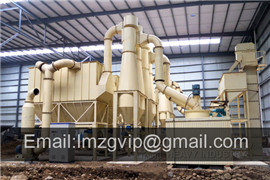
Raw Material DryingGrinding Cement Plant Optimization
Grinding Operation Objectives and KPIs: Highly energy intensive unit operation of size reduction in cement industry is intended to provide a homogeneous, dry (<0.5%
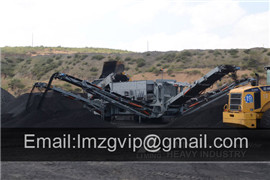
Cement Plant, Cement Equipment Cement Plant
Our Production Equipment. AGICO Cement is a cement plant manufacturer with production capacity of 30,000 tons of equipments and structure parts and 20,000 tons of
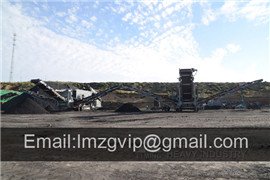
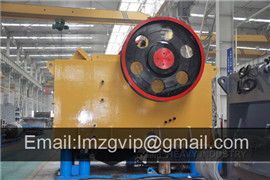
Raw Mill, Cement Raw Mill, Raw Mill In Cement Plant
Low investment: the vertical raw mill set crushing, drying, grinding, grading transportation in one, simple system, compact layout, less space, it also can be arranged
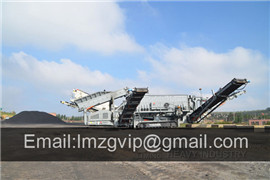
Vertical Roller Mill Operation in Cement Plant
The vertical roller mill (VRM) is a type of grinding machine for raw material processing and cement grinding in the cement manufacturing process.In recent years, the VRM cement
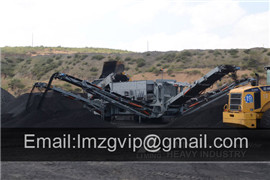
Cement Manufacturing Process: 6 StepsTo Make
6 steps of the cement manufacturing process. When we talked about the manufacturing of cement, anyone who knows the cement manufacturing process slightly will mention “two grinding and one
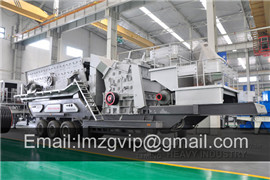
Cement Raw Mill in Cement Plant for Cement Raw Meal
Raw mill is mainly used for grinding cement raw meal in the cement factory production process. It is also suitable for metallurgical, chemical, electric power and other industrial
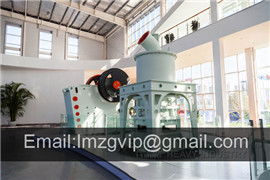
Cement Plant Cement Manufacturing Plant EPC Project
The cement manufacturing plant can be divided into five steps: Crushing & prehomogenization: cement crusher crush limestone and other materials and stacker and
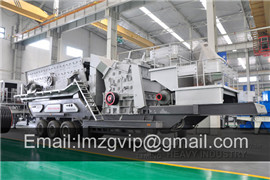
CEMENT MANUFACTURING PROCESS: RAW GRINDING
Today we are going to start here one very important topic i.e. Process technology of cement manufacturing: Raw grinding plant. We will understand the various
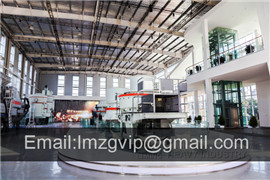
BASIC CEMENT PLANT LAYOUT Process
CHAENG holds deep domain knowledge of the industry and hence, is equipped to offer customized service that are directed to meet the needs of clients from cement plants. Cement production line includes
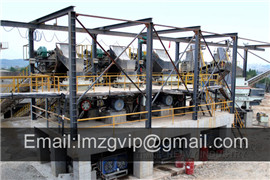
The Green Cement Plant Of The Near Future World Cement
The equipment might look the same, but quality control will be vastly refined thanks to the use of software programmes like QCX/BlendExpert™ Pile and Mill, which help cement plant operators gain greater control over their raw mill feed. 3D modelling and fast, precise analysis provides the greatest possible insight into stockpile composition
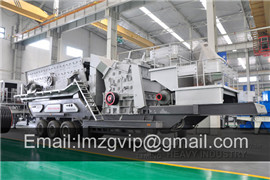
Cement Mill Cement Grinding Machine AGICO Cement
The cement grinding mill in a cement plant mainly includes cement vertical mill, cement ball mill, ultra fine grinding mill, cement roller press, etc. They are suitable for both wet process and dry process. AGICO offers EPC cement projects and different kinds of equipment needed for cement plant, such as a series of cement mills: cement ball
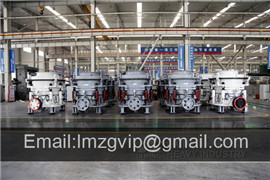
Vertical Roller Mill Operation in Cement Plant
The vertical roller mill (VRM) is a type of grinding machine for raw material processing and cement grinding in the cement manufacturing process.In recent years, the VRM cement mill has been equipped in more and more cement plants around the world because of its features like high energy efficiency, low pollutant generation, small floor area, etc.. The
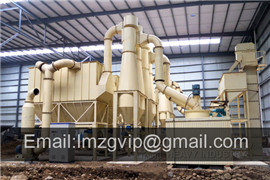
Low carbon measures for cement plant a review typeset.io
Cement manufacturing is an energy and carbonintensive industry. The cement industry contributes approximately 5% of the global manmade carbon dioxide (CO2) emissions and is thus becoming the second largest CO2 contributor in industry after power plants. A wide range of options are available to considerably reduce CO2 emissions. This
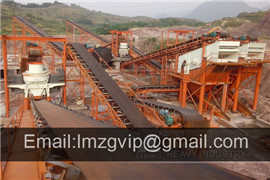
Raw Meal Ball Mill gwmcn
Raw Meal Ball Mill is mainly used in grinding raw materials and final products in cement plant. It is also suitable for grinding various ores and other materials in the metallurgy, mine, chemical, construction and other industries. Suitable enterprise type: cement plant Output:21~210t/h Effective volume:29.5~185 m3
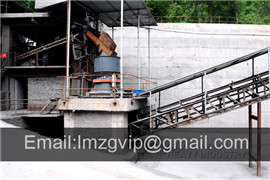
Cement plant design under EPC contract esfccompany
Our team offers financing and engineering design for cement plants around the world, helping companies implement innovative technical solutions.
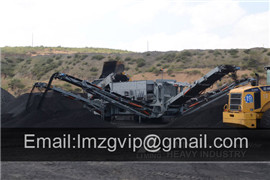
(PDF) Environmental Pollution by Cement
Moreover, in the cement industry, various operations like handling of raw material, crushing of limestone, processing in kilns, manufacturing, and storage of clinker, grinding of finished cement
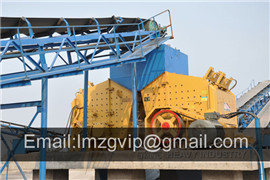
(PDF) THE CEMENT MANUFACTURING PROCESS
They are mixed either dry (dry mixing) or by water (wet mixing). 3) Prepared raw mix is fed into the rotary kiln. 4) As the materials pass through the kiln their temperature is rised upto 13001600 °C. The process of heating is named as “burning”. The output is known as “clinker” which is 0.155 cm in diameter. 5) Clinker is cooled
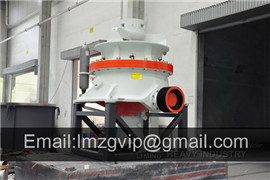
BASIC CEMENT PLANT LAYOUT Process
CHAENG holds deep domain knowledge of the industry and hence, is equipped to offer customized service that are directed to meet the needs of clients from cement plants. Cement production line includes
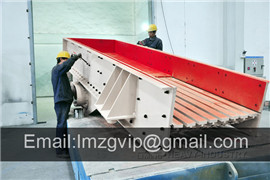
Oman Cement increases ninemonth profit by 3.7% in
North America: Germanybased Schenck Process has awarded a contract for the supply of “fitting connectors, spigots and bulk bag loaders to one of its North American plants” to original equipment manufacturing (OEM) company BFM Global. It says it will integrate BFM Global products in pneumatic conveying, dust collection, weighing and
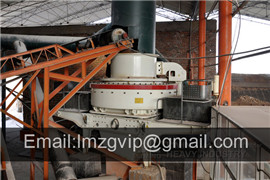
Raw Meal Ball Mill gwmcn
Raw Meal Ball Mill is mainly used in grinding raw materials and final products in cement plant. It is also suitable for grinding various ores and other materials in the metallurgy, mine, chemical, construction and other industries. Suitable enterprise type: cement plant Output:21~210t/h Effective volume:29.5~185 m3
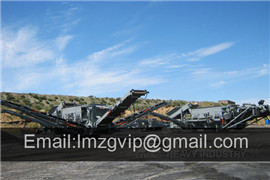
Vertical Raw Mill for Cement Raw Meal Grinding in
Vertical Raw Mill. Feeding size: 35110mm. Capacity: 12350t/h. Motor power: 2553600kW. Applications: It can be used for grinding limestone, gypsum, siliceous, coal and other materials. It is mainly used in cement raw materials grinding section of cement factory, and also be used in concrete and mineral fields. Email: info@ballmillssupplier.
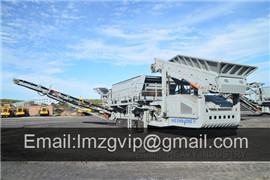
Cement plant design under EPC contract esfccompany
Our team offers financing and engineering design for cement plants around the world, helping companies implement innovative technical solutions.
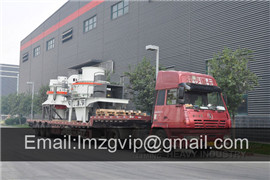
Cement Analysis IEA
The direct CO 2 intensity of cement production increased about 1.5% per year during . In contrast, 3% annual declines to 2030 are necessary to get on track with the Net Zero Emissions by 2050 Scenario. Sharper focus is needed in two key areas: reducing the clinkertocement ratio (including through greater uptake of blended cements) and
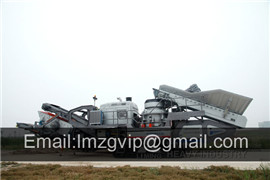
Low carbon measures for cement plant a review typeset.io
Cement manufacturing is an energy and carbonintensive industry. The cement industry contributes approximately 5% of the global manmade carbon dioxide (CO2) emissions and is thus becoming the second largest CO2 contributor in industry after power plants. A wide range of options are available to considerably reduce CO2 emissions. This
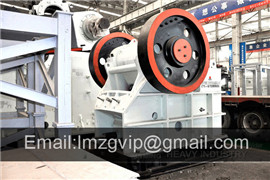
(PDF) THE CEMENT MANUFACTURING PROCESS
They are mixed either dry (dry mixing) or by water (wet mixing). 3) Prepared raw mix is fed into the rotary kiln. 4) As the materials pass through the kiln their temperature is rised upto 13001600 °C. The process of heating is named as “burning”. The output is known as “clinker” which is 0.155 cm in diameter. 5) Clinker is cooled
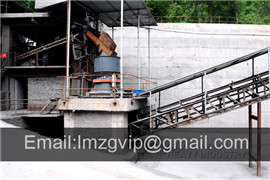
BASIC CEMENT PLANT LAYOUT Process
CHAENG holds deep domain knowledge of the industry and hence, is equipped to offer customized service that are directed to meet the needs of clients from cement plants. Cement production line includes
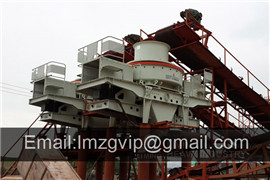
Production Process Home Cement
Stage 8. Cement Grinding (with Gypsum & additives) Stage 9. Packing Dispatch. Cement manufacturing process can classified in to two types in thermal operation as wet process and dry process. Palavi process operation is designed in dry process manufacturing which is most widely used method in the world was established in 1969 as state cement
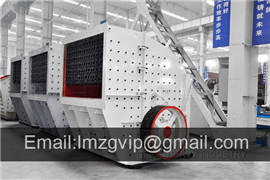
Oman Cement increases ninemonth profit by 3.7% in
North America: Germanybased Schenck Process has awarded a contract for the supply of “fitting connectors, spigots and bulk bag loaders to one of its North American plants” to original equipment manufacturing (OEM) company BFM Global. It says it will integrate BFM Global products in pneumatic conveying, dust collection, weighing and
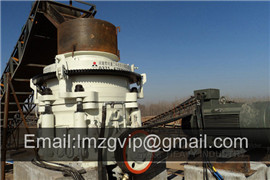
REDUCCIÓN DE CO2 EN LA INDUSTRIA CEMENTERA POR
This article shows an initial review of the research developed around manufacturing pure calcium silicate phases of Portland cement, Alite and Belite, through alternative methods of synthesis. Portland cement is the most successful material in the last few years and so far not clearly identify a material that can replace it. In 2012 world
- بيع معدات محاجر تعدين الحديد
- تعدين الحجر الجيري أمبير ألواح رصف الكوارتز
- معدات كسارة الحجر الأجنبية في دلهي
- Abrasive Wheels 3x1xgrit Black United States Made
- تركيز الجاذبية الذهب الرسم البياني مصنع
- Shaking Tables And Particle Size Distribution
- فاصل مغناطيسي جاف لخام المنغنيز من زمبابوي
- مصنع خلية التعويم بيو سلسلة
- شركات التعدين انسواز ايلاند
- فلو شیت فرآوری سنگ آهن در ایران
- نظرية التجارة الآلية iti pdf
- موردي آلة تصنيع الأسمنت المسحوق
- تستخدم كسارات الحجر اليابان
- وظائف مشرف معدات البناء في أفريقيا
- muncie m22 rock crusher mobile jaw crusher
- مطحنة الكرة الأسمنتية الأنبوب الفرن الدوار
- موقع شركة بن قريعة للمعدات الثقيلة
- پیمانکاران سنگ شکن مخروطی در مصر
- كسارة مثل محطة تكسير الفحم
- concrete jaw crusher price in nigeria