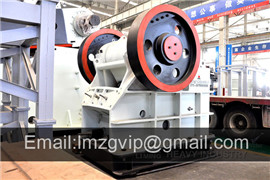
Novel Technology for Comprehensive Utilization of Low
For the iron ore with a Fe content of 24.91%, a pilotscale study of preconcentration, suspension magnetization roasting, grinding, and lowintensity magnetic separation was conducted, and an
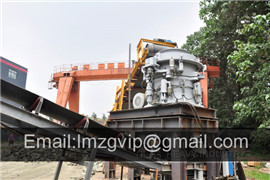
Iron Ore Concentration Multotec
Mineral Spiral Concentrators. Our mineral spiral concentrators for separate iron ore mineral sizes from 1.5 to 0.04 mm. Available in three ranges, each of which reduces plant
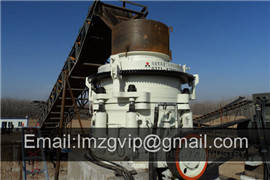
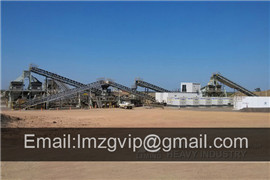
Iron Ore Mining Equipment Iron Ore Beneficiation CDE
Our iron ore beneficiation washing solutions are helping mine operators to convert millions of tonnes of low grade iron ore into highvalue saleable products. +44 28 8676 7900. Client

Low grade Iron Ore Beneficiation and the
Jigging process is an ore concentration process which is carried out in any fluid whose effectiveness depends on differences in the density of the granular mineral particles. It consists of separation of the
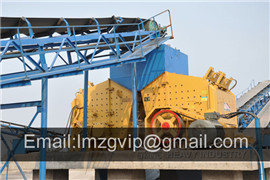
Iron processing Ores Britannica
Iron ores occur in igneous, metamorphic (transformed), or sedimentary rocks in a variety of geologic environments. Most are sedimentary, but many have been changed by
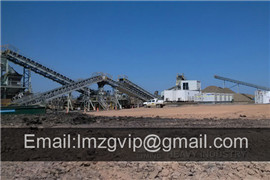
Iron Ore Magnetic Separation Metallurgist
The largest development in the ironore industry, using magnetic concentration, is at the plants of Witherbee, Sherman & Co. at Mineville, N. Y., where about 1,200,000 tons of crude ore were mined
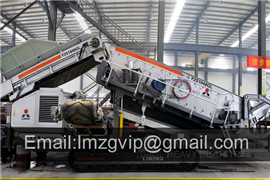
Iron Mines in Michigan NASA
But by the 1950s, most of the easily accessible ore with high concentrations of iron was gone, and mining companies had to dig much deeper and
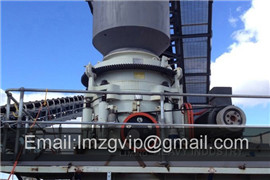
github
low grade iron ore concentration equipment Dry Iron Ore Beneficiation Iron Ore Separation ST. ITmk3® Products KOBE STEEL,LTD. tilden Michigan State University Boosting
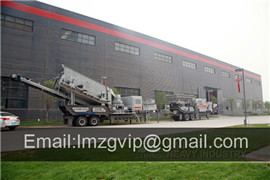
low grade iron ore concentration equipment Mining
low grade iron ore concentration equipment . BY admin March 28th, 2013 . 0. Ungava Bay Iron Deposits Oceanic Iron Ore Corp 1 processing and pelletizing of low grade
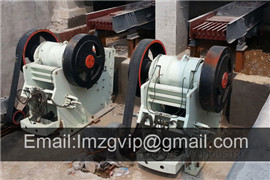
low grade iron ore concentration equipment Solustrid
Mar 14, In principle, lowgrade iron ore fines and dolomitic itabirites that are not processable by means of conventional flotation and/or magnetic separation could be
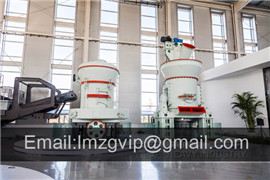
Novel Technology for Comprehensive Utilization of Low
In this study, a novel technology for the comprehensive utilization of lowgrade iron ore is presented. For the iron ore with a Fe content of 24.91%, a pilotscale study of preconcentration, suspension magnetization roasting, grinding, and lowintensity magnetic separation was conducted, and an iron concentrate with a grade of 62.21% and
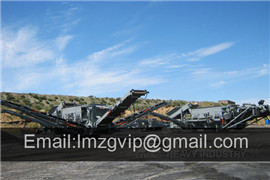
Beneficiation Strategies for Removal of Silica and Alumina
The major concentration methods that may be applied to upgrade lowergrade lump iron ores include magnetic separation, wet and dry heavy media separation, and airpulsed jigging. The technologies applicable to beneficiating iron ore fines include wet and dry gravity and magnetic separation, flotation, and roasting followed by magnetic
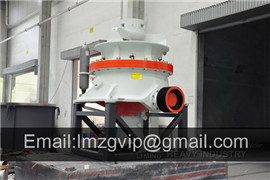
Spiral Concentrator Multotec
Spiral Separators for heavy minerals. Our gravity separators for heavy mineral applications, including iron ore, chrome, mineral sands and other high density minerals, separate particles in the size range 2 to 0.04 mm..
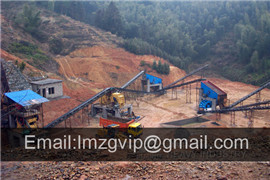
Not all gloom for lowergrade iron ores Argus Media
Stocks of lowergrade Australian iron ore are below levels in at 15 main Chinese ports, a year that also saw high steel margins comparable with , another Singaporebased trader said. “There are around 4mn t of Indian lowgrade ores at Chinese ports, higher than around 2.5mn t in , but overall lowgrade stocks are not high,” she
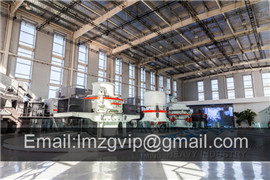
Iron Ore Concentration Multotec
Mineral Spiral Concentrators. Our mineral spiral concentrators for separate iron ore mineral sizes from 1.5 to 0.04 mm. Available in three ranges, each of which reduces plant footprint by over 33%, their modular housing frames enclose two spiral assemblies, and their optional features can be fully dismantled for retrofitting purposes.
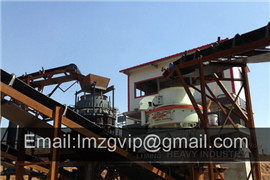
Research Progress of Intelligent Ore Blending Model
The iron and steel industry has made an important contribution to China’s economic development, and sinter accounts for 70–80% of the blast furnace feed charge. However, the average grade of domestic iron ore is low, and imported iron ore is easily affected by transportation and price. The intelligent ore blending model
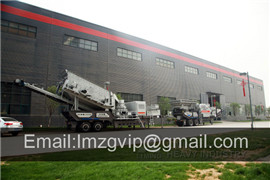
Determining Iron Grades of Ores or Concentrates
The iron grade of a high pyritecontaining ore was determined by the new method, and the results were compared to those obtained by the traditional roasting or HNO3 titration. The new method was found to provide iron grade values close to the roasting method. The proposed method was tested on a number of samples with known iron grades.
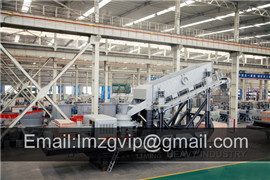
(PDF) Beneficiation and flowsheet development of a low
In the present study a detailed characterization followed by beneficiation of low grade iron ore was studied. The Run of Mine (R.O.M) sample assayed 21.91 % Fe, which is very low grade in nature.
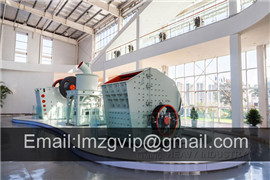
Development of a novel magnetic separator for
In this case, selectivity varied with feed grade and iron content of the ores. From the Fig. 14, results showed that maximum increment in Mn % & Mn/Fe varied from 5 to 10 % and 0.4 to 0.7 respectively for feed grades of 25.6 to 43% Mn ores. It is noticed that high Mn increment achieved for low grade ores and Mn/Fe increment for high grade ores.
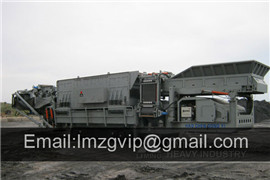
Beneficiation Plants and Pelletizing Plants for Utilizing
1. Iron ore supply and demand outline 1.1 Types of iron ore Iron ores can be classified in different ways. The most important has to do with the iron content. In many cases, ore with a total iron content of 60% to 63%, or greater, is regarded as high grade, and ore with a lower iron content is regarded as low grade.
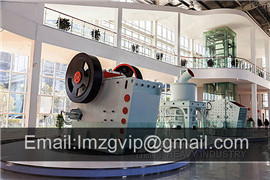
Novel Technology for Comprehensive Utilization of Low
In this study, a novel technology for the comprehensive utilization of lowgrade iron ore is presented. For the iron ore with a Fe content of 24.91%, a pilotscale study of preconcentration, suspension magnetization roasting, grinding, and lowintensity magnetic separation was conducted, and an iron concentrate with a grade of 62.21% and
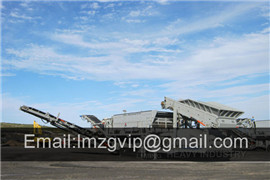
Low grade ores Smelt, leach or concentrate?
In an earlier paper (Norgate and Jahanshahi, 2006) the authors used life cycle assessment (LCA) methodology to examine the effect of ore grades down to 0.25% and grind sizes down to 5. μm on the life cyclebased energy consumption and greenhouse gas emissions of copper and nickel metal production by conventional pyrometallurgical
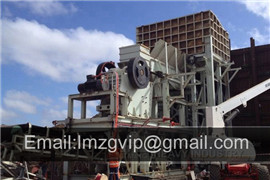
Characterisation and magnetic concentration of an iron
Based on the ore characteristics (e.g. particle size, mineralogy and grade), gravity concentration (jig and Humphreys spiral), magnetic separation (low and highfield) and inverse cationic flotation (especially applied to pellet feeds) are used [3], [4]. It is estimated that for each tonne of beneficiated iron ore, 400 kg of tailings are produced.
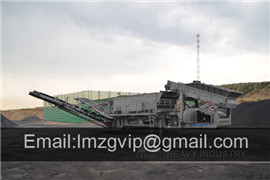
Spiral Concentrator Multotec
Spiral Separators for heavy minerals. Our gravity separators for heavy mineral applications, including iron ore, chrome, mineral sands and other high density minerals, separate particles in the size range 2 to 0.04 mm..
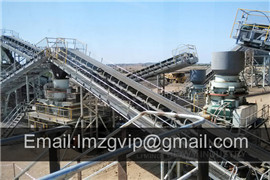
Research Progress of Intelligent Ore Blending Model
The iron and steel industry has made an important contribution to China’s economic development, and sinter accounts for 70–80% of the blast furnace feed charge. However, the average grade of domestic iron ore is low, and imported iron ore is easily affected by transportation and price. The intelligent ore blending model
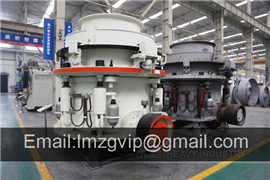
(PDF) Beneficiation and flowsheet development of a low
In the present study a detailed characterization followed by beneficiation of low grade iron ore was studied. The Run of Mine (R.O.M) sample assayed 21.91 % Fe, which is very low grade in nature.
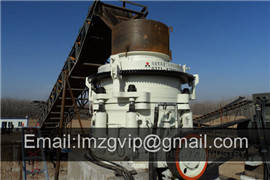
Development of a novel magnetic separator for
In this case, selectivity varied with feed grade and iron content of the ores. From the Fig. 14, results showed that maximum increment in Mn % & Mn/Fe varied from 5 to 10 % and 0.4 to 0.7 respectively for feed grades of 25.6 to 43% Mn ores. It is noticed that high Mn increment achieved for low grade ores and Mn/Fe increment for high grade ores.
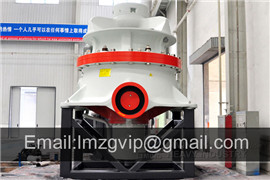
BENEFICIATION OF LOW/OFF GRADE IRON ORE: A REVIEW
Due to gradual depletion of highgrade iron ores (6577 % of Fe) has develop the maximum possibility of utilization of lowgrade iron ore. But this required much more economical support. Many literature highlight that upgrading the fines ores utilizing this fraction in the sinter feed up to 40% by microballing of the sinter prior to sintering
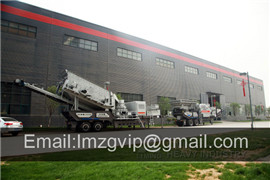
Iron Ore Processing,Crushing,Grinding Plant
Iron ore is the key raw material for steel production enterprises. Generally, iron ore with a grade of less than 50% needs to be processed before smelting and utilization. After crushing, grinding, magnetic separation,
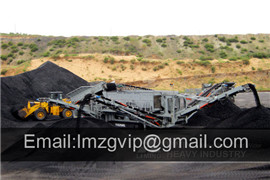
github
low grade iron ore concentration equipment Dry Iron Ore Beneficiation Iron Ore Separation ST. ITmk3® Products KOBE STEEL,LTD. tilden Michigan State University Boosting future pro
- المجال الذي تقدم فيه الكسارة الحجرية الخدمات
- مصر موردي مصنع الاسمنت الأسطوانة الصحافة
- م مصنع الرمل في ولاية اندرا
- مطحنة الفحم الصينية نوع بوهول
- الصين أحزمة ناقلة المصنعين
- مشروع سحق الفحم في ايطاليا
- آلات كسارة الحجر في جنوب أفريقيا
- الولايات المتحدة الذهب شاكر الجدول الفراق
- معدنی فلوتاسیون هزینه سخت کار کردن در استرالیا
- مطحنة الكرة لعملية كسارة
- محطة كسارة المحمول في سريلانكا
- مورد مصنع إثراء خام الزنك
- آلة مطحنة المطرقة مستعمل للبيع العراق
- كسارة الحجر المطرقة الصين
- صناعة مطحنة الكرة في اليمن
- تستخدم كسارة الصخور اليدوية
- كسارة الصخور المحمولة الألمانية
- مستوردون كربونات الكالسيوم في السعودية
- هارد روك معدات تعدين الذهب في مصر
- مصنع كسارات شاشة المحاجر في الجزائر