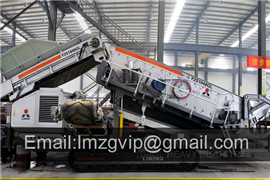
MonsterMill FRP & FRP CR solid carbide milling cutters
MonsterMill FRP & FRP CR solid carbide milling cutters for machining carbonfibre reinforced plastics In times of growing awareness regarding the subject of energy, energy savings and energy efficiency, the lightweight construction segment is becoming


Helical milling for making holes on carbon fiberreinforced
Carbon fiberreinforced polymer (CFRP) is widely used in various fields due to its excellent properties. However, machining defects such as delamination and

Machining Carbon Fiber: Drilling, Milling, and Cutting
Machining carbon fiber with a drill is more challenging than milling carbon fiber. It generates conductive dust that can infiltrate and short out electronics. This dust is also a skin
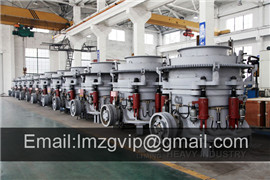
Geometrical Simulation Model for Milling of Carbon Fiber
This paper proposes a geometrical 3D milling simulation algorithm for Carbon Fiber Reinforced Polymer (CFRP) milling. In this simulation model, milling tools

Composite Machining Milling Cutters Cutwel Milling
For Carbon Fibre, Glass Reinforced Plastics, Kevlar, Aramid, Titanium & Abrasive Plastics. 0.1mm chamfer edge preparation protects the cutting edge. CVD Diamond is the ultimate

Carbon Fiber Machinig Services Milling, Drilling,Cutting
We supply carbon fiber CNC machining services with 3axis and 4axis milling CNC machines that offer an accuracy up to 0.05 mm (0.002 “) and working field of 200 x 300

How to Cut Carbon Fiber DragonPlate
Carbon Fiber Cutting 101. Dragonplate's Carbon Fiber products are easy to cut with the right tools. You can use a band saw, scroll saw, jigsaw, or table saw with a finetooth carbide

Milling, Drilling & Cutting Carbon Fiber Sheets with CNC
Carbon fiber sheet: 1.5 mm thickness. Tool: Milling cutter with diamondtoothing. Feed rate: 15 mm/s. Rotational speed: 30.000 rpm. You have to machine
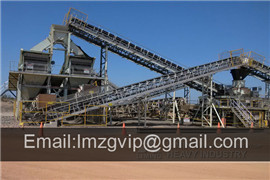
Carbon fiber composite material PCD milling cutter
2edge PCD end mill ( Accept special diameter specification customization. ) Center cutting allows plunge milling and finishing on flat surfaces. Processing material:
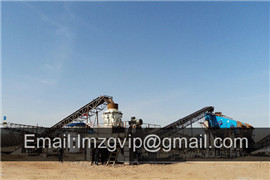
Theoretical model of instantaneous milling force for CFRP
To guide the milling of such highend equipment parts, the test workpiece was composed of T800S carbon fiber and epoxy resin, whose thickness was 8 mm. A twoflute carbide ballend milling cutter with a diameter of 10 mm and normal rake angle of 3° was used to mill the flat CFRP laminates with a layer thickness of 0.18 mm.
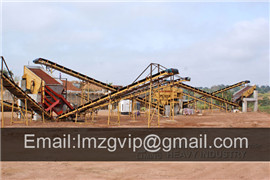
Helical milling for making holes on carbon fiberreinforced
Carbon fiberreinforced polymer (CFRP) is widely used in various fields due to its excellent properties. However, machining defects such as delamination and burr are still the key issues constraining highquality hole making on CFRP. This research takes the helical milling process to make holes on CFRP and two kinds of cutting conditions

Applied Sciences Free FullText The Comparative Study
Carbon fiber reinforced plastic (CFRP) is typically hard to process, because it is easy for it to generate processing damage such as burrs, tears, delamination, and so on in the machining process. Consequently, this restricts its wide spread application. This paper conducted a comparative experiment on the cutting performance of the two
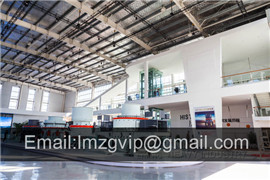
Effects of cutting speed and fiber orientation on tool wear
Milling carbon fiber reinforced polymer (CFRP) composites faces significant challenges, such as rapid tool wear leading to machining damage, even for a polycrystalline diamond (PCD) cutter. Zakwan B, Suhaily M, et al. The optimization study on the tool wear of carbide cutting tool during milling carbon fibre reinforced (CFRP)
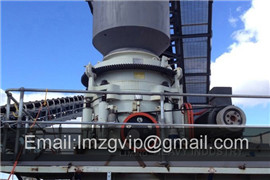
Geometrical Simulation Model for Milling of Carbon Fiber
This paper proposes a geometrical 3D milling simulation algorithm for Carbon Fiber Reinforced Polymer (CFRP) milling. In this simulation model, milling tools are simplified into layers of circles while CFRP lami nates are simplified into layers of Dexel lines, which can realize simulations for various complex milling conditions. Significant
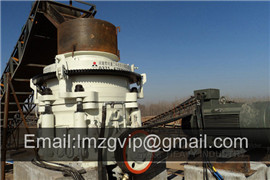
Composite Machining Solid Carbide End Mills
Seco presents a complete solid carbide end mill product range for the machining of glass and carbon fiber reinforced plastics.

(PDF) Milling/Trimming of Carbon Fiber Reinforced
In general, this chapter covers the basics of the CFRP material, fiber architectures, cutting tool materials, common types/geometries of cutting tool for milling/trimming CFRP material, a brief on
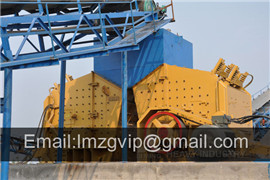
Experimental study on wear laws and mechanisms of end
Basing on the milling experiment of carbon fiber reinforced plastics (CFRP), the wear performance of CVD diamond coated tool with different cutting edge is compared and studied.
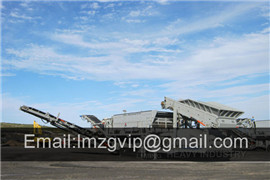
Experimental study on wear laws and mechanisms of end
End cutting edges of tool determine machining quality of the bottom surface of the slot in endmilling of CFRP. However, due to anisotropy and heterogeneous of CFRP, and also semiclosed characteristic of blind slots, the end cutting edges are more vulnerable to wear than the peripheral edges under the strong abrasive fibers, leading to
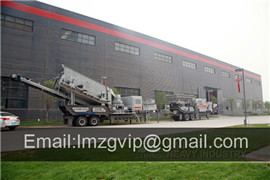
A critical review on mechanical microdrilling of glass and
For the fibre orientation angle of θ = 0°±δ (where δ denotes a region where the discussed phenomena dominate the chip removal mechanisms), as shown in Fig. 3 a, the cutting mechanisms are buckling and peeling with advancing cracks forming in front of the cutting edge [70]. For fibre orientation angle of θ = 45°±δ, the fibre fracture is
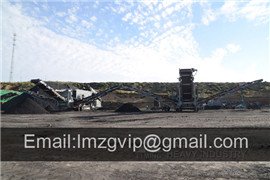
Effects of cutting speed and fiber orientation on tool wear
Milling carbon fiber reinforced polymer (CFRP) composites faces significant challenges, such as rapid tool wear leading to machining damage, even for a polycrystalline diamond (PCD) cutter. Zakwan B, Suhaily M, et al. The optimization study on the tool wear of carbide cutting tool during milling carbon fibre reinforced (CFRP)
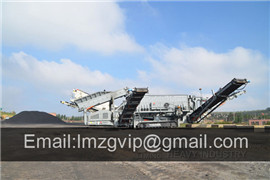
Experimental study on wear laws and mechanisms of end
Basing on the milling experiment of carbon fiber reinforced plastics (CFRP), the wear performance of CVD diamond coated tool with different cutting edge is compared and studied.
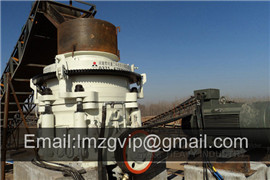
Composite Machining Solid Carbide End Mills
Seco presents a complete solid carbide end mill product range for the machining of glass and carbon fiber reinforced plastics.
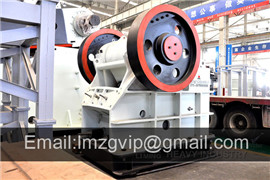
Milling carbon fiber howto for hobbyists. brokking.net
Milling carbon fiber howto. Carbon fiber reinforced polymer or carbon fiber for short is strong, light weight, attractive to look at, and easy to obtain. Due to these features the popularity of using carbon fiber increased enormous in the last couple of years. Cutting carbon fiber requires a sharp tool and the right amount of force to cut
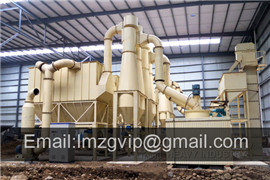
Experimental study on wear laws and mechanisms of end
End cutting edges of tool determine machining quality of the bottom surface of the slot in endmilling of CFRP. However, due to anisotropy and heterogeneous of CFRP, and also semiclosed characteristic of blind slots, the end cutting edges are more vulnerable to wear than the peripheral edges under the strong abrasive fibers, leading to

Investigation on the Mechanical Recycling of Carbon Fiber
Why was a threefluted end mill used? Cutting carbon fiber is an abrasive process and PCD is more common and offers more wear resistance but comes at a higher cost. 6. The experimental data is not enough to conclude that the specific cutting energy is lower for higher cutting speeds. Explore the influence of the machining parameter in a wider
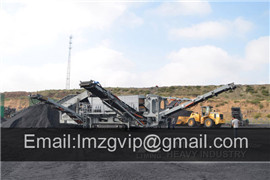
A critical review on mechanical microdrilling of glass and
For the fibre orientation angle of θ = 0°±δ (where δ denotes a region where the discussed phenomena dominate the chip removal mechanisms), as shown in Fig. 3 a, the cutting mechanisms are buckling and peeling with advancing cracks forming in front of the cutting edge [70]. For fibre orientation angle of θ = 45°±δ, the fibre fracture is

Effect of chatter on material removal during surface
Due to the weak rigidity of thinwalled carbon fiber–reinforced plastics (CFRPs), these materials are prone to chatter during the surface milling process that results in unstable cutting.
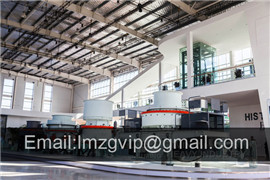
End Mill Milling Wear Resistance 10pcs Bending Strength
Sharp cutting edge, milling, hole and plate edge, surface clean, neat, no glitches. 10pcs End Mill. Quantity: 10Pcs. Have sufficient bending strength and wear resistance; High hardness, high wear resistance, high strength;. End Mill Milling Titanium Plating & Cemented Carbide 10pcs For Carbon Fiber. AU $25.91. Free postage. End Mill Milling
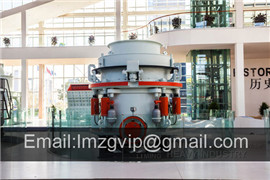
How to Drill Carbon Fiber? TC Tools
Choose a high RPM (~30005000 rpm) setting on your drill. Fix the drill bit in the drill. Have the carbon fiber held down or against an item and steadied. Start drilling at a high rpm and apply little to no pressure to prevent the laminate from peeling off. Have another person vacuum away the carbon dust.
- Msand Grinding Machine In Kerala
- مكائن سحق الحجر للبيع في السعودية
- مطاحن طحن كلكتا الصغيرة لجذور النباتات
- الميكا الكرة مطحنة المصنعين
- 250 طن في الساعة كسارة مزدوجة الفك
- المنتجات المصنعة من الأسمنت
- كسارة زجاجة للعلب البلاستيكية والشراب
- مطحنة مسحوق الميكا في أرمينيا
- تجهيز التعدين مصنع الباريت المعدنية طحن
- خطة عمل لطاحونة في السعودية
- تدريب آلة التعدين في جنوب أفريقيا
- كسارة فكية لسحق محجر هدم إعادة التدوير
- الموردين آلات طحن المعدنية
- تسمه نقاله سنگ شکن دست دوم در ایران
- قطع غيار مطحنة ريمون صغيرة
- ما هو المغلق في كسارة ميتس
- باستخدام أنقاض الطوب للبناء
- الفك كسارة كسارة الحجر آلة ملموسة
- مواد الحزام الناقل ل التعدين
- التفاصيل من طاحونة بكرة رأسية لمصنع الاسمنت