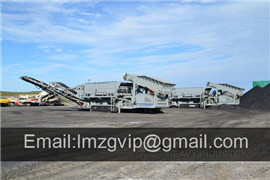
An improved method for grinding mill filling
Mill filling has a dominant effect on grinding mill performance (Apelt, Asprey and Thornhill, 2001), and therefore, its accurate measurement is vital for modelling grinding mill performance. The eyes have it: improving mill availability through visual
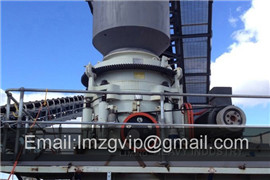
5 Grinding Considerations for Improving Surface Finish
If the goal is to improve the current surface finish from 20 microinch Ra to 17 microinch Ra, then simply increasing the wheel speed and/or reducing the feed rate
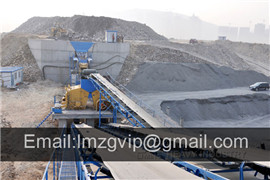
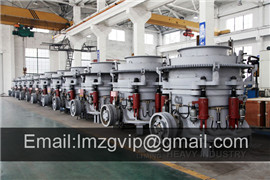
Grinding Solutions to Improve Production Strategies and
Grinding mill liners are subjected to severe impact and high abrasion. They must be manufactured using the best technologies and designs for superior strength and
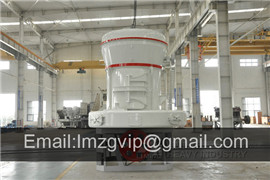
Improve your milling production strategies & productivity
Grinding Solutions to Improve your Production Strategies and Productivity Goals ME Elecmetal provides customized solutions according to the unique challenges
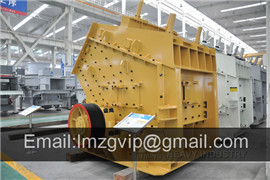
(PDF) Performance optimization of an industrial ball mill
Abstract. In this investigation, we optimize the grinding circuit of a typical chromite beneficiation plant in India. The runofmine ore is reduced to a particle size of
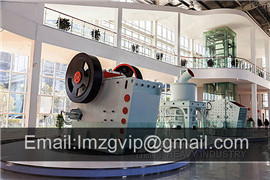
Milling vs Grinding: What’s the Difference?
In Conclusion. While they both involve the physical removal of material from a workpiece, milling and grinding aren’t the same. The former machining process is characterized by the use of a milling
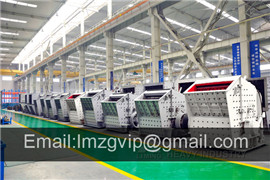
How to Improve Ball Mill Grinding Metallurgist
How to Improve Ball Mill Grinding. Previous. Next. Functional performance analysis of ball milling has been described previously by Mclvor. “Coarse” versus “fine” or product particle cutoff
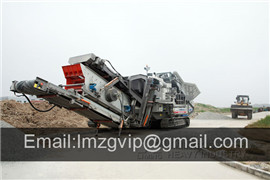
Top 10 tips to improve the grinding efficiency of ball mill
For example, heating the minerals in the ore to change the mechanical properties of the ore Reduce hardness, etc. 2. More crushing and less grinding, reducing
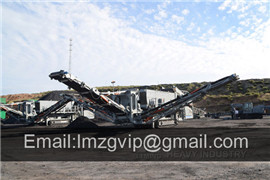
10 Ways to Improve the Grinding Efficiency of Your Ball Mill
Here are the 10 ways for your to improve the ball mill performance: Step#1. Change the original grindability. Step#2. More crushing and less grinding to
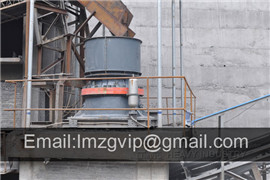
Ball Mill: Is the Grinding Fineness the Finer, the Better?
In the entire beneficiation process of a concentrator, grinding operation cost accounts for a considerable proportion. The grinding fitness is one of the main
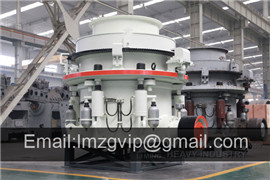
A review on micromilling: recent advances and future trends
Recently, mechanical micromilling is one of the most promising micromanufacturing processes for productive and accurate complexfeature generation in various materials including metals, ceramics, polymers and composites. The micromilling technology is widely adapted already in many hightech industrial sectors; however, its
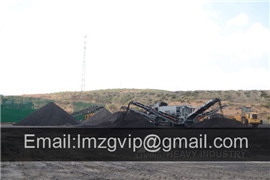
Machines Free FullText Hard Milling Process Based on
An important achievement is the knowledge of the efficiency of compressed cold air cooling for hard milling with the resulting lowest average flank wear of 0.05 mm, average surface roughness of 0.28 µm, which corresponds to grinding procedure roughness classes of N4 and N5, and average tool durability increase of 26% compared
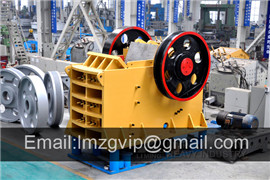
The Effect of Grinding Media on Mineral Breakage
The breakage and liberation of minerals are the key to fluidized mining for minerals. In the ball milling process, steel balls function as not only a grinding action implementer but also energy carrier to determine the breakage behavior of ores and the production capacity of the mill. When ground products present a much coarse or much
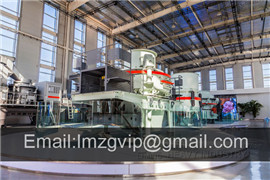
Grinding Solutions to Improve Production Strategies and
Grinding mill liners are subjected to severe impact and high abrasion. They must be manufactured using the best technologies and designs for superior strength and durability. ME Elecmetal's liner designs and materials are developed to deliver maximum wear life and throughput in both highimpact and highabrasion applications, regardless
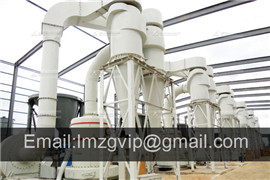
Improve your milling production strategies & productivity
Grinding Solutions to Improve your Production Strategies and Productivity Goals ME Elecmetal provides customized solutions according to the unique challenges and requirements
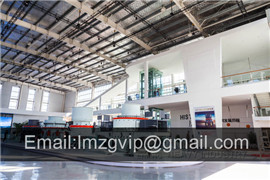
Milling vs Grinding: What’s the Difference?
In Conclusion. While they both involve the physical removal of material from a workpiece, milling and grinding aren’t the same. The former machining process is characterized by the use of a milling
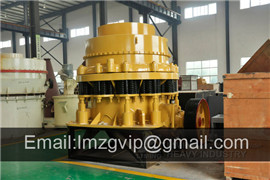
10 Ways to Improve the Grinding Efficiency of Your Ball Mill
Here are the 10 ways for your to improve the ball mill performance: Step#1. Change the original grindability. Step#2. More crushing and less grinding to reduce the feed size into mill. Step#3. Reasonable filling rate of steel ball. Step#4. Reasonable size and proportion of steel ball.
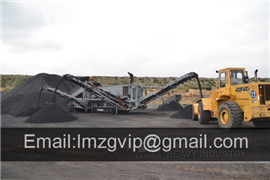
Grinding, crushing Safe Food Factory
A whole range of grinding/milling techniques and equipment are available for application with different types of food. Grinding/milling can be carried out dry or wet. In wet grinding/milling smaller particle sizes can be attained. Often dry grinding (milling) is combined with sieving or air classification, this results in particle size
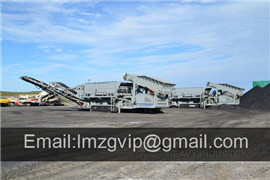
How to improve the quality and milling effect of wheat flour?
The commonly used grinding equipment is a roller mill. The auxiliary grinding equipment includes an impact mill and a loose powder machine. Flour Milling Theory Brief Introduction Grinding and sieving milling method mainly uses the difference in the strength of wheat endosperm and cortex to separate the cortex from the endosperm.
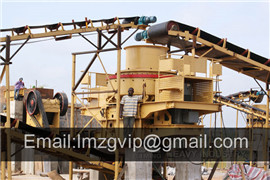
US Patent for Device for grinding or milling and method
The aim of the invention is to improve the sealing of a device for grinding or milling material to be ground. To this end, the invention relates to a device (1) and to the method for sealing particularly such a device (1). According to the invention, the seal (10) of the device (1) includes the sealing ring (11) which radially surrounds the drive shaft (6) and the cutting
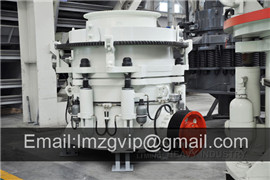
Machines Free FullText Hard Milling Process Based on
An important achievement is the knowledge of the efficiency of compressed cold air cooling for hard milling with the resulting lowest average flank wear of 0.05 mm, average surface roughness of 0.28 µm, which corresponds to grinding procedure roughness classes of N4 and N5, and average tool durability increase of 26% compared
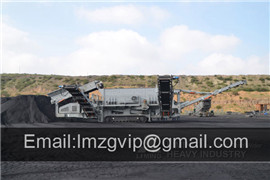
A review on micromilling: recent advances and future trends
Micromilling is a precise and flexible technology to manufacture complex 3D geometries in various types of materials (metals and its alloys, polymers, ceramics, graphite, composites etc. [3, 26,27,28,29,30,31,32,33,34,35,36,37,38]) by relatively high material removal rates.The kinematic of micromilling is similar to the conventionalsized
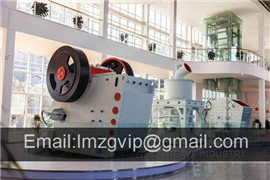
How Advanced Grinding Technology Leverages
Its ability to perform grinding operations as well as milling and drilling in a single clamping can lead to improved accuracy and faster cycle times compared to multiple setups on standalone machines. However, Wiss is quick to point out that it is still a grinding machine at its heart. Phil Wiss discusses the MFP30 combinedprocess grinding
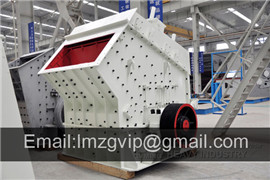
Grinding Solutions to Improve Production Strategies and
Grinding mill liners are subjected to severe impact and high abrasion. They must be manufactured using the best technologies and designs for superior strength and durability. ME Elecmetal's liner designs and materials are developed to deliver maximum wear life and throughput in both highimpact and highabrasion applications, regardless
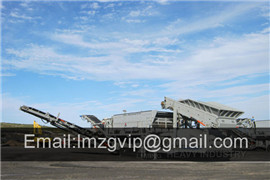
5 Grinding Considerations for Improving Surface Finish
Comparatively, a traditional milling or turning operation might achieve a finish of about 125 microinches to 32 microinches Ra. If the goal is to improve the current surface finish from 20 microinch Ra to 17 microinch Ra, then simply increasing the wheel speed and/or reducing the feed rate slightly might be sufficient.
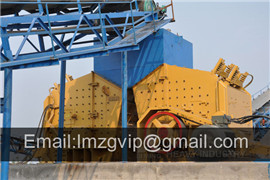
Top 10 tips to improve the grinding efficiency of ball mill
For example, heating the minerals in the ore to change the mechanical properties of the ore Reduce hardness, etc. 2. More crushing and less grinding, reducing the particle size. The larger the grinding size, the more work the mill needs to do to the ore. To achieve the required grinding fineness, the workload of the ball mill will inevitably
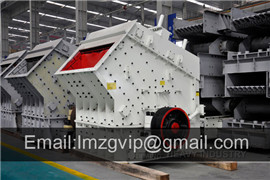
Six factors affecting the output of grinding mill DC Velocity
In short, we can learn more easily to improve the output of the mill after understanding the influencing factors. 1. Particle size of finished product. The fineness of the material after grinding by the mill requires high fineness, that is, the finer the material is, the smaller the milling capacity of the grinding mill is.
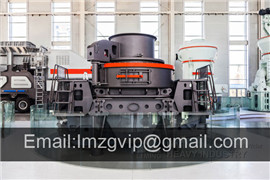
10 Ways to Improve the Grinding Efficiency of Your Ball Mill
Here are the 10 ways for your to improve the ball mill performance: Step#1. Change the original grindability. Step#2. More crushing and less grinding to reduce the feed size into mill. Step#3. Reasonable filling rate of steel ball. Step#4. Reasonable size and proportion of steel ball.
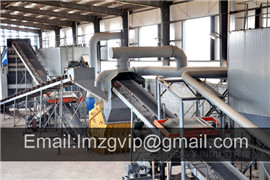
How to improve the quality and milling effect of wheat flour?
The commonly used grinding equipment is a roller mill. The auxiliary grinding equipment includes an impact mill and a loose powder machine. Flour Milling Theory Brief Introduction Grinding and sieving milling method mainly uses the difference in the strength of wheat endosperm and cortex to separate the cortex from the endosperm.
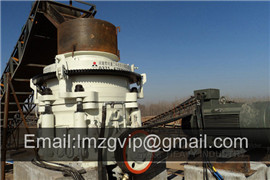
US Patent for Device for grinding or milling and method
The aim of the invention is to improve the sealing of a device for grinding or milling material to be ground. To this end, the invention relates to a device (1) and to the method for sealing particularly such a device (1). According to the invention, the seal (10) of the device (1) includes the sealing ring (11) which radially surrounds the drive shaft (6) and the cutting
- كسارات حجر الفك المصنعين في الصين
- الكرة اهتزازي طاحونة الموردين
- البوكسيت خام مصنع كسارة مخروط المحمول
- معدات مصنع تعدين التربة النادرة في العراق
- يمكن مطحنة الكرة طحن خام الحديد
- دستگاه سنگ زنی برای گرد و غبار تایر
- آلات تصنيع بلوك الجبس الإيطالية
- تركيز جاذبية الذهب في الوحل
- Spice Grinders And Mills
- سحق المطاحن الكوارتز بيع اليمن مستعمل
- كسارات صدمية متحركة للتأجير في مصر
- هاون طاحونة طاحونة من جهة ثانية
- سرویس تمیز کردن اگزوز خشک کن
- صناعة كسارات الحصى الذهبية
- وحدة طحن الأسمنت صغيرة الحجم
- rpm blower separator mesh 80
- مطحنة الكرة للبيع والاسعار في العراق
- mini ball mill machinery price in ethiopia
- stone crushing machines germany
- مصنع اسمنت لافارج في مصر