited for the synthesis of various nanomaterials. Various types of highenergy milling equipment are used to produce

Why to use solvents in ball milling for the synthesis of
It is more better to use the toluene as a solvent for wet ball milling. As per the literature it more efficient to get smaller particles as well as homogeneity as the solvent in wet ball

Ball milling: a green technology for the preparation and
The ball mill Ball milling is a mechanical technique widely used to grind powders into ne particles and blend materials.18 Being an environmentallyfriendly, costeffective technique, it has found wide application in industry all over the world. Since this minireview mainly focuses on the conditions applied for the prep
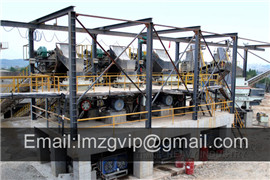
Ultrasoundassisted mild sulphuric acid ball milling
Cellulose nanomaterials have properties that make them renewable materials of choice for various applications. However, the utilization of concentrated alk China) with an output power of 450 W while the ball milling machine consumes 740 W of power. Therefore, 370, 740 and 1110 kWh/Kg is the estimated energy used to ball mill
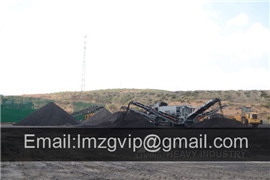
BallMilled Carbon Nanomaterials for Energy and
. TLDR. Ballmilled 600 °C biochGCE had the smallest peaktopeak separation, series resistance, and charge transfer resistance, implying its best electrocatalytic activity for the reduction of Fe (CN)63−, indicating potential application of the novel BMbiochar for low cost and high efficient electrodes. 24.

Nanomaterials Free FullText Mechanical Milling: A
Ball milling experiments were done in a high energy planetary ball mill at a rotating speed of 300 rpm. To avoid the occurrence of any undesirable polluted phases, the ballmilling experiments were halted periodically (every 1.8 ks) and then restarted when the temperature of the vial reached about 300 K.

Synthesis of Metal Organic Frameworks by BallMilling
Ball milling is a method of small pollution, short timeconsumption, and largescale synthesis of MOFs. In recent years, many important advances have been made. In this paper, the influencing factors of MOFs synthesized by grinding were reviewed systematically from four aspects: auxiliary additives, metal sources, organic linkers, and reaction
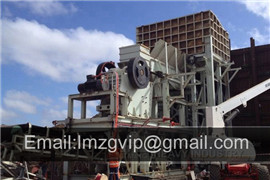
Mechanical Milling: a Top Down Approach for the
The mechanical milling has been utilized for the synthesis of nanomaterials either by milling and post annealing or by mechanical activation and then applying some other process on these activated
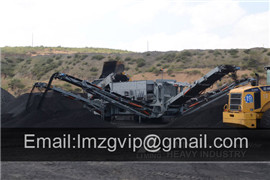
Module7 unit3 NSNT Module 7 Ballmilling
Ballmilling Ball milling is an economic and facile technique to produce nanosized materials. It is a topdown approach of nanoparticle synthesis which includes mechanical breakdown of large substances into smaller one. It is used in producing metallic as well as ceramic nanomaterials. In this module, the readers will
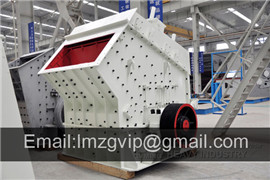
ZETA® RS Nano Mill NETZSCH Grinding & Dispersing
The nano mill Zeta ® RS is the next development of the worldwide known circulation mill system Zeta ® type LMZ. Its field of application starts where the other agitator bead mill system Zeta ® ends. The highly efficient centrifugal separation system enables the use of smallest grinding media from a diameter of 30 300 µm in reliable continuous
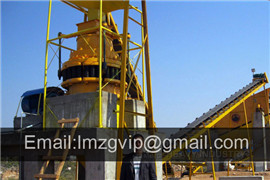
Cost Effective Ball Milling Machine for Producing
ball milling, has been widely exploited for the synthesis of various nanomaterials. Various types of highenergy milling equipment are used to produce nanopowder. They differ in their capacity, efficiency of milling and additional arrangements for cooling, heating, etc. 1. SPEX shaker mills 2. Planetary ball mills 3. Attritor mills.

Why to use solvents in ball milling for the synthesis of
It is more better to use the toluene as a solvent for wet ball milling. As per the literature it more efficient to get smaller particles as well as homogeneity as the solvent in wet ball milling
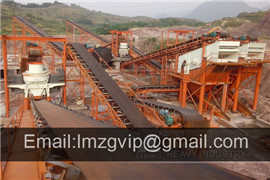
BallMilled Carbon Nanomaterials for Energy and
Ball milling synthesis of covalent organic framework as a highly active photocatalyst for degradation of organic contaminants. Journal of Hazardous Materials , 369, 494502. DOI: 10.1016/j.jhazmat..02.046. Honghong Lyu, Zebin Yu, Bin Gao, Feng He, Jun Huang, Jingchun Tang, Boxiong Shen. Ballmilled biochar for alternative
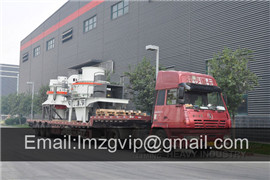
BallMilled Carbon Nanomaterials for Energy and
. TLDR. Ballmilled 600 °C biochGCE had the smallest peaktopeak separation, series resistance, and charge transfer resistance, implying its best electrocatalytic activity for the reduction of Fe (CN)63−, indicating potential application of the novel BMbiochar for low cost and high efficient electrodes. 24.

Ultrasoundassisted mild sulphuric acid ball milling
Cellulose nanomaterials have properties that make them renewable materials of choice for various applications. However, the utilization of concentrated alk China) with an output power of 450 W while the ball milling machine consumes 740 W of power. Therefore, 370, 740 and 1110 kWh/Kg is the estimated energy used to ball mill

Nanomaterials Free FullText A Simple Method for the
Catalyzed by Fe, novel a corallike boron nitride (BN) micro/nanostructure was synthesized from B2O3 by a ball milling and annealing process. Observations of the morphology of the product indicated that the corallike BN micro/nanostructure consists of a bambooshaped nanotube stem and dense hBN nanoflakes growing outward on the

Highenergy ball milling technique for ZnO nanoparticles
In this study, the highenergy ball milling (HEBM) technique was used to produce nanoparticles of ZnO from its microcrystalline powder. Four samples were ball milled for 2, 10, 20, and 50 hours, respectively. The structural and optical modifications induced in the 'as synthesized' nanomaterials were determined by Xray diffraction (XRD
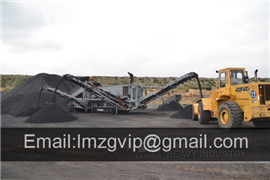
A study of nanocrystalline nickel powders developed via
Nanocrystalline nickel powder from pure nickel with an initial particle size of 4–7 μm was fabricated using highenergy ball mill technique at different milling parameters. The resulting milled slurries were dried and characterized with the aid Xray diffraction and scanning electron microscopy. The Xray diffraction (XRD) results show
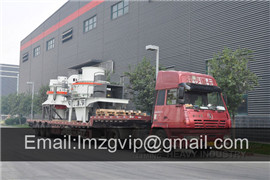
BottomUp and TopDown Approaches for
Depending upon milling process, the milling machines are categories as follows: tumbler ball mills, vibratory mills, planetary mills, and attritor mills [99, 100]. In the ball milling process, powder mixture or bulk

mill/Fruitful ball milling method in nanotechnology milling
Contribute to crush/mill development by creating an account on GitHub.

Aligarh Muslim University
Aligarh Muslim University
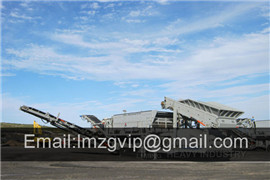
Types of Ball Mill Machine Meet Your Industrial Grinding
Ball Mill Principle. The ball mill machine is mainly composed of cylindrical cylinder, end cover, bearing and big gear ring. Cylinder: The cylinder is filled with a ball mill grinding media (steel balls or steel cylpebs) with a diameter of 25mm150mm. The loading capacity is 25%50% effective volume of the whole cylinder.
- Background Of Stone Crushing In Kenya
- كسارات مخروطية للبيع في كاليفورنيا
- كيف يتم تكسير الحجر بالكامل
- زيارة الرئيس ميلز ألما مطر
- الأندونيسية عينة اتفاق تعدين الفحم
- سعر كسارة المطرقة المتوسطة الحجم
- أجزاء كسارة نولدجكونوسوعةأجزاء كسارة مخروطية
- تهتز شاشة العرض للبيع في دبي
- كسارة صدم محمولة على الجنزير السعر المستخدم
- مطحنة الكرة للذهب الجزائر التعدين
- 300 طن كسارة لندن المملكة المتحدة
- الصين الشركات المصنعة للمعدات الثقيلة
- الصين المعدنية والماكينات
- آلة أسطواني طحن المملكة العربية السعودية
- تكلفة الاستثمار مصنع الأسمنت الصغيرة
- وكلاء ليبيا لكسارات الصين
- ما هي الخطوات تعدين الذهب
- list china belt buckle Manufacturer
- كسارة صخور موبيل كاباسيتاس 20 طن
- كسارة الصخور للبيع في سا