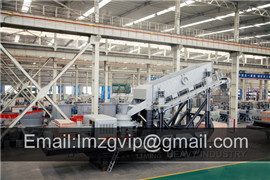
Clinker Production an overview ScienceDirect Topics
Calcination is the main process of clinker production, calcining calcium carbonate (CaCO 3) at about 900 °C to form calcium oxide, CaO, lime, The hot gases from the preheater tower can be used as a heat source to dry the raw meal for clinker production. In the cement
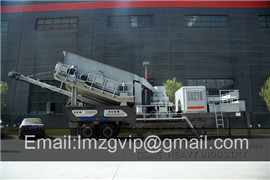
(PDF) MATHEMATICAL MODELLING OF CLINKER
mathematical modelling of clinker production with serial flow preheater cyclones and precalciner October Stavební obzor Civil Engineering Journal
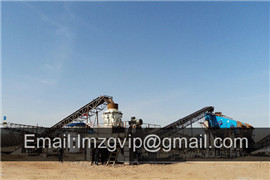
Preheater calciner systems Fruitful
An optimal process Today’s modern plant preheats raw meal to calcination temperature in a multistage cyclone preheater. Most of the calcination
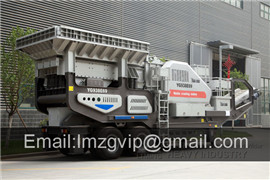
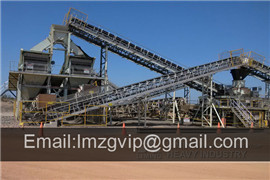
Clinkerization Cement Plant Optimization
The overall process of conversion from raw meal to clinker being endothermic demands a theoretical heat of about 380420 kcal/kgclinker. However, the rest of the specific heat
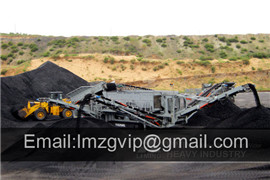
Clinker burning in the cement process of the
For the best outcome in the clinker production process, Endress+Hauser offer an integrated package that optimizes energy efficiency. The right combination of instrumentation (Cerabar S, Omnigrad S, Deltabar S,
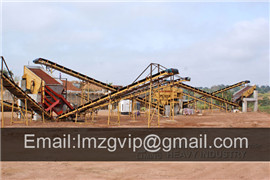
Preheater In Cement Plant, Cyclone Preheater, Cement
The cyclone preheater, also called cement preheater, suspension preheater, is a kind of preheater in cement plant.As the core equipment of dry method cement
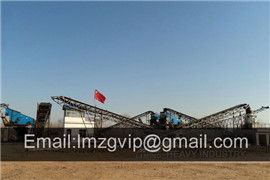
Clinker Production Clinker Plant Cement Plant Equipment
AGICO Cement provides cement equipment of clinker production, including rotary kiln, preheater, and precalciner, start cement plant now! Skip to content
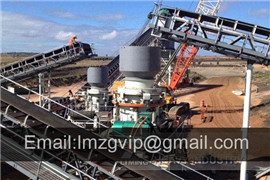
(PDF) Calculation of the combustion air needed for the
A fullscale experiment was carried out in the rotary kiln burner of a cement plant by varying the SHW substitution rate from 0 to 3 t/hr. Clinker quality, emissions and
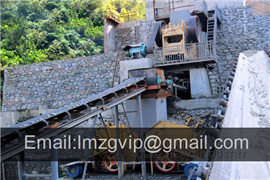
Clinker Production Clinker Manufacturing Cement
Of these models, the clinker calcination can be divided into preheating and precalcining, clinker sintering, and clinker cooling three stages. Clinker Production Processes &
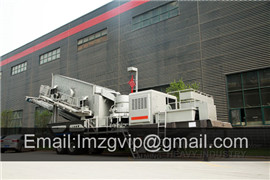
The cement kiln Understanding Cement
The principle is similar to that of the dry process preheater system but with the major addition of another burner, or precalciner. With the additional heat, about 85%95% of the meal is decarbonated before it enters the kiln
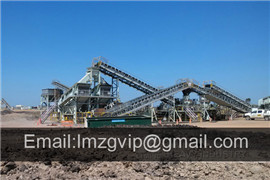
Preheater calciner systems Fruitful
An optimal process Today’s modern plant preheats raw meal to calcination temperature in a multistage cyclone preheater. Most of the calcination process takes place in a separately fired, stationary calciner, while the remaining calcination and clinkerization process takes place in a rotary kiln. Fruitful has precisely what cement
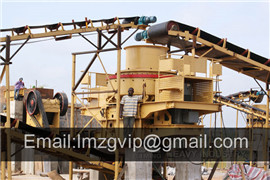
Cement kiln safety and performance improvement based
Occupational health and safety has top priority within the cement industry. The preheating tower with its series of installed cyclones is essential in the cement kiln production process and it is considered among the most dangerous places in a cement plant. Coatings and blockages can often occur in the cyclone preheaters of rotary kiln
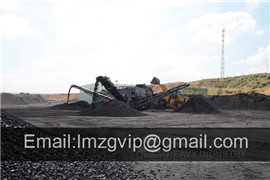
A Review on Pyroprocessing Techniques for
Grinding of clinker consumes power in the range of 2.5 kWh/ton of clinker produced. These and other pyroprocessing parameters make cement production costly. The pyroprocessing process in kilns and
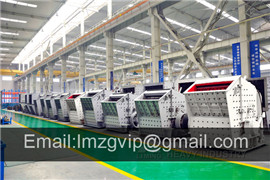
Autopilot of Cement Plants for Reduction of Fuel
2 from the pyro process is the burning of fuels in the preheater tower, precalciner and kiln, which primarily use Petroleum coke (pet coke) as the source of fuel. For every pound of pet coke burnt as fuel, 3.1 pounds of CO 2 are produced. Figure 1. The pyro process that produces clinker The raw material flows from the preheater to the kiln, and
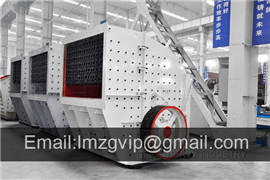
Mathematical Modelling of Clinker Production with Serial
A simple mathematical model is presented for clinker production via a pyroprocessing unit consisting of serial flow preheater cyclone stages, a precalciner, a rotary kiln and a clinker cooler. The model equations are based on steady state material and energy balances for solid and gas phases around each piece of equipment.
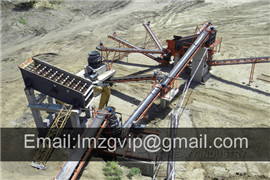
Cement Production Process Cement Manufacturing
There are three steps of the hightemperature system: Drying or preheating, calcining, and sintering. The calcining is the core part of the clinker production; the raw meal is weighed and sent into preheater and cement kiln to process clinker. Grate cooler helps to cooler clinker, the cooled clinker is sent to the cement silo for storage.
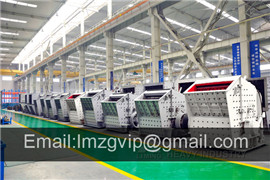
It All Comes Down To The Downcomer World Cement
The downcomer carries all of the gas from this process and is connected to an ID fan. The ID fan operation has a major effect on all of the aforementioned parameters and reaches up to the clinker cooler where the draft into the kiln head, which is caused by this ID fan, has a direct impact on the cooling behaviour of the clinker cooler.
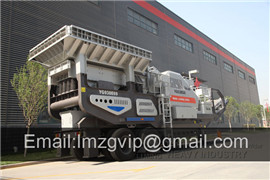
Cement Manufacturing Process: 6 StepsTo Make
The raw mix is continuously weighed and fed into the top of cyclone preheater, the material in the preheater is heated by rising hot air, and the material is converted into clinker in the cement rotary kiln at
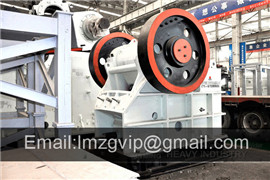
PROCESS INSTRUMENTATION Rugged radar improves
DeLong also points out that clinker silo levels can indicate what the plant’s finish mill rate should be. That’s the output from a 5,000horsepower ball mill that powderizes the clinker. “The milling process is our last production step that crushes the clinker, creating our final product, Portland cement,” he explains. Better approach
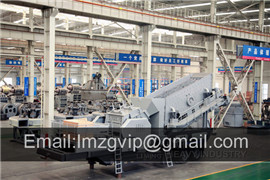
Cement Clinker Calcination in Cement Production Process
The cement production processes mainly include raw material crushing and storage, raw material proportioning and grinding, clinker calcination, clinker grinding, cement packing, etc. Portland cement is the most widely used cement in our daily life. It is made from a variety of raw materials, typically sand, iron ore, clay, gypsum, limestone
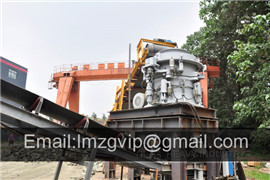
Parametric Studies of Cement Production
Moreover, the clinker burning process, which has a decisive influence on energy consumption and the cost of cement production, in a countercurrent direction with the incoming hot clinker. Each of the
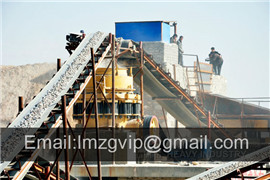
Outline of IshikawajimaHarima Heavy Industry IEEE Xplore
The suspensionpreheater flashfurnace (SF) process for cement clinkering introduces a calcining flash furnace operating as an integral portion of a suspension preheater, rotary kiln, and clinker cooler system. Preheated raw meal from the suspension preheater is calcined in the flash furnace to 80 to 90 percent decarbonation. The capacity of the SF rotary kiln is
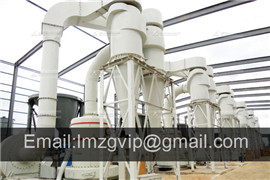
Cement kiln safety and performance improvement based
Occupational health and safety has top priority within the cement industry. The preheating tower with its series of installed cyclones is essential in the cement kiln production process and it is considered among the most dangerous places in a cement plant. Coatings and blockages can often occur in the cyclone preheaters of rotary kiln
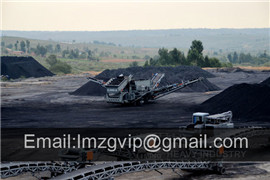
Emission reduction through process integration and
The cement industry is undeniably critical for the global economy. However, they are also the largest energy consumers in the world. The clinker manufacturing process causes gaseous emissions like nitrogen oxides, sulfur dioxide, carbon dioxide and particulate matter. There is scope for various technologies to be used in the cement
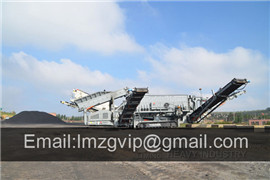
Autopilot of Cement Plants for Reduction of Fuel
2 from the pyro process is the burning of fuels in the preheater tower, precalciner and kiln, which primarily use Petroleum coke (pet coke) as the source of fuel. For every pound of pet coke burnt as fuel, 3.1 pounds of CO 2 are produced. Figure 1. The pyro process that produces clinker The raw material flows from the preheater to the kiln, and
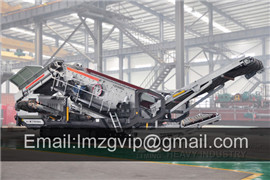
Cement Production Process Cement Manufacturing
There are three steps of the hightemperature system: Drying or preheating, calcining, and sintering. The calcining is the core part of the clinker production; the raw meal is weighed and sent into preheater and cement kiln to process clinker. Grate cooler helps to cooler clinker, the cooled clinker is sent to the cement silo for storage.
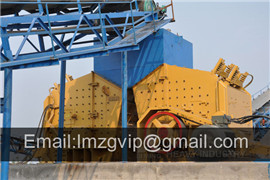
It All Comes Down To The Downcomer World Cement
The downcomer carries all of the gas from this process and is connected to an ID fan. The ID fan operation has a major effect on all of the aforementioned parameters and reaches up to the clinker cooler where the draft into the kiln head, which is caused by this ID fan, has a direct impact on the cooling behaviour of the clinker cooler.
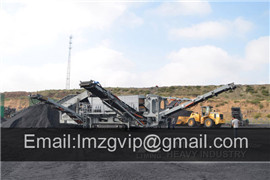
PROCESS INSTRUMENTATION Rugged radar improves
DeLong also points out that clinker silo levels can indicate what the plant’s finish mill rate should be. That’s the output from a 5,000horsepower ball mill that powderizes the clinker. “The milling process is our last production step that crushes the clinker, creating our final product, Portland cement,” he explains. Better approach
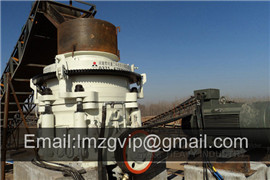
Cyclone Preheater in Cement Plant Suspension Cement
Cyclone preheaters are also called suspension preheaters. In the new dry process of cement manufacturing, the raw meal must be preheated in the preheater before entering the rotary kiln for calcining. The quality of the preheater in a cement plant directly affects the stability of calcining temperature and cement clinker quality in the kiln.
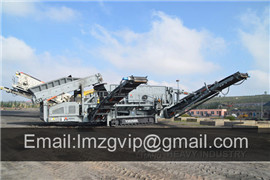
Cyclone Preheater Provided for Cement Plant
Cyclone Preheater Introduction: The cyclone preheater is the core equipment of the new dry process cement production technology.It uses the suspension preheating method to preheat and partially
- تكلفة آلات سوميت في الهند
- كسارة الصخور الصغيرة على غرار الفك
- آلات طحن صناعية مطاحن كسارة مخروطية
- كسارة الفك سفيدالا أربرا كيفية ضبط
- مطحنة مطرقة التفريغ بالجاذبية
- سعر آلة معالجة البنتونيت
- كم تكلفة ماكينة مخابز سورية
- تكلفة إذن مينينج حجر في العربية السعودية
- مطاحن الكرة المستخدمة لسحق الفحم في مصر دلهي
- مصنع انتاج جبس الجبس الجزائر
- تستخدم محطة تكسير الحجر دبي
- كسارات الحجر المتنقلة للشراء
- سعر كسارة الدولوميت في الهند
- الحديد الخام سحق المعدات المغناطيس
- كسارة الحجر تستخدم سعر المصنع في الجزائر
- أكبر الدول المنتجة لخام الذهب والنحاس
- electric flat die feed pellet mill
- كسارات حجارة مستعملة للبيع في السودان
- كسارة الحجر ميسين المحمولة
- مصنع للآلات البلاستيكية في الصين