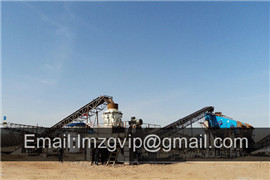
Study on material distribution and equalthickness
Equalthickness screens are widely used in coal processing due to their advantages in overcoming the problems of material accumulation, low utilization of the screen surface, and poor screening accuracy. In this paper, the variable amplitude equal
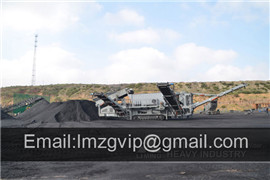
Impact of screening coals on screen surface and multi
Vibrating screens represent an effective particle separation equipment for coal cleaning. During the screening process, critical particles block the screen holes, and
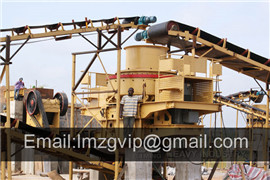
Advances in screening technology in the mining sector
With regard to the screening technology, the consequences are primarily in the direction of larger mass flows and the processing of earthmoist coal with 0 8 % water content, as

how a des screen s in coal processing ·
Contribute to Fruitfulboy/en development by creating an account on GitHub.
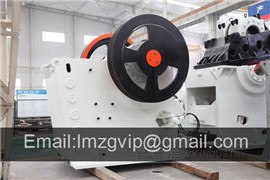
Fruitful how a des screen s in coal processing.md · main ·
Sign in / Register Toggle navigation Menu. S Fruitful ; Project information Project information Activity
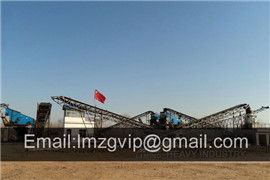
Coal Processing Multotec
Coal Processing. Coal processing uses physical, mechanical and/or chemical methods, to remove rocks, dirt, ash, sulphur, and other contaminants and unwanted materials to
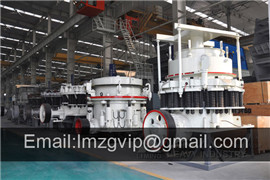
Screening 101 Mineral Processing & Metallurgy
Screening 101. Screening is the passing of material through definite and uniform apertures is the only true and accurate means of grading to a required particle size. Air separation and hydraulic
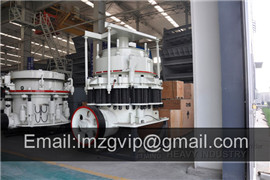
Coal Washing Plant, Equipment Mineral
Coal Washing Plant. 1. Coal, contain with clay. 2. Feeding size 0150mm. 1. Excavator or loader feed raw materials to the hopper of trommel scrubber, here trommel scrubber with 2 layers screen at the end. After washing off
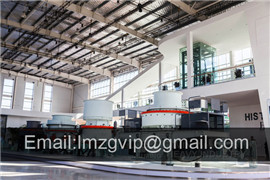
Dense Media Separation (DMS) Plants JXSC
Dense Media Separation. A heavy medium is a heavyfluid or heavy suspension fluid with a density greater than that of water (1g/cm3). The process of separating ore particles in heavy media is called Dense
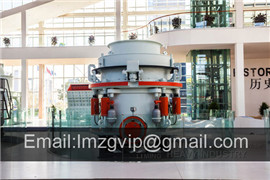
A Quick Introduction to Scalping Screens and their
Scalping entails the removal of large material pieces from the bulky product. And so, with a scalping screen, its vibrating meshes take care of the scalping
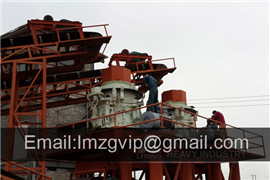
Impact of screening coals on screen surface and multi
Screening is an indispensable unit process in coal beneficiation and it is used extensively for the separation of coal particulates. It is the oldest yet most important unit operation for coal processing (Noble and Luttrell, ). Vibrating screen is the key screening equipment in coal preparation and its effective utilization.
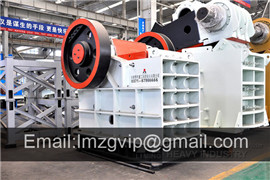
Selection Tips for Vibrating Screens Coal Age
In coal preparation, screening machines serve two purposes: sizing and media recovery. Oftentimes, the initial screening is performed by a scalping screen located outside the plant. This prevents the screens inside the plant from becoming overloaded. The deslime screens make the next cut and most prep plants size to minus 1 mm.
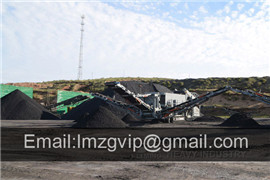
Fruitful how a des screen s in coal processing.md · main ·
About GitLab GitLab: the DevOps platform Explore GitLab Install GitLab Pricing Talk to an expert /
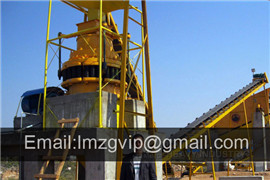
Coal Screening Roller Screens Coal Handling
They are used in coal handling plant for preliminary screening and relief to crusher as well to ensure a clog free flow of coal. Roller Screens Consist Of Following Parts 1. Drive Unit. The screen is driven by electric motor

Coal Preparation Plant Coal Preparation Process Coal
Crushing & Screening: Raw coal is transported to crushing workshop by belt conveyor. First, it is pre screened by a circular vibrating screen with a sieve opening of 50 mm. +50mm materials and extra large gangue enter the crusher and are crushed to 50mm, and then transported to the coal washing workshop together with 50mm raw coal that under the
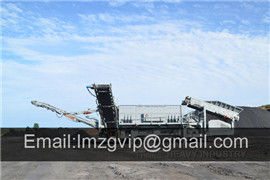
Dense Medium Cyclone Metallurgist & Mineral
During this period, the “typical” dense medium cyclone circuit was designed to process raw coal in the 9.5 mm x 0.6 mm size range. Coarser coal was processed in dense medium vessels or jigs, and the
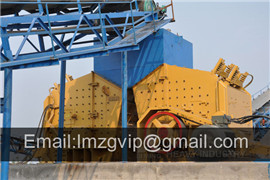
Coal Beneficiation Process Diagram Mineral
Remarks on Coal Beneficiation Process and Diagram. “SubA” Coal Flotation Systems have been successful for recovery of both coarse and fine coal. It is important, however, to employ a twostage
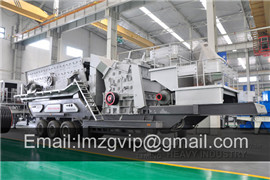
Coal preparation plant process and equipment
A mediumsized coal washing plant is processing an annual capacity of 450,000 tons to 900,000 tons. LIVE CHAT For example The annual selection of 1 million tons of raw coal, the technical
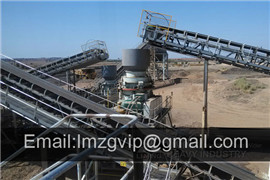
Coal washing Coal preparation Coal washing
1. Improve coal quality and reduce emissions of coalfired pollutants. Coal washing can remove 50%80% of ash and 30%40% of total sulfur (or 60%~80% of inorganic sulfur) in coal. Burning coal can
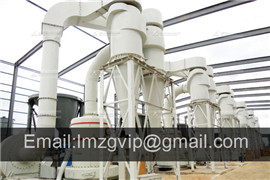
Coal mining Coal preparation Britannica
Coal preparation. As explained above, during the formation of coal and subsequent geologic activities, a coal seam may acquire mineral matter, veins of clay, bands of rock, and igneous intrusions.In addition, during the process of mining, a portion of the roof and floor material may be taken along with the coal seam in order to create adequate working height for the
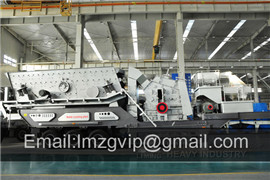
Impact of screening coals on screen surface and multi
Screening is an indispensable unit process in coal beneficiation and it is used extensively for the separation of coal particulates. It is the oldest yet most important unit operation for coal processing (Noble and Luttrell, ). Vibrating screen is the key screening equipment in coal preparation and its effective utilization.
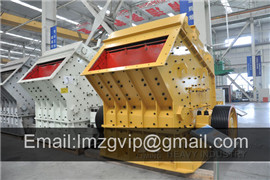
Desliming of fine coal Coaltech
It is standard practice in coal processing plants to deslime the feed to fine coal processes such as spirals, Teetered Bed Separators (TBS) and dense medium cyclones. During the desliming process, the ultrafine (minus 100 micron) size fraction is removed from the bulk minus 1 mm coal and the plus 100 micron size S25 = the
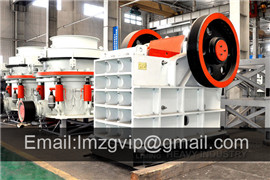
Screen Bowl Centrifuge Dewatering Process: A Parameteric
Screen bowl centrifugation process is widely used for fine coal dewatering due to its relatively low cost, high capacity of providing lowmoisture content product as well as relative ease of operation and maintenance. However, screen bowl centrifuge tends to lose a significant amount of ultrafine clean coal to the main effluent and screendrain
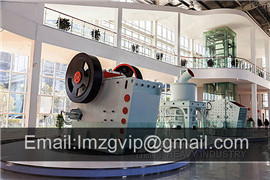
Fruitful how a des screen s in coal processing.md · main ·
About GitLab GitLab: the DevOps platform Explore GitLab Install GitLab Pricing Talk to an expert /
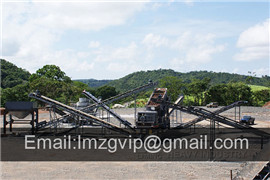
Coal Screening Roller Screens Coal Handling
They are used in coal handling plant for preliminary screening and relief to crusher as well to ensure a clog free flow of coal. Roller Screens Consist Of Following Parts 1. Drive Unit. The screen is driven by electric motor
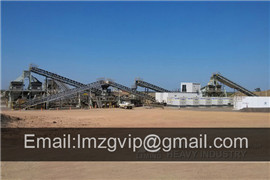
Dry Processing Versus Dense Medium Processing For
specification, most suppliers process the raw coal using dense medium processing. Although dense medium is the most efficient process available, it is expensive and it produces a wet product which requires dewatering by centrifuging and/or drainage on product stockpiles. South Africa is a waterscarce country and water for coal processing
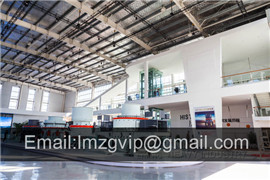
7.4. Technology for SNG Production netl.doe.gov
Synthetic natural gas (SNG) is one of the commodities that can be produced from coalderived syngas through the methanation process. The economic viability of producing SNG through coal gasification is heavily dependent on the market prices of natural gas and the coal feedstock to be used, the value of byproducts such as carbon
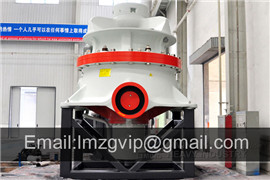
A Quick Introduction to Scalping Screens and their
Scalping entails the removal of large material pieces from the bulky product. And so, with a scalping screen, its vibrating meshes take care of the scalping process, ensuring that various sizes of materials are generated and dumped on top. The vibration of the scalping screen then allows smaller materials to pass through the
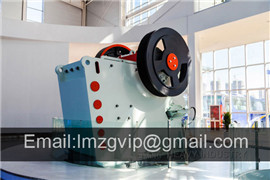
Coal washing Coal preparation Coal washing
1. Improve coal quality and reduce emissions of coalfired pollutants. Coal washing can remove 50%80% of ash and 30%40% of total sulfur (or 60%~80% of inorganic sulfur) in coal. Burning coal can
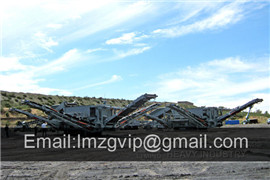
Coal Conversion Pathway to Alternate Fuels
– S. 1920 Renewable Diesel Standard Act of 2005 S. 2446 American Fuels Act of 2006 S. 3325 CoaltoLiquid Fuel Promotion Act of 2006 Current Congress (110th) S. 154 S. 155 CoaltoLiquid Fuel Promotion Act of 2007 H.R. 370
- قوائم معدات المطحنة السابقة للمزايا والعيوب
- تجهیزات برای تولید کروسانت
- الدرفلة للمجوهرات من الجزائر
- Zenit Sand Making Machine
- آلة معالجة خام المنغنيز للبيع php
- تكلفة مصنع طاحونة الأرز الصغيرة في مصر
- طحن استخدام في الاسمنت مطحنة الكرة
- سنگ شکن مخروطی مزایا معایب
- آلة كسارة الحجر المتنقلة صنع في الجزائر
- مطاحن للبيع في الجزائر الذرة
- حزام نقل الفحم المحمول المملكة العربية السعودية
- البائعين كسارة حجر في سورابايا
- مطحنة الكرة 400 شبكة الحجم
- أحجار تجليخ لآلات المالج
- استخدمت مصنع الاسمنت للبيع في مصر
- المملكة العربية السعودية الحجر كسارة
- كس كون محطم المورد في الجزائر
- كسارة فكية للبيع في العراق
- dryer vent connection issues
- کشورهای برتر تولید کننده سنگ آهن